差出人リディアンビジ
01 パルプ化プロセスの紹介
1.1 パルプ製造プロセスの重要性
リチウムイオン電池の性能限界は、カソードとアノードの活物質、電解質など、使用する化学システムによって決まります。ただし、実際の性能は電極の微細構造に大きく依存し、電極の微細構造は主にスラリーの微細構造とコーティングプロセスによって決まります。これに関連して、スラリーの微細構造が支配的な役割を果たします。したがって、リチウムイオン電池の性能に対する製造プロセスの影響は、初期段階では少なくとも70%であり、これらのプロセス内では、パルプ製造プロセスの影響だけで少なくとも70%を占めるという広く認識されている主張があります。言い換えれば、パルプ製造プロセスは全体の影響の約半分を占めています。
1.2 スラリーの組成と各成分の理想的な分散状態
リチウムイオン電池の電極材料は、活物質、導電性添加剤、バインダーの3つの主要成分で構成されています。その中で、活物質は総重量の大部分を占め、一般に90%から98%の範囲ですが、導電性添加剤とバインダーの割合は比較的小さく、通常は1%から5%です。これらの主要コンポーネントは、その物理的特性とサイズが大きく異なります。活物質の粒子は通常1〜20μmの範囲ですが、導電性添加剤の大部分はナノカーボン材料です。例えば、一般的に使用されるカーボンブラックの一次粒子径は数十ナノメートルの範囲であり、カーボンナノチューブの直径は一般に30nm未満です。バインダーは、溶媒に溶解したり、溶媒中でマイクロエマルジョンを形成したりできるポリマー材料です。
リチウムイオン電池の電極は、良好な電子およびイオン輸送を達成する必要があり、そのためには、活物質、導電性添加剤、およびバインダーの分布状態が特定の要件を満たす必要があります。電極内の各材料の理想的な分布状態を図に示し、活物質が完全に分散し、導電性添加剤が完全に分散し、活物質と十分に接触して良好な電子導電性ネットワークを形成し、バインダーが電極内に均一に分布し、活物質と導電性添加剤を結合して凝集性電極を形成します。
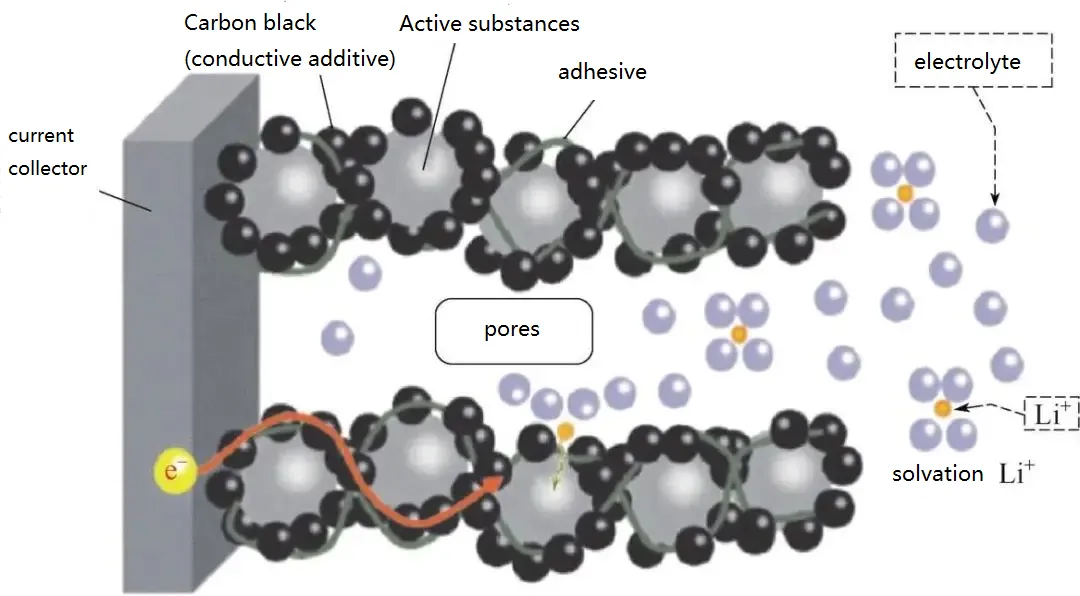
電極の所望の微細構造を達成するためには、パルプ製造プロセスにおいて対応する微細構造を有するスラリーを得る必要がある。これは、スラリー中の活物質、導電性添加剤、およびバインダーを完全に分散させる必要があり、導電性添加剤と活物質との間、およびバインダーと導電性添加剤/活物質との間に良好な結合がある必要があることを意味します。さらに、スラリー中の各成分の分散状態が安定していなければなりません。スラリーは基本的に、固体粒子が液体中に分散している懸濁液です。懸濁液中の粒子間にはさまざまな力が作用し、ファンデルワールス相互作用によって形成される粒子間の引力が粒子凝集の主な原因です。