Les batteries prismatiques font référence aux batteries avec des boîtiers en aluminium. Ils utilisent la technologie de scellage laser, et la technologie des boîtiers en aluminium entièrement scellés est déjà très mature. Il a de faibles exigences pour les indicateurs technologiques matériels tels que la génération et l’expansion de gaz, ce qui en fait une forme de batterie d’alimentation popularisée précoce en Chine. Par rapport aux deux autres formes de batteries au lithium (cylindriques et à poche), les batteries prismatiques présentent des avantages importants sur le marché, notamment :
(1) Haute fiabilité de l’emballage.
(2) Efficacité élevée d’intégration du système.
(3) Relativement léger avec une densité d’énergie élevée.
(4) Structure simple et évolutivité pratique, ce qui en fait un choix de premier choix pour les cellules individuelles de grande capacité.
(5) Capacité de cellule individuelle élevée, structure de système simple et gestion facile de la batterie.
01 Fonctions principales et description de l’équipement
La ligne d’assemblage de batteries au lithium à boîtier en aluminium est utilisée pour l’assemblage intermédiaire des batteries d’alimentation et constitue une partie importante du processus de production de batteries d’alimentation. Il a un impact significatif sur les performances et la précision de la batterie. Par conséquent, le niveau d’automatisation et la précision opérationnelle de cette ligne d’assemblage attirent de plus en plus l’attention du marché. Dans cette section, nous présenterons une ligne d’assemblage de batteries très mature et éprouvée sur le marché, qui a été reconnue et acceptée. La ligne d’assemblage présente les caractéristiques suivantes :
1. Forte compatibilité : Il peut être compatible avec différentes séries de produits selon les exigences du client.
2. Conception modulaire : temps de changement court, moins de pièces et faible coût.
3. Haute précision d’assemblage : double positionnement utilisant des méthodes visuelles et mécaniques pour améliorer la précision du positionnement.
4. Personnalisation pour différents types de cellules et itinéraires de processus spécifiques au client afin de réaliser des lignes d’assemblage entièrement automatisées.
5. Disposition raisonnable de l’équipement : économie d’espace, ligne entièrement automatisée et faible coût de main-d’œuvre.
6. Assurance de la qualité de fabrication élevée : test et surveillance des paramètres complets.
7. Garantie de fabrication pour la sécurité et la cohérence de la batterie.
Cette ligne de production automatisée est utilisée pour l’assemblage automatique de cellules de batterie lithium-ion prismatiques en aluminium après bobinage. La ligne de production se compose principalement des principaux composants suivants : machine d’essai de presse à chaud, machine à rayons X, machine d’appariement, machine de soudage par ultrasons, machine de soudage à languette, machine d’alignement de noyaux, machine de film / thermoscellage / adhésif, machine de soudage pré-point pour boîtier, machine de soudage de couvercle laser et machine de test de fuite d’hélium. Il réalise des fonctions telles que le pressage thermique des cellules de batterie, les tests aux rayons X, le pré-soudage et l’appariement des languettes d’électrode, le soudage des connecteurs d’électrodes, l’application d’adhésif à l’arrière, le soudage au laser des plaques de recouvrement, l’application d’adhésif, le pliage et l’alignement des languettes et de l’alignement du noyau, l’encapsulation, le soudage du boîtier et de l’étanchéité du couvercle, permettant une automatisation complète tout au long du processus.
1.2 Tendances futures de développement des chaînes de montage
La ligne de production de batteries à coque en aluminium (prismatique) est utilisée depuis longtemps, la technologie correspondante est très mature et la chaîne de montage existante est également similaire. La tendance de développement future, en plus de continuer à améliorer les matériaux et à trouver des matériaux de cellules haute performance, pour les lignes de production d’assemblage de batteries, le rendement élevé et le faible coût sont toujours les orientations futures du développement des batteries au lithium de puissance. Un aperçu de l’évolution du marché existant Après avoir résumé, les points suivants méritent l’attention :
(1) Les performances du corps de la batterie, telles que la taille de la batterie, la densité d’énergie, la structure multi-onglets, etc.
(2) Efficacité de la production d’assemblage, améliorez continuellement l’efficacité de la production tout en veillant à ce que les coûts de l’équipement ne changent pas de manière significative.
(3) L’automatisation des chaînes d’assemblage de batteries continue de s’améliorer et le rendement de production est plus facile à contrôler. Le temps de production de chaque processus est raisonnablement contrôlé, ce qui raccourcit efficacement le temps de production des batteries au lithium et améliore considérablement les problèmes de forte intensité de main-d’œuvre pour les travailleurs et les coûts de production élevés.
(4) Meilleure compatibilité, adapté à une gamme plus large de produits.
(5) La technologie modulaire est un moyen important d’améliorer l’efficacité.
1.3 Conception de la coque en aluminium (prismatique) chaîne de production et d’assemblage de batteries au lithium
Lors de la conception d’une ligne d’assemblage de production de batteries au lithium à boîtier en aluminium (prismatique), différentes conceptions sont prises en compte en fonction des exigences du client. Compte tenu des problèmes rencontrés et des pratiques correspondantes dans le processus de production, les aspects suivants sont principalement pris en compte :
1. Processus du produit : Cela comprend la taille de la batterie, la taille de la languette et l’épaisseur de la soudure