DeLIDIANBIJI
01 Introduction au processus de mise en pâte
1.1 L’importance du processus de fabrication de la pâte à papier
La limite de performance des batteries lithium-ion est déterminée par le système chimique utilisé, y compris les matériaux actifs de la cathode et de l’anode, ainsi que l’électrolyte. Cependant, les performances réelles dépendent de manière cruciale de la microstructure de l’électrode, qui est principalement déterminée par la microstructure de la boue et le processus de revêtement. Dans ce contexte, la microstructure de la boue joue un rôle dominant. Par conséquent, il est largement reconnu que l’influence du processus de fabrication sur les performances des batteries lithium-ion est d’au moins 70 % dans les processus de démarrage, et dans ces processus, l’impact du processus de fabrication de la pâte à lui seul représente au moins 70 %. En d’autres termes, le processus de fabrication de la pâte contribue à environ la moitié de l’influence globale.
1.2 Composition de la boue et état de dispersion idéal de chaque composant
Les matériaux d’électrode des batteries lithium-ion se composent de trois composants principaux : les matériaux actifs, les additifs conducteurs et les liants. Parmi eux, le matériau actif constitue la grande majorité du poids total, allant généralement de 90% à 98%, tandis que les proportions d’additifs conducteurs et de liants sont relativement faibles, généralement entre 1% et 5%. Ces principaux composants diffèrent considérablement par leurs propriétés physiques et leurs tailles. Les particules du matériau actif varient généralement de 1 à 20 μm, tandis que la majorité des additifs conducteurs sont des matériaux nanocarbonés. Par exemple, le noir de carbone couramment utilisé a des diamètres de particules primaires de l’ordre de dizaines de nanomètres, et les nanotubes de carbone ont des diamètres généralement inférieurs à 30 nm. Le liant est un matériau polymère qui peut se dissoudre dans les solvants ou former des microémulsions dans les solvants.
L’électrode d’une batterie lithium-ion doit assurer un bon transport d’électrons et d’ions, ce qui nécessite l’état de distribution du matériau actif, des additifs conducteurs et des liants pour répondre à certaines exigences. L’état de distribution idéal de chaque matériau dans l’électrode est illustré sur la figure, où le matériau actif est complètement dispersé, les additifs conducteurs sont entièrement dispersés et en contact suffisant avec le matériau actif, formant un bon réseau de conduction électronique, et le liant est uniformément réparti dans l’électrode, liant le matériau actif et les additifs conducteurs ensemble pour former une électrode cohésive.
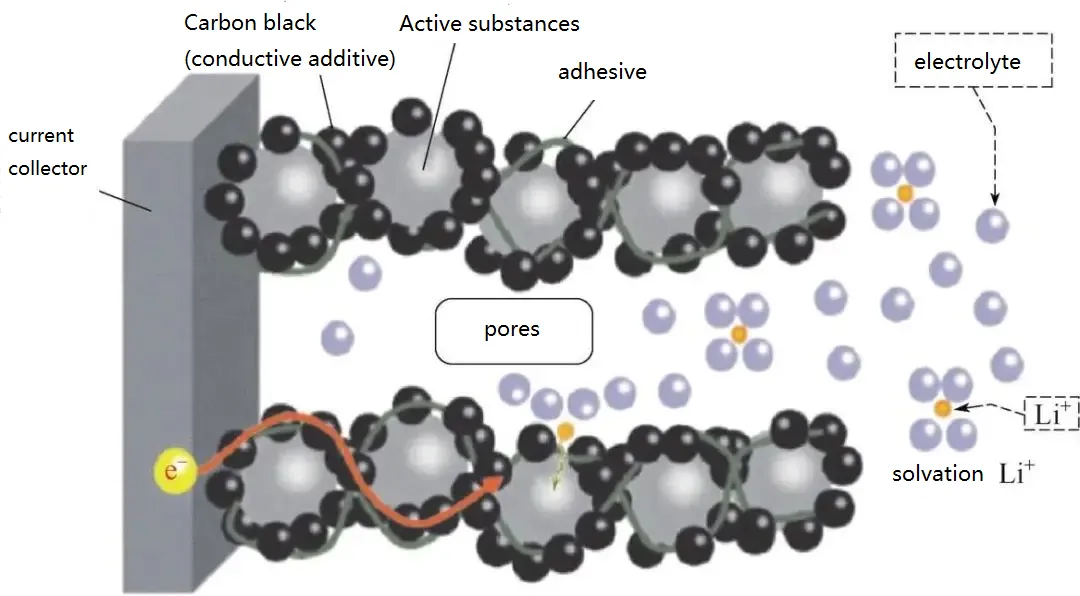
Afin d’obtenir la microstructure souhaitée de l’électrode, il est nécessaire d’obtenir une boue avec la microstructure correspondante pendant le processus de fabrication de la pâte à papier. Cela signifie que le matériau actif, les additifs conducteurs et les liants dans la boue doivent être complètement dispersés, et qu’il doit y avoir une bonne liaison entre les additifs conducteurs et le matériau actif, ainsi qu’entre le liant et les additifs conducteurs/matériau actif. De plus, l’état de dispersion de chaque composant dans la suspension doit être stable. La boue est essentiellement une suspension où les particules solides sont dispersées dans un liquide. Diverses forces agissent entre les particules en suspension, et les forces d’attraction entre les particules formées par les interactions de van der Waals sont la principale cause de l’agrégation des particules. Pour éviter cette agrégation, il est nécessaire d’avoir un certain niveau de répulsion entre les particules. Les types courants de répulsion comprennent la répulsion électrostatique et l’entrave stérique causée par les chaînes polymères. La théorie DLVO (théorie de Deryaguin-Landau-Verwey-Overbeek) est une théorie classique utilisée pour décrire la stabilité des dispersions colloïdales. Il examine les effets combinés de la répulsion électrostatique et de l’attraction de van der Waals. Comme le montre la figure, l’énergie totale formée par la répulsion électrostatique et les forces de van der Waals atteint une valeur maximale (Gmax) à une certaine distance. Cette valeur maximale forme une barrière d’énergie, empêchant les particules de s’approcher davantage et de former des primaires.