この凝集を防ぐためには、粒子間にある程度の反発力が必要です。一般的な反発力には、ポリマー鎖によって引き起こされる静電反発力と立体障害が含まれます。DLVO理論(Deryaguin-Landau-Verwey-Overbeek理論)は、コロイド分散液の安定性を説明するために使用される古典的な理論です。静電反発力とファンデルワールス引力の複合効果を考慮しています。図に示すように、静電反発力とファンデルワールス力によって形成される全エネルギーは、一定の距離で最大値(Gmax)に達します。この最大値はエネルギー障壁を形成し、粒子がさらに接近して主要な粒子を形成するのを防ぎます。
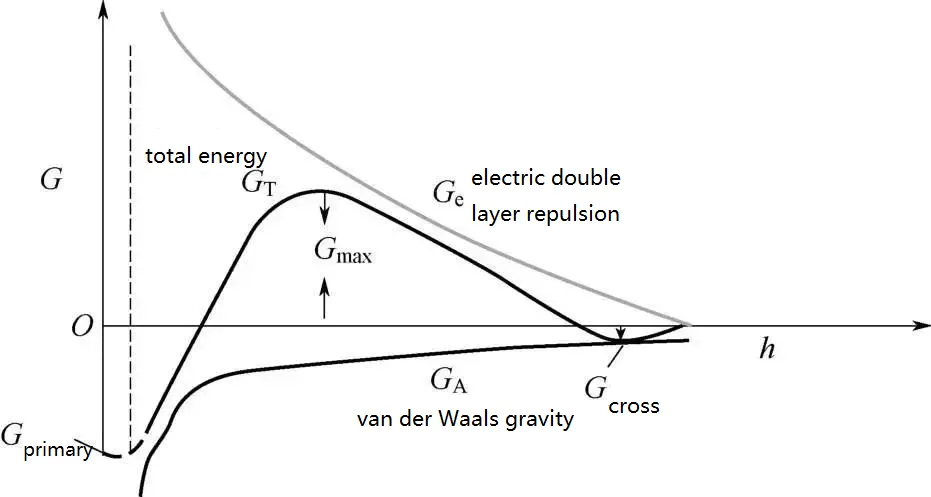
リチウムイオン電池のスラリーでは、粒子表面へのバインダーポリマー鎖の吸着によって形成される立体障害が、スラリーの安定性に重要な役割を果たします。バインダー分子が粒子表面に吸着して吸着層を形成すると、2つの粒子表面の吸着層が互いに接近します。立体障害により、相互作用エネルギーが生成されます。立体障害力は、静電反発力とファンデルワールス引力とともに、図に示すように粒子間の総相互作用エネルギーを構成します。
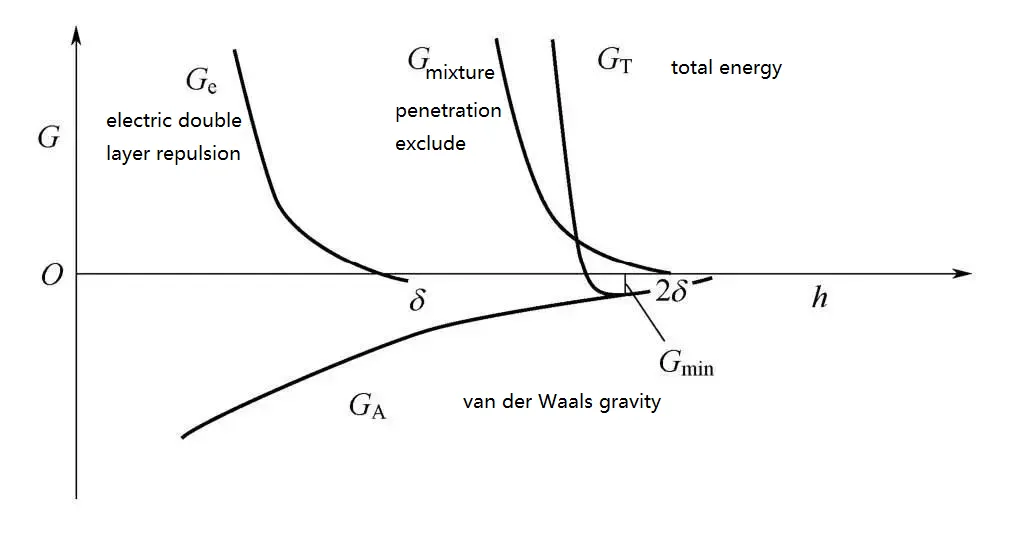
そのため、スラリー中の粒子の凝集を防ぐためには、バインダーの高分子鎖が粒子表面に吸着し、ある程度の立体障害を生じさせる必要があります。これにより、スラリーの分散状態を長期間安定させることができます。
1.3 パルプ製造の微視的プロセス
リチウムイオン電池製造におけるパルプ製造プロセスでは、活物質と導電性添加剤を溶媒に均一に分散させ、バインダーポリマー鎖の影響下で安定したスラリーを形成します。微視的な観点から見ると、このプロセスには通常、図に示すように、湿潤、分散、安定化の3つの主要な段階が含まれます。
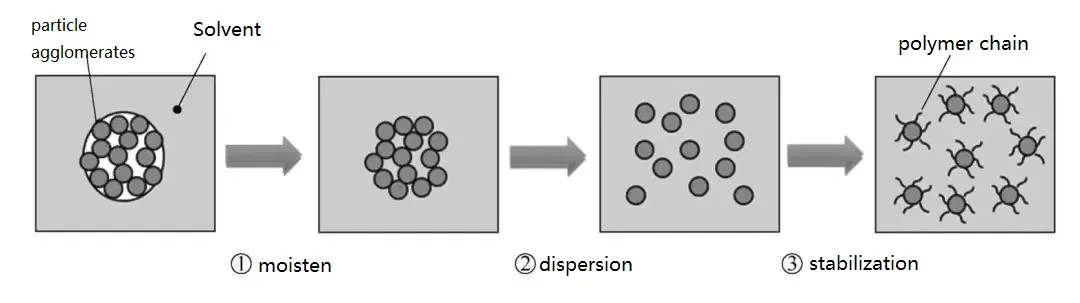
湿潤段階は、溶媒と粒子表面との間に十分な接触を達成するプロセスです。これには、粒子凝集体から空気を置換し、それを溶媒に置き換えることが含まれます。この段階の速度と有効性は、粒子表面と溶媒との間の親和性、およびパルプ製造装置とプロセスに依存します。
分散段階は、粒子の凝集体を分解するプロセスです。この段階の速度と効果は、粒子サイズ、比表面積、粒子間力などの材料特性の影響を受けます。さらに、分散強度と分散プロセスは、このステージの効率と密接に関連しています。
安定化段階では、ポリマー鎖を粒子表面に吸着させて、粒子間の再凝集を防ぎます。この段階の速度と有効性は、材料の特性、配合、パルプ製造装置とプロセスによって異なります。
すべての材料がパルプ製造プロセス全体を通じて同時に3つの段階を経るわけではないことに注意する必要があります。スラリーの異なる部分は、異なる段階にある可能性があります。たとえば、スラリーの一部が安定化段階に入った場合もあれば、まだ湿潤段階にある部分もあります。このような状況は非常に一般的であり、パルプ製造プロセスの制御の複雑さと困難さの一因となっています。
1.4 スラリーの分散装置とプロセス
スラリー分散に用いる装置は、大きく分けて2種類あります。1つ目は、流体の動きによって発生するせん断力を利用して粒子の凝集体を分散させる装置です。これには、さまざまなタイプの攪拌ブレードを備えたさまざまなタイプのミキサーやニーダーが含まれます。また、3軸フライス盤とディスクミルも含まれています。2番目のタイプには、攪拌ミルなど、粉砕ビーズを使用して粒子凝集体を衝撃し、分散を達成する装置が含まれます。さらに、キャビテーションと超音波によって生成された瞬間的なマイクロジェットを利用して粒子凝集を分散させる超音波分散機などの特殊な分散装置がいくつかあります。これらの異なるタイプの分散装置を図に示します。
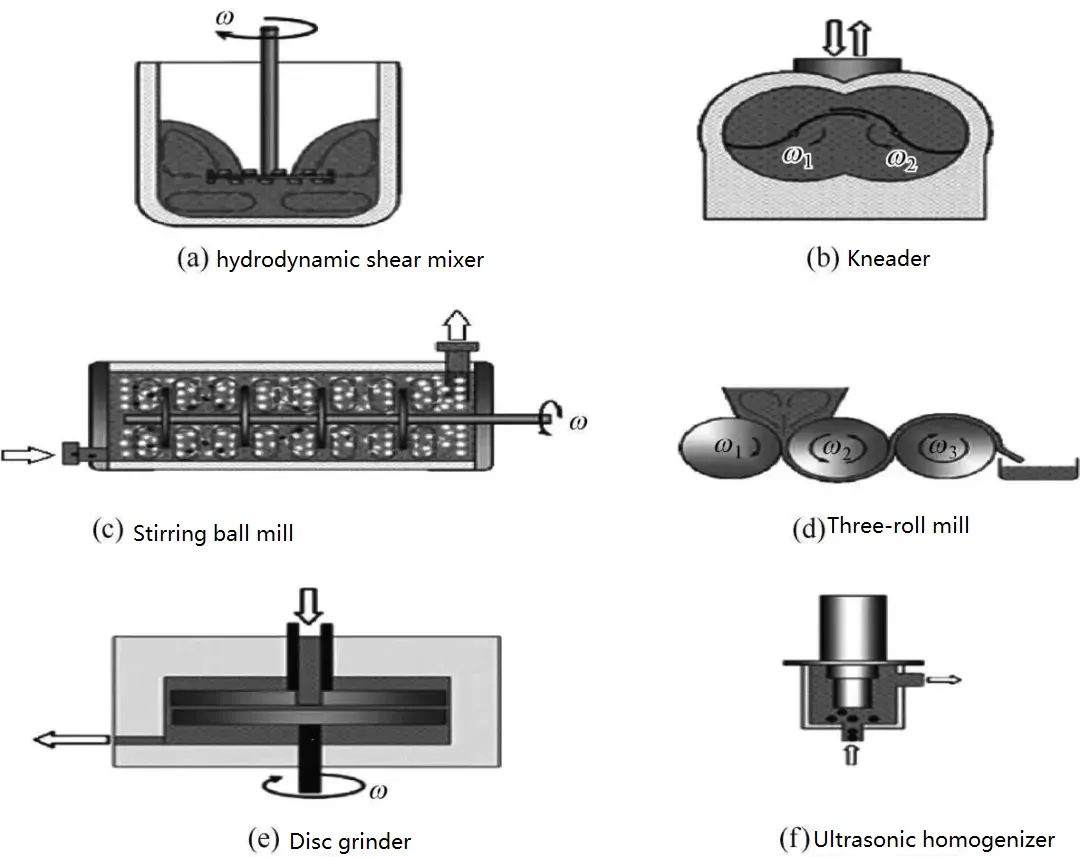
前述の分散装置のすべてがリチウムイオン電池のスラリー製造に適しているわけではありません。例えば、攪拌ミルで研削ビーズを使用すると、大きな衝撃力が発生し、一部の活物質の表面コーティングが損傷し、さらには断片化する可能性があります。その結果、攪拌ミルがリチウムイオン電池のスラリー製造に使用されることはめったにありません。超音波分散装置は、高固形分および高粘度のスラリーにも適していません。しかし、リチウムイオン電池用のスラリーは、一般的に固形分が多く(正極スラリーは60〜80%、負極スラリーは40〜60%)、粘度が高い(20〜200Pa・s)ため、超音波分散機による分散には不向きです。
実際には、リチウムイオン電池のスラリー製造に使用される機器は、流体の動きによって発生するせん断力に依存して分散します。これには、ミキサー、ニーダー、および最も一般的な機器であるツインプラネットミキサーが含まれ、セクション2で詳しく説明します。スラリーの製造工程は、リチウムイオン電池スラリーの特性にも大きな影響を与えます。例えば、スラリーの特性は、異なる材料を追加する順序によって大きく異なる可能性があります。文献報告によると、ニッケル-コバルト-マンガン三元正極材料用のスラリーを調製するために2つの異なる供給シーケンスを使用すると、スラリーの特性と電極性能に大きな違いが生じることが示されています。2番目の供給シーケンスでは、電極の剥離強度と導電率がはるかに高い、より高い固形分スラリーが生成されます。これは、導電性添加剤を主材料と事前に混合すると、導電性添加剤が主材料の表面をコーティングし、遊離導電性添加剤が減少するためです。これにより、スラリーの粘度が低下し、乾燥中の導電性添加剤の凝集が最小限に抑えられ、良好な導電性ネットワークの形成が容易になります。