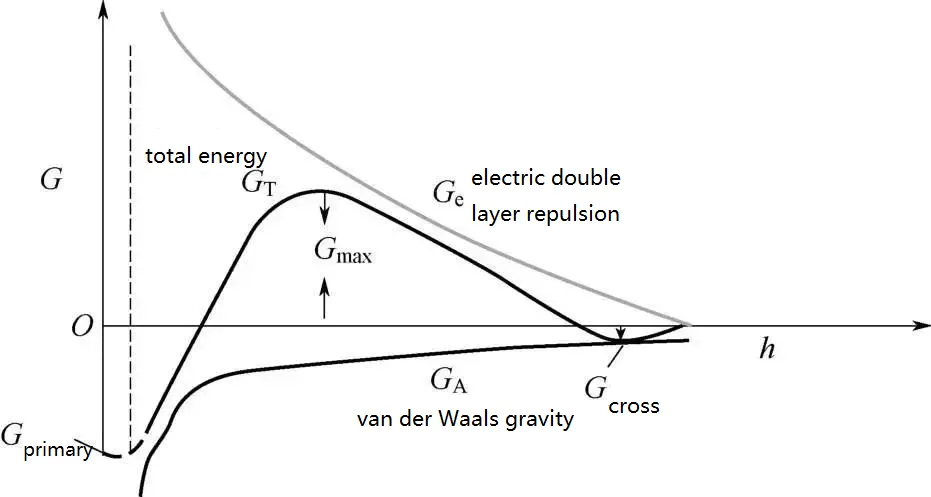
Dans la suspension des batteries lithium-ion, l’obstacle stérique formé par l’adsorption des chaînes de polymères liants à la surface des particules joue un rôle crucial dans la stabilité de la boue. Lorsque les molécules de liant s’adsorbent à la surface des particules pour former une couche d’adsorption, les couches d’adsorption sur deux surfaces de particules se rapprochent l’une de l’autre. En raison de l’obstacle stérique, une énergie d’interaction est générée. La force d’entrave stérique, ainsi que la répulsion électrostatique et l’attraction de van der Waals, constituent l’énergie d’interaction totale entre les particules, comme le montre la figure.
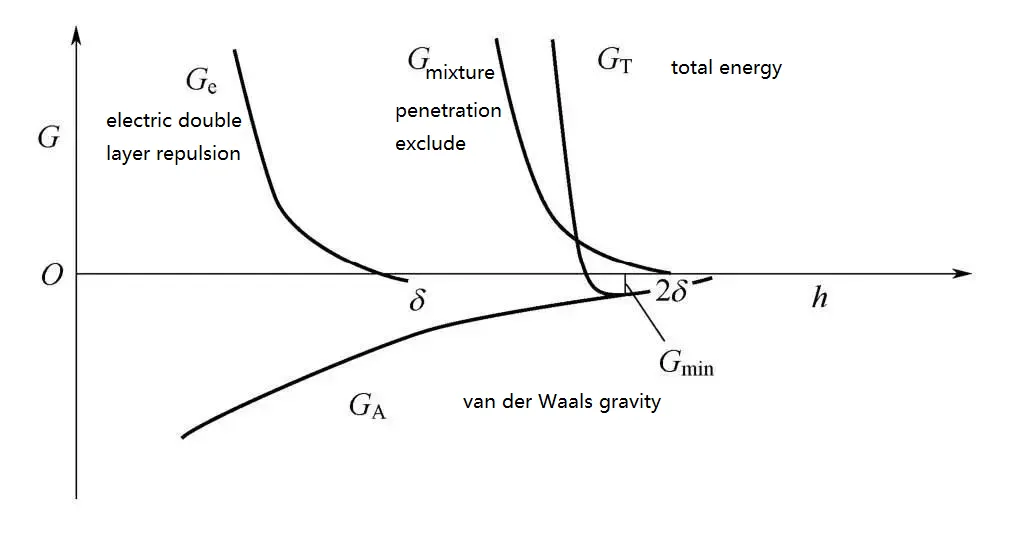
Par conséquent, pour éviter l’agrégation des particules dans la boue, il est nécessaire que les chaînes polymères du liant s’adsorbent sur les surfaces des particules, créant ainsi un certain niveau d’entrave stérique. Cela permet à l’état de dispersion de la suspension de rester stable pendant une période prolongée.
1.3 Le processus microscopique de fabrication de la pâte à papier
Le processus de fabrication de la pâte à papier dans la fabrication de batteries lithium-ion implique la dispersion uniforme de matériaux actifs et d’additifs conducteurs dans un solvant, formant une boue stable sous l’influence de chaînes polymères liantes. D’un point de vue microscopique, ce processus comprend généralement trois étapes principales : le mouillage, la dispersion et la stabilisation, comme illustré sur la figure.
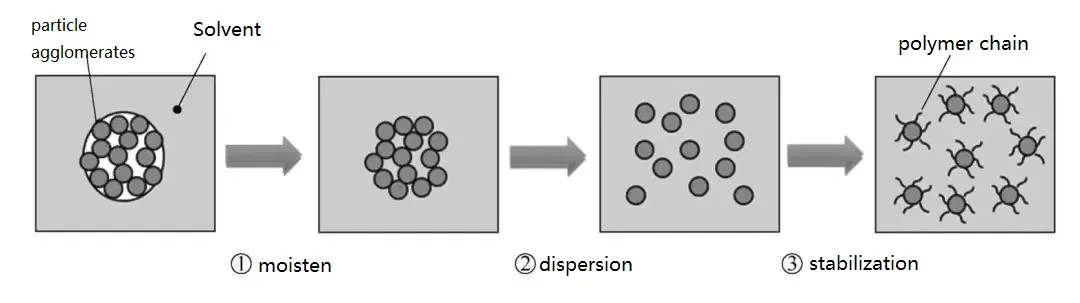
L’étape de mouillage est le processus qui permet d’obtenir un contact suffisant entre le solvant et les surfaces des particules. Il s’agit de déplacer l’air des agglomérats de particules et de le remplacer par le solvant. La vitesse et l’efficacité de cette étape dépendent de l’affinité entre la surface des particules et le solvant, ainsi que de l’équipement et du processus de fabrication de la pâte à papier.
L’étape de dispersion est le processus de rupture des agglomérats de particules. La vitesse et l’efficacité de cette étape sont influencées par les caractéristiques du matériau telles que la taille des particules, la surface spécifique et les forces entre les particules. De plus, l’intensité de la dispersion et le processus de dispersion sont étroitement liés à l’efficacité de cette étape.
L’étape de stabilisation implique l’adsorption de chaînes polymères sur les surfaces des particules pour empêcher la réagrégation entre les particules. La rapidité et l’efficacité de cette étape dépendent des caractéristiques du matériau, de la formulation, ainsi que de l’équipement et du processus de fabrication de la pâte à papier.
Il convient de noter que tous les matériaux ne subissent pas les trois étapes simultanément tout au long du processus de fabrication de la pâte à papier. Différentes parties de la boue peuvent se trouver à différents stades. Par exemple, certaines parties du lisier peuvent être entrées dans la phase de stabilisation, tandis que d’autres sont encore dans la phase de mouillage. Cette situation est assez courante et contribue à la complexité et à la difficulté de contrôler le processus de fabrication de la pâte à papier.
1.4 Équipement et procédés de dispersion des boues
Les équipements utilisés pour la dispersion du lisier peuvent être classés en deux types. Le premier type implique des dispositifs qui utilisent les forces de cisaillement générées par le mouvement des fluides pour disperser les agglomérats de particules. Cela comprend différents types de mélangeurs et de pétrins équipés de différents types de lames d’agitation. Il comprend également des fraiseuses à trois axes et des broyeurs à disques. Le deuxième type implique des équipements qui utilisent des billes de broyage pour impacter les agglomérats de particules et obtenir une dispersion, tels que les broyeurs agités. De plus, il existe des dispositifs de dispersion spécialisés, tels que les disperseurs à ultrasons, qui utilisent la cavitation et les micro-jets instantanés générés par les ultrasons pour disperser les agglomérats de particules. Ces différents types d’équipements de dispersion sont illustrés dans la figure.
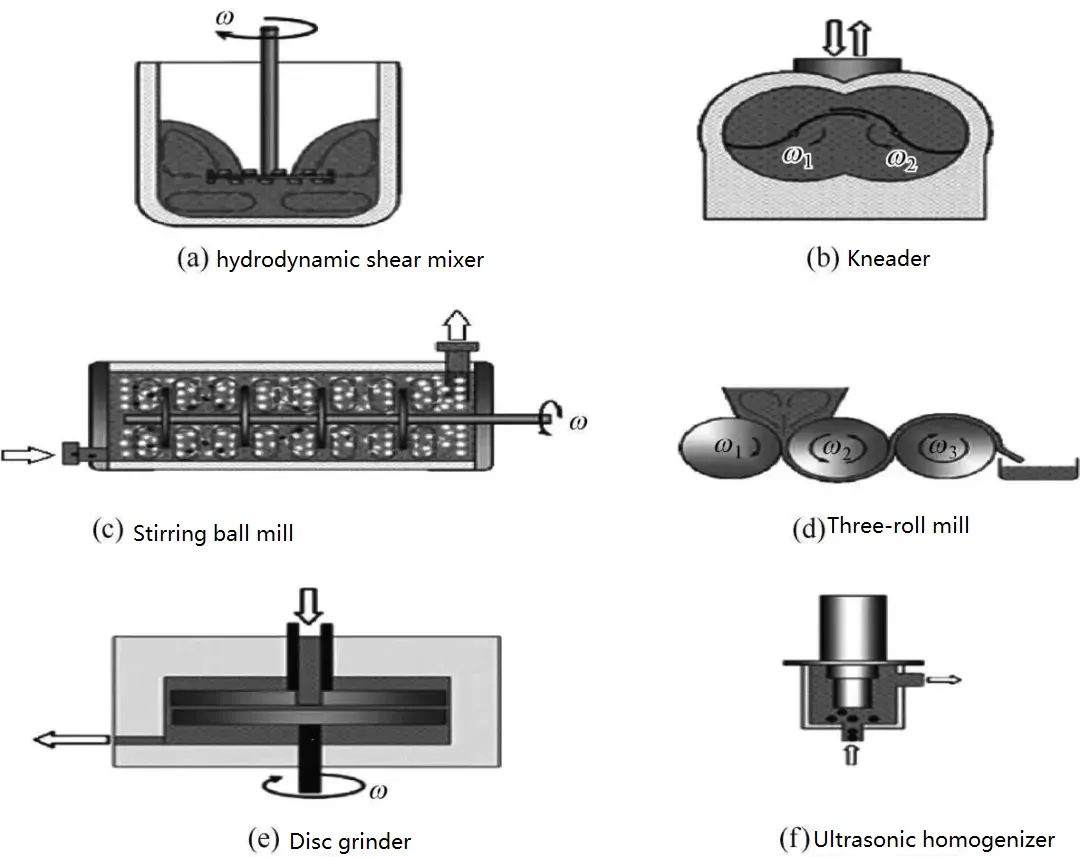
Tous les équipements de dispersion susmentionnés ne conviennent pas à la production de boues dans les batteries lithium-ion. Par exemple, l’utilisation de billes de broyage dans les broyeurs agités génère des forces d’impact importantes, qui peuvent endommager le revêtement de surface de certains matériaux actifs et même entraîner leur fragmentation. Par conséquent, les broyeurs agités sont rarement utilisés dans la production de boues pour les batteries lithium-ion. Les dispositifs de dispersion à ultrasons ne conviennent pas non plus aux boues à haute teneur en solides et à haute viscosité. Cependant, les boues pour les batteries lithium-ion ont généralement une teneur élevée en solides (60 % à 80 % pour les boues à électrodes positives, 40 % à 60 % pour les boues à électrodes négatives) et une viscosité élevée (20 à 200 Pa·s), ce qui les rend impropres à la dispersion à l’aide de disperseurs à ultrasons.