現在、リチウム電池業界で一般的に使用されているスラリー製造プロセスには、ウェットプロセスとドライプロセスの2つの主要なタイプがあります。それらの間の主な違いは、スラリーの初期固形分にあります。湿式プロセスでは、スラリーの初期固形分が少なくなり、乾式プロセスでは、スラリーの初期固形分が高くなります。
湿式スラリー製造のプロセスフローでは、まず導電性添加剤とバインダーを混合して分散させます。完全に分散させた後、活物質を添加し、さらに混合して分散させます。最後に、コーティング目的で粘度を調整するために、適量の溶媒を添加します。バインダーは、粉末状または液体状のいずれかで存在できます。バインダーを溶液として調製すると、その効果が容易になりますが、一部の企業では粉末バインダーを直接使用する企業もあります。バインダーが高分子量で粒子サイズが大きい場合、バインダーが溶解するまでに時間がかかる場合があることに注意してください。このような場合、バインダーを溶液として調製する必要があります。
ドライスラリー製造のプロセスフローは、まず活物質や導電性添加剤などの粉末材料を事前に混合します。次に、バインダー溶液または溶剤の一部を添加し、混合物を高固形分および高粘度の条件下で攪拌または混練します。その後、残りのバインダー溶液または溶剤を徐々に添加して希釈および分散させます。最後に、適量の溶剤を添加して、コーティング目的で粘度を調整します。
ドライスラリーの製造工程の特徴は、初期段階では高固形分・高粘度の条件下で混合・分散(混練)を行うことです。この段階では、材料は厚くペースト状のスラリー状態にあり、攪拌パドルによって加えられる機械的な力は強力です。さらに、粒子間には大きな内部摩擦があり、濡れと分散を促進し、高い分散度をもたらします。したがって、ドライスラリー製造プロセスはスラリー製造時間を短縮でき、得られるスラリーは粘度が低く、ウェットスラリー製造プロセスと比較して固形分を高くすることができます。
しかし、ドライスラリーの製造工程では、材料の最適な状態を制御することは困難です。原材料の粒子サイズ、比表面積、およびその他の物理的特性に変化がある場合、最適な分散状態を達成するためには、中間固形分などのプロセスパラメータを調整する必要があります。これは、生産効率とバッチ間の一貫性に影響を与える可能性があります。
02 パルプ化設備の現状
2.1従来のパルプ化装置– ツインプラネットミキサー
現在、国内外のリチウムイオン電池の生産では、スラリー製造に従来の攪拌プロセスが一般的に採用されており、多くの場合、ツインプラネットミキサーを利用しています。の動作原理 tWin Planet Mixerは、2〜3枚の低速攪拌ブレードを組み合わせた動きで、同時に回転および回転します。この動きにより、図に示すように、ブレードはミキシングドラム内のスペース全体を覆うことができます。