En pratique, l’équipement utilisé pour la production de boue dans les batteries lithium-ion repose sur les forces de cisaillement générées par le mouvement du fluide pour la dispersion. Il s’agit notamment des mélangeurs, des pétrins et de l’équipement le plus typique, le mélangeur Twin planet, qui sera détaillé dans la section 2. Le processus de production des boues a également un impact significatif sur les propriétés des boues de batteries lithium-ion. Par exemple, les propriétés de la boue peuvent varier considérablement en fonction de l’ordre d’ajout des différents matériaux. Des rapports de littérature ont montré que l’utilisation de deux séquences d’alimentation différentes pour préparer des boues pour des matériaux d’électrodes positives ternaires nickel-cobalt-manganèse entraîne des différences significatives dans les caractéristiques des boues et les performances des électrodes. La deuxième séquence d’alimentation produit une suspension à teneur en solides plus élevée, avec une résistance au pelage et une conductivité de l’électrode beaucoup plus élevées. En effet, le prémélange des additifs conducteurs avec le matériau principal permet aux additifs conducteurs de recouvrir la surface du matériau principal, réduisant ainsi les additifs conducteurs libres. Ceci, à son tour, réduit la viscosité de la boue et minimise l’agrégation des additifs conducteurs pendant le séchage, facilitant ainsi la formation d’un bon réseau conducteur.
Actuellement, il existe deux principaux types de processus de production de boue couramment utilisés dans l’industrie des batteries au lithium, connus sous le nom de processus humide et de processus sec. La principale différence entre eux réside dans la teneur initiale en solides de la boue. Le processus humide implique une teneur initiale en solides plus faible de la boue, tandis que le processus sec implique une teneur initiale en solides plus élevée de la boue.
Le déroulement du processus de production de boues humides consiste d’abord à mélanger et à disperser les additifs conducteurs et les liants. Après avoir obtenu une dispersion complète, les matériaux actifs sont ajoutés, puis mélangés et dispersés. Enfin, une quantité appropriée de solvant est ajoutée pour ajuster la viscosité à des fins de revêtement. Le liant peut exister sous forme de poudre ou de liquide. La préparation du liant en tant que solution facilite son efficacité, bien que certaines entreprises utilisent également directement des liants en poudre. Il convient de noter que lorsque le liant a un poids moléculaire élevé et une grande taille de particules, la dissolution du liant peut prendre plus de temps. Dans de tels cas, il est nécessaire de préparer le liant en tant que solution.
Le déroulement du processus de production de boues sèches implique d’abord le prémélange de matériaux en poudre tels que des matériaux actifs et des additifs conducteurs. Ensuite, une partie de la solution de liant ou du solvant est ajoutée, et le mélange est agité ou pétri dans des conditions de teneur élevée en solides et de viscosité élevée. Par la suite, la solution liante ou le solvant restant est ajouté progressivement pour la dilution et la dispersion. Enfin, une quantité appropriée de solvant est ajoutée pour ajuster la viscosité à des fins de revêtement.
La caractéristique du processus de production de boue sèche est que, dans un premier temps, le mélange et la dispersion (pétrissage) sont effectués dans des conditions de teneur élevée en solides et de viscosité élevée. À ce stade, le matériau est dans un état de boue épaisse et pâteuse, et la force mécanique appliquée par la palette d’agitation est forte. De plus, il existe une friction interne importante entre les particules, ce qui favorise le mouillage et la dispersion, ce qui entraîne un degré élevé de dispersion. Par conséquent, le processus de production de lisier sec peut raccourcir le temps de production de lisier, et le coulis obtenu a une viscosité plus faible, ce qui permet une teneur en solides plus élevée par rapport au processus de production de lisier humide.
Cependant, il est difficile de contrôler l’état optimal du matériau dans le processus de production de boue sèche. Lorsqu’il y a des changements dans la taille des particules, la surface spécifique et d’autres propriétés physiques des matières premières, il est nécessaire d’ajuster les paramètres du processus tels que la teneur en solides intermédiaires pour obtenir l’état de dispersion optimal. Cela peut avoir un impact sur l’efficacité de la production et la cohérence d’un lot à l’autre.
02 État actuel de l’équipement de mise en pâte
2.1 Équipement de mise en pâte traditionnel – Mélangeur à deux planètes
À l’heure actuelle, la production nationale et internationale de batteries lithium-ion utilise généralement des procédés d’agitation traditionnels pour la production de boues, souvent à l’aide d’un mélangeur à deux planètes. Le principe de fonctionnement d’un tLe mélangeur Win Planet implique le mouvement combiné de 2 à 3 pales d’agitation à vitesse lente, qui tournent et tournent simultanément. Ce mouvement permet aux pales de couvrir tout l’espace à l’intérieur du tambour de mélange, comme le montre le schéma.
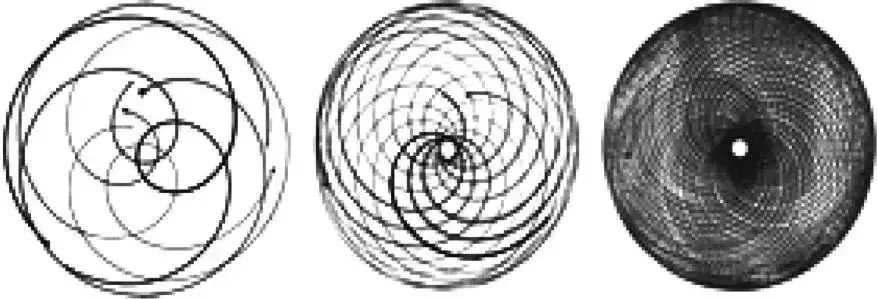
Avec les progrès technologiques, il y a eu de nouvelles améliorations dans les équipements de production de boue. En plus des pales d’agitation à basse vitesse existantes, des pales de dispersion à grande vitesse ont été ajoutées. Ces lames dispersives à grande vitesse utilisent la rotation rapide du disque denté pour générer de fortes forces de cisaillement. Cela permet une dispersion supplémentaire de la boue prémélangée, comme le montre le schéma.
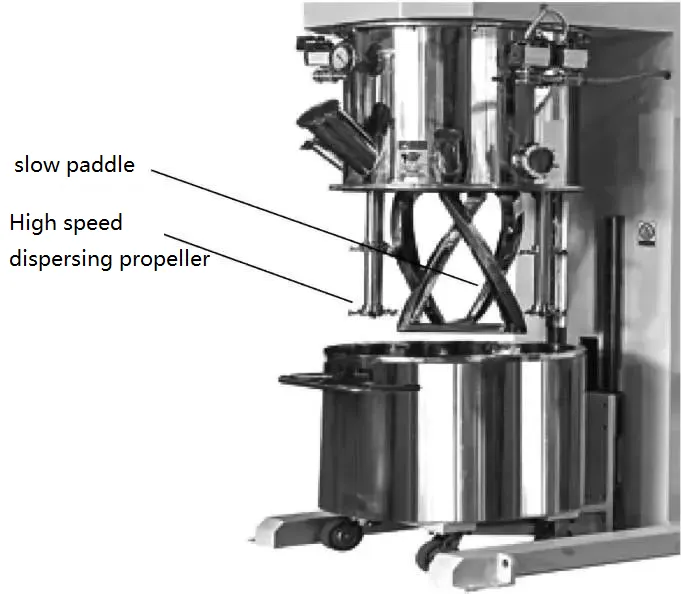
Le mélangeur à deux planètes présente l’avantage d’ajuster facilement les paramètres du processus tels que la séquence d’alimentation, la vitesse et le temps pour s’adapter aux différentes caractéristiques du matériau. Il permet également de retravailler facilement lorsque les propriétés de la boue ne répondent pas aux exigences, faisant preuve d’une grande adaptabilité et d’une grande flexibilité. De plus, lors des changements de produits, en particulier pour les mélangeurs à petite échelle, le nettoyage est relativement simple.
Dans le mélangeur à planètes jumelles, l’interaction du matériau avec les pales d’agitation suit une distribution de probabilité, nécessitant un long temps de mélange pour assurer un mélange et une dispersion complets de tous les matériaux. Dans les premiers stades, la préparation du lisier pouvait prendre plus de 10 heures. Grâce à l’amélioration continue des processus, en particulier l’introduction de techniques de production de boue sèche, le temps de production a été réduit à 3-4 heures. Cependant, en raison de limitations inhérentes, il est difficile de réduire davantage le temps de production de boue avec un mélangeur à deux planètes. L’efficacité de la production de lisier est relativement faible et la consommation d’énergie par unité est plus élevée.