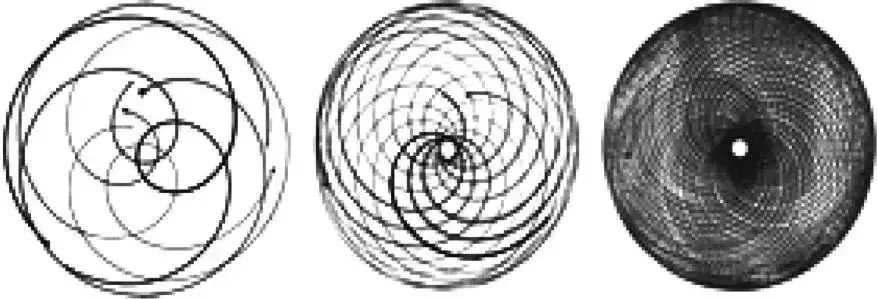
技術の進歩に伴い、スラリー製造設備はさらに改善されています。従来の低速撹拌翼に加え、高速分散翼を追加しました。これらの高速分散ブレードは、歯付きディスクの急速な回転を利用して、強力なせん断力を生成します。これにより、図に示すように、予め混合されたスラリーをさらに分散させることができます。
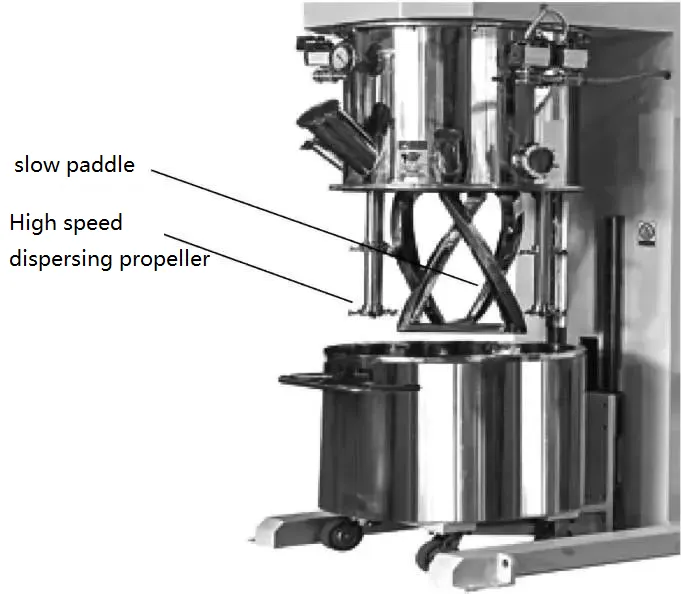
ツインプラネットミキサーには、供給順序、速度、時間などのプロセスパラメータを簡単に調整して、さまざまな材料特性に対応できるという顕著な利点があります。また、スラリーの特性が要件を満たさない場合のやり直しも容易で、強力な適応性と柔軟性を発揮します。さらに、特に小規模ミキサーの場合、製品の切り替え時には、清掃が比較的簡単です。
ツインプラネットミキサーでは、材料と攪拌ブレードとの相互作用は確率分布に従うため、すべての材料を完全にブレンドして分散させるためには長い混合時間が必要です。初期段階では、スラリーの準備に10時間以上かかることがありました。継続的なプロセス改善、特にドライスラリー製造技術の導入により、生産時間は3〜4時間に短縮されました。しかし、固有の制限により、ツインプラネットミキサーでスラリー製造時間をさらに短縮することは困難です。スラリー製造の効率は比較的低く、単位あたりのエネルギー消費量は高くなります。
ミキシングドラムの容量が大きくなると、均一な分散を実現することが難しくなります。現在、リチウムイオン電池のスラリー製造に使用されるツインプラネットミキサーの最大容量は2000リットルを超えず、最大バッチサイズは約1200リットルのスラリーです。
ツインプラネットミキサーの主なメーカーは、アメリカのロス、日本の浅田鉄工所と井上製作所、中国のホンユンミキシングイクイップメントです。ツインプラネットミキサーの技術は非常に成熟しています。
2.2 デュアルプラネタリーミキサーの限られた分散能力を補完するために、新しいタイプのスラリー分散装置である薄膜高速分散機が導入されています。小さな粒子サイズのリン酸鉄リチウムや比表面積の大きい導電性カーボンブラックなど、分散が困難な材料を扱う場合、デュアルプラネタリーミキサーは効果的な分散を実現するのに苦労する可能性があります。そのため、より効率的な分散装置が必要であり、日本のPRIMIX社が開発した薄膜高速分散機は、スラリー分散の優れた選択肢です。
薄膜高速分散機の動作原理は次のとおりです:スラリーは底部から分散容器に入り、分散ホイールとともに高速で回転します。遠心力の下で、スラリーは分散容器の内壁に投げられ、スラリーリングを形成します。さらに、遠心力の影響を受けたスラリーは、分散ホイールの外壁から急速に分離し、分散容器の壁に衝撃を与えます。同時に、ホイールの表面に瞬間的な真空が形成され、スラリーがホイールの分散穴を通過しやすくなり、図に示す軌道が得られます。
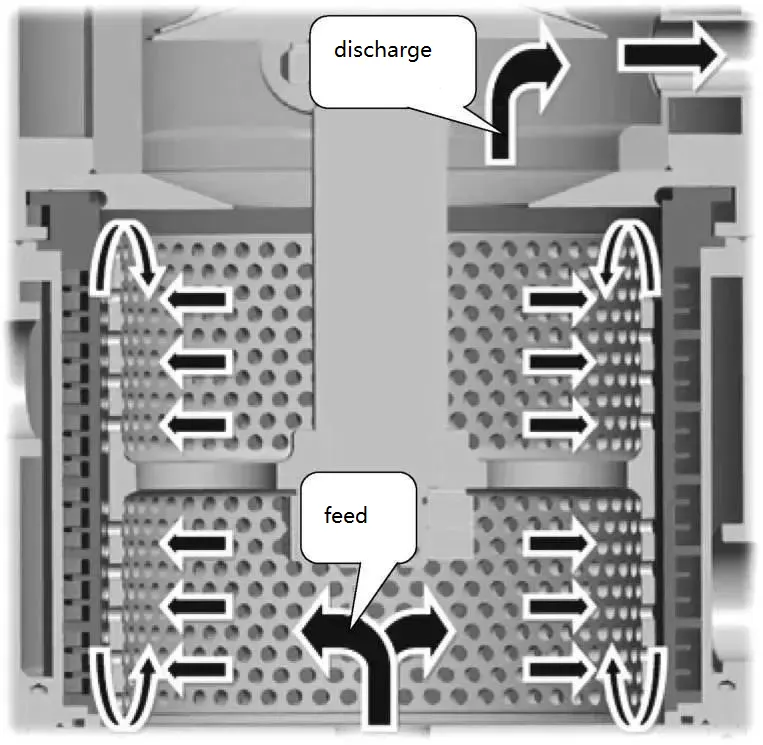
さらに、分散ホイールと容器壁の間のギャップがわずか2mmと狭いため、分散ホイールが高速(最大30〜50m / sの線速度)で回転すると、スラリーはこの小さなギャップ内で均一で激しいせん断力を受けます。スラリーは分散器内で約30秒の滞留時間を持っています。この間、スラリーは分散器内で連続的に循環し、せん断分散を受けるため、理想的な分散効果が得られます。この図は、シミュレーション計算を通じて得られた、ツインプラネットミキサーと薄膜高速分散機の両方でスラリーに作用するせん断力の強度と頻度の比較を示しています。図から、ツインプラネットミキサーでは、スラリーは攪拌ブレードの端部でのみ強いせん断力を受け、スラリーに対する高いせん断作用の頻度が低くなることがわかります。対照的に、薄膜高速分散機では、スラリーは全領域にわたって強いせん断力を受け、スラリーに高いせん断作用が高頻度で発生します。これにより、スラリーの分散効果と効率が大幅に向上します。
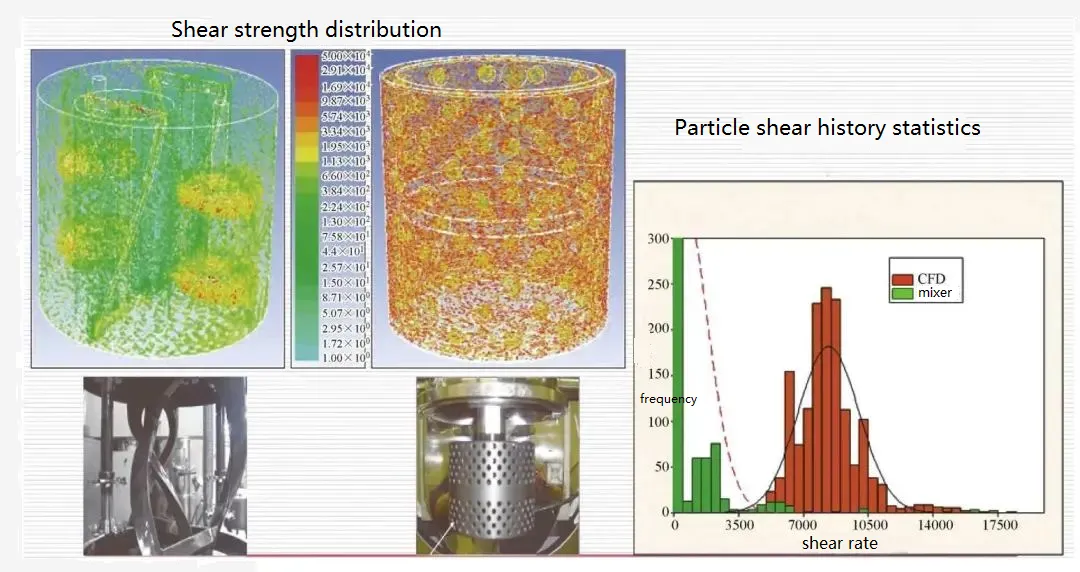
日本のPRIMIXが先駆けて開発した薄膜高速分散機は、韓国や中国の一部のリチウムイオン電池メーカーに採用されています。SHANGSHUIは国内で最初に導入し、その製品性能はPRIMIXの製品と同レベルに達しています。この薄膜高速分散機は、単独でスラリー製造に使用できないことに注意してください。Twin planet Mixerなどの装置を使用して粉末材料と液体材料を事前に混合してスラリーを形成し、その後、Thin-film High-Speed Disperserを使用してさらに分散する必要があります。したがって、この装置の適用には一定の制限があり、通常、分散しにくい材料の製造にはTwin Planet Mixerと組み合わせて使用されます。
2.3新しいパルプ化装置–二軸スクリューパルプ化機
ツインプラネットミキサーの効率の低さの問題に対処するために、一部のメーカーは新しいスラリー製造プロセスと機器を導入しています。その中でも大きな注目を集めているのが、二軸押出機を中核装置とする連続パルプ化システムです。ドイツのブルックナーは、このシステムを導入した企業の1つであり、広く採用されています。
もともとプラスチック加工などの業界で使用されていた二軸スクリュー押出機は、高粘度材料の混合と分散に適しています。ブルックナーは、この装置をリチウムイオン電池スラリー製造の分野に導入しました。このシステムは、スクリューに沿って異なる位置に粉末と液体を導入することにより、スラリーの連続調製を可能にします。
具体的なプロセスは次のとおりです:活物質と導電剤の粉末は、最初にネジの前端に導入されます。ネジが材料を後端に向かって運ぶと、溶剤または接着剤がネジのさまざまなセクションに順次追加されます。混練、希釈、分散、脱気などのプロセスを実現するために、さまざまなスクリューエレメントが利用されています。ネジの一番端で、出力は完成したスラリーです。
ツインスクリューパルプ化機では、スラリーの分散は主に混練段階で発生します。この段階では、スラリーの粘度が高く、スクリューエレメントの作用により激しいせん断力が発生します。これにより、スラリーの効率的な分散が可能になります。
ダブルスクリューマシンでのパルプ化プロセスには、粉末原料と液体原料の連続混合が含まれ、巨視的ブレンドの効率が大幅に向上します。また、機械内の混練エレメントにより、高固形分や高粘度のスラリーに対して高強度のせん断分散を実現し、分散効率を大幅に向上させています。その結果、ダブルスクリューパルプ化機は、高効率や低エネルギー消費などの顕著な利点を提供します。
ただし、リチウムイオン電池スラリー製造にツインスクリューパルプ化機を使用することには、いくつかの顕著な欠点もあります。まず、ツインスクリューパルプ化機のスクリューの長さが長く、摩耗を減らして滞留時間を延長する必要があるため、回転速度を高くしすぎることはできません。通常、スクリューエレメントの端の線速度は2〜3 m / sです。このような低い線速度で強いせん断力を発生させるには、スクリューエレメント間およびスクリューエレメントとバレル壁の間の最小クリアランスを最小限に抑える必要があります。現在、ツインスクリューパルプ化機の最小クリアランスは約0.2〜0.3mmです。このような小さなクリアランスは、処理と設置に高い精度を必要とし、スクリューエレメントの摩耗につながる可能性があります。結果として生じる摩耗した金属粒子は、リチウムイオン電池製品に深刻な安全上の問題を引き起こす可能性があります。
第二に、ツインスクリューマシンの連続パルプ化モードでは、すべての材料に対して正確で安定した供給速度を確保するために、粉末および液体原料の正確な動的計量が必要です。特定の材料の供給速度が変動すると、スラリーの成分比率が変動する可能性があります。これらの変動が許容範囲を超えると、スラリーの一部が拒否されたり、後続のプロセスで予期しない損失が発生したりする可能性があります。したがって、この連続パルプ化システムには、高精度の原材料計量および供給システムを装備する必要があり、システム全体のコストが大幅に増加します。実際の生産では、送り速度の変動による異常の発生を防ぐため、二軸押出機の後に攪拌式の大型バッファータンクを設置することが多いです。押出機によって生成されたスラリーは、供給速度の瞬間的な変動の影響を排除するために、バッファータンク内で部分的に均質化されます。ただし、このアプローチにより、システムはバッチパルプ化システムにやや似ています。
さらに、ツインスクリューパルプ化機は、原材料の品質の変動に敏感です。原料品質の変動によりスラリーパラメータが不適合となった場合、再加工はできません。また、異なる製品バリエーションを切り替える場合、新しい材料や配合に対応するために一部のスクリュー要素を変更する必要があり、その結果、適応性が低下する場合があります。
現在、二軸スクリューパルプ化機の主なサプライヤーはドイツのブリュックナー社です。中国の一部の国内メーカーも同様の機器を提供しています。この連続パルプ化システムは、中国の国内動力電池工場で採用されています。
2.4新しいパルプ化装置–循環パルプ化機
連続パルプ化システムの長所と短所を考慮して、一部のメーカーは半連続パルプ化システムを導入しています。たとえば、Shangshui Intelligentは、連続パルプ化システムとバッチパルプ化システムの利点を組み合わせた循環式高効率パルプ化機を開発しました。このシステムは、バッチ計量、パルプ化のための連続供給、および循環分散を利用して、スラリーの効率的な調製とバッチ全体の均一な分散を実現します。これは、国内のハイエンドパワーバッテリー工場で採用されています。Shangshui Intelligentの循環パルプ化機の基本構造を図14に示します。
基本的な動作原理は、最初に粉末を混合し、粉末供給モジュールを介して所定の流量でパルプ化機に連続的に供給することです。パルプ化機の排出時に形成される負圧下で、粉末はいくらかのガスを放出し、高速回転する粉末分散装置によって煙のような状態に分散されます。次に、流れの速い液体に引き込まれ、浸漬され、液体に分散されます。スラリーがインペラの下の分散モジュールに下向きに流れると、高速回転インペラとチャンバーに固定されたステータから強いせん断力を受け、ロータステータ構造を形成します。これにより良好な分散状態が達成され、スラリーはインペラによって加速され、接線方向の出口から排出されます。
03 パルプ化装置の今後の開発動向
従来のミキサーは、これまでのところ依然として主流のパルプ化装置であり、その利点は、その強力な適応性にあり、特に頻繁な品種変更と小さなバッチサイズのリチウムイオン電池の製造に適しています。しかし、品種の変更頻度が少なく、バッチサイズが大きいパワーバッテリー製造の分野では、単一マシンの容量が低く、ミキサーのエネルギー消費が高いという欠点により、分散効率の高い新しいパルプ化装置に徐々に置き換えられています。たとえば、SHANGSHUIの循環パルプ化機は、中国のハイエンドパワーバッテリーメーカーに徐々に受け入れられ、採用されています。
さらに、新しい分散剤を研究し、高強度分散装置への依存を減らすことも、業界の将来の開発の方向性の1つです。