À mesure que le volume du tambour de mélange augmente, il devient plus difficile d’obtenir une dispersion uniforme. Actuellement, le volume maximum des mélangeurs à deux planètes utilisés pour la production de boues de batteries lithium-ion ne dépasse pas 2000 litres, avec une taille de lot maximale d’environ 1200 litres de boue.
Les principaux fabricants de mélangeurs à planètes jumelles comprennent Ross des États-Unis, Asada Iron Works et Inoue Mfg. du Japon, et Hongyun Mixing Equipment de Chine. La technologie du mélangeur à planètes jumelles est très mature.
2.2 Le disperseur à grande vitesse à couche mince, un nouveau type d’équipement de dispersion de boues, est introduit pour compléter la capacité de dispersion limitée du mélangeur planétaire double. Lorsqu’il s’agit de matériaux difficiles à disperser tels que le phosphate de fer lithium de petite taille de petites particules et le noir de carbone conducteur à haute surface spécifique, le mélangeur planétaire double peut avoir du mal à obtenir une dispersion efficace. Par conséquent, un équipement de dispersion plus efficace est nécessaire, et le disperseur à grande vitesse à couche mince, développé par PRIMIX au Japon, est un excellent choix pour la dispersion des boues.
Le principe de fonctionnement du disperseur à grande vitesse à couche mince est le suivant : la boue pénètre dans la cuve de dispersion par le bas et tourne à grande vitesse avec la roue de dispersion. Sous l’effet de la force centrifuge, la boue est projetée contre la paroi interne du récipient en dispersion, formant un anneau de boue. De plus, la boue, influencée par la force centrifuge, se sépare rapidement de la paroi extérieure de la roue de dispersion et heurte les parois de la cuve de dispersion. Simultanément, un vide momentané se forme à la surface de la roue, facilitant le passage de la boue à travers les trous de dispersion sur la roue, ce qui entraîne la trajectoire illustrée sur le schéma.
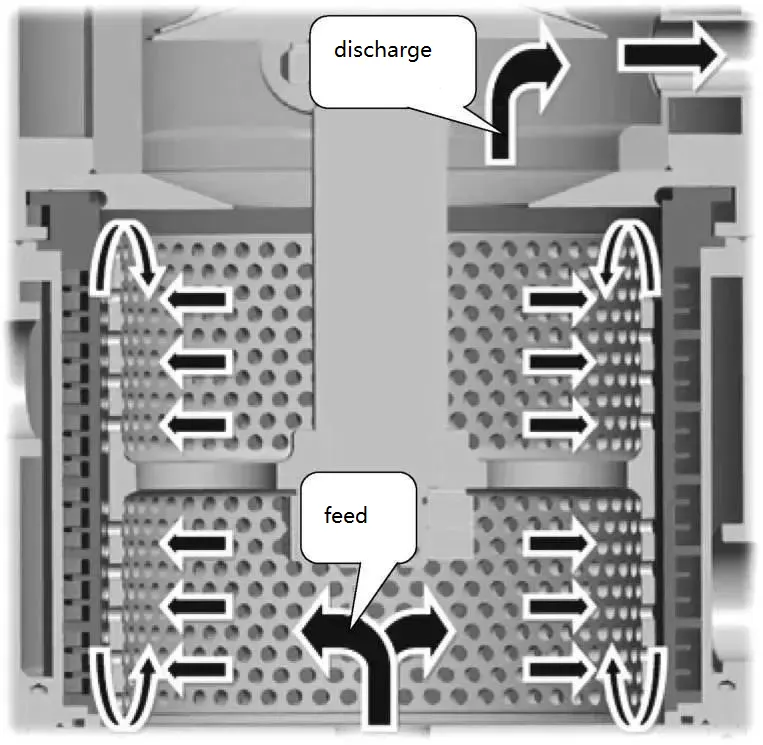
De plus, en raison de l’écart étroit de seulement 2 mm entre la roue de dispersion et la paroi de la cuve, lorsque la roue de dispersion tourne à grande vitesse (avec une vitesse linéaire allant jusqu’à 30-50 m/s), la boue subit des forces de cisaillement uniformes et intenses dans ce petit espace. La boue a un temps de séjour d’environ 30 secondes à l’intérieur du disperseur. Pendant ce temps, la boue subit une circulation continue et une dispersion par cisaillement à l’intérieur du disperseur, ce qui entraîne un effet de dispersion idéal. Le diagramme illustre une comparaison de l’intensité et de la fréquence des forces de cisaillement agissant sur la boue dans le mélangeur à planétaires jumeaux et le disperseur à grande vitesse à couche mince, obtenue par des calculs de simulation. D’après le diagramme, il est évident que dans le mélangeur à planètes jumelles, la boue ne subit que de fortes forces de cisaillement dans la région finale des pales d’agitation, ce qui entraîne une faible fréquence d’action de cisaillement élevée sur la boue. En revanche, dans le disperseur à grande vitesse à couche mince, la boue subit de fortes forces de cisaillement dans toute la région, ce qui entraîne une fréquence élevée d’action de cisaillement élevée sur la boue. Cela améliore considérablement l’effet de dispersion et l’efficacité de la boue.
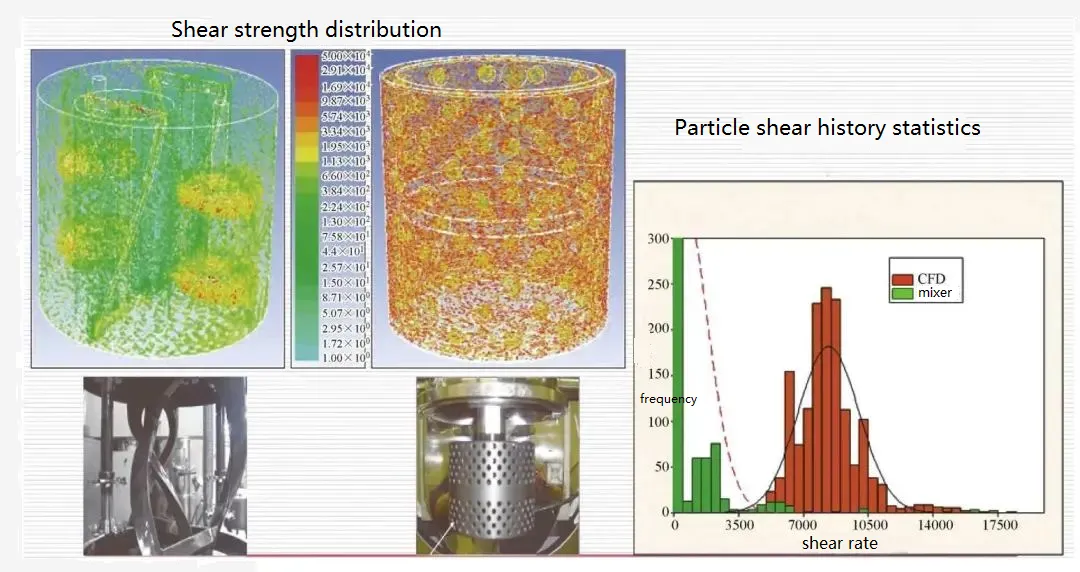
Le disperseur à couche mince à grande vitesse, mis au point par PRIMIX au Japon, a été adopté par certains fabricants de batteries lithium-ion en Corée du Sud et en Chine. SHANGSHUI a été le premier à l’introduire au niveau national, et les performances de ses produits ont atteint le même niveau que les produits PRIMIX. Il convient de noter que ce disperseur à grande vitesse à couche mince ne peut pas être utilisé indépendamment pour la production de boues. Il nécessite un pré-mélange de matériaux en poudre et liquides pour former une boue à l’aide d’un équipement tel qu’un mélangeur à planètes jumelles avant une dispersion supplémentaire à l’aide du disperseur à grande vitesse à couche mince. Par conséquent, l’application de cet équipement présente certaines limites et est généralement utilisée en conjonction avec des mélangeurs à planètes jumelles pour la production de matériaux difficiles à disperser.
2.3 Nouvel équipement de mise en pâte – machine de mise en pâte à double vis
Pour résoudre le problème de la faible efficacité des mélangeurs à planètes jumelles, certains fabricants ont introduit de nouveaux processus et équipements de production de boues. L’un de ces développements qui a suscité beaucoup d’attention est le système de mise en pâte continue, qui comporte une extrudeuse à double vis comme équipement de base. Brueckner d’Allemagne est l’une des entreprises qui a introduit ce système, qui a été largement adopté.
Utilisée à l’origine dans des industries telles que la plasturgie, l’extrudeuse à double vis est adaptée au mélange et à la dispersion de matériaux à haute viscosité. Brueckner a introduit cet équipement dans le domaine de la production de boues de batteries lithium-ion. Le système permet la préparation continue de la boue en introduisant de la poudre et du liquide à différentes positions le long des vis.
Le procédé spécifique est le suivant : la poudre de matériaux actifs et d’agents conducteurs est d’abord introduite à l’extrémité avant des vis. Au fur et à mesure que les vis transportent les matériaux vers l’extrémité arrière, des solvants ou des adhésifs sont ajoutés séquentiellement à différentes sections des vis. Divers éléments de vis sont utilisés pour réaliser des processus tels que le pétrissage, la dilution, la dispersion et la désaération. À la toute fin des vis, le rendement est la boue finie.
Dans la machine de dépulpage à double vis, la dispersion de la boue se produit principalement pendant l’étape de pétrissage. Au cours de cette étape, la boue a une viscosité élevée et des forces de cisaillement intenses sont générées par l’action des éléments de vis. Cela permet une dispersion efficace du lisier.。
Le processus de mise en pâte dans la machine à double vis implique le mélange continu de matières premières pulvérulentes et liquides, améliorant considérablement l’efficacité du mélange macroscopique. De plus, les éléments de pétrissage de la machine fournissent une dispersion par cisaillement de haute intensité pour des matières solides élevées et des boues à haute viscosité, ce qui améliore considérablement l’efficacité de la dispersion. Par conséquent, la machine de dépulpage à double vis offre des avantages notables tels qu’un rendement élevé et une faible consommation d’énergie.
Cependant, l’utilisation de machines de dépulpage à double vis pour la production de boues de batteries lithium-ion présente également des défauts notables. Tout d’abord, en raison de la grande longueur des vis de la machine de dépulpage à double vis et de la nécessité de réduire l’usure et de prolonger le temps de séjour, la vitesse de rotation ne peut pas être trop élevée. En règle générale, la vitesse linéaire à l’extrémité des éléments de vis est comprise entre 2 et 3 m/s. Générer de fortes forces de cisaillement à une vitesse linéaire aussi faible nécessite de minimiser les jeux minimaux entre les éléments de vis et entre les éléments de vis et la paroi du cylindre. Actuellement, le jeu minimum dans les machines de dépulpage à double vis est d’environ 0,2 à 0,3 mm. Un si petit jeu nécessite une grande précision dans le traitement et l’installation, et peut entraîner une usure des éléments de vis. Les particules métalliques usées qui en résultent peuvent présenter de graves risques pour la sécurité des produits de batteries lithium-ion.
Deuxièmement, le mode de mise en pâte continue de la machine à double vis nécessite un dosage dynamique précis des matières premières pulvérulentes et liquides afin de garantir des vitesses d’alimentation précises et stables pour tous les matériaux. Toute fluctuation de la vitesse d’alimentation d’un matériau particulier peut entraîner des fluctuations dans le rapport des ingrédients de la boue. Si ces fluctuations dépassent la plage acceptable, elles peuvent entraîner le rejet d’une partie de la boue ou même provoquer des pertes imprévues dans les processus ultérieurs. Par conséquent, ce système de mise en pâte continue doit être équipé d’un système de dosage et d’alimentation des matières premières de haute précision, ce qui augmente considérablement le coût global du système. Dans la production pratique, pour éviter que les fluctuations des vitesses d’alimentation ne provoquent des anomalies, un grand réservoir tampon avec agitation est souvent installé après l’extrudeuse à double vis. La boue produite par l’extrudeuse est partiellement homogénéisée dans le réservoir tampon pour éliminer l’impact des fluctuations instantanées des vitesses d’alimentation. Cependant, cette approche fait ressembler le système à un système de mise en pâte par lots.
De plus, la machine de mise en pâte à double vis est sensible aux fluctuations de la qualité des matières premières. Si les paramètres de boue ne sont pas conformes en raison de fluctuations de la qualité des matières premières, il n’est pas possible de les retravailler. De plus, lors du passage d’une variante de produit à l’autre, il peut être nécessaire de changer certains éléments de vis pour s’adapter à de nouveaux matériaux et formulations, ce qui entraîne une faible adaptabilité.
Actuellement, le principal fournisseur de machines de mise en pâte à double vis est Brueckner d’Allemagne. Certains fabricants nationaux en Chine proposent également des équipements similaires. Ce système de mise en pâte continue a été adopté par les usines de batteries domestiques en Chine.
2.4 Nouvel équipement de mise en pâte – machine à pâte circulante
Compte tenu des forces et des faiblesses des systèmes de mise en pâte en continu, certains fabricants ont introduit des systèmes de mise en pâte semi-continue. Shangshui Intelligent, par exemple, a mis au point une machine de mise en pâte à circulation à haut rendement qui combine les avantages des systèmes de mise en pâte continue et discontinue. Ce système utilise le dosage des lots, l’alimentation continue pour la mise en pâte et la dispersion circulante pour obtenir une préparation efficace de la boue et une dispersion uniforme de l’ensemble du lot. Il a été adopté par les usines de batteries d’alimentation domestiques haut de gamme. La structure de base de la machine de mise en pâte à papier circulante de Shangshui Intelligent est illustrée à la figure 14.
Le principe de fonctionnement de base consiste à mélanger d’abord la poudre et à l’introduire en continu dans la machine de mise en pâte à travers le module d’alimentation en poudre à un débit prédéterminé. Sous la pression négative formée lors de la décharge de la machine à dépulper, la poudre libère un peu de gaz et est dispersée dans un état semblable à de la fumée par le dispositif de dispersion de poudre rotatif à grande vitesse. Il est ensuite aspiré dans le liquide à écoulement rapide, immergé et dispersé dans le liquide. Lorsque la boue s’écoule vers le bas dans le module de dispersion sous la roue, elle subit des forces de cisaillement intenses de la roue rotative à grande vitesse et du stator fixé dans la chambre, formant une structure rotor-stator. Cela permet d’obtenir un bon état de dispersion, et la boue est accélérée par la roue et déchargée par la sortie tangentielle.
03 Tendances futures du développement des équipements de mise en pâte
Le mélangeur traditionnel est toujours l’équipement de mise en pâte courant jusqu’à présent, et son avantage réside dans sa forte adaptabilité, particulièrement adaptée à la production de batteries lithium-ion avec des changements fréquents de variété et de petites tailles de lots. Cependant, dans le domaine de la fabrication de batteries de puissance, avec des changements de variété moins fréquents et des lots de plus grande taille, les inconvénients de la faible capacité d’une seule machine et de la consommation d’énergie élevée des mélangeurs les font progressivement remplacer par de nouveaux équipements de mise en pâte avec une efficacité de dispersion plus élevée. Par exemple, la machine à pâte circulante de SHANGSHUI a été progressivement acceptée et adoptée par les fabricants de batteries de puissance haut de gamme en Chine.
De plus, la recherche de nouveaux dispersants et la réduction de la dépendance à l’égard des équipements de dispersion à haute intensité constituent également l’une des orientations de développement futures de l’industrie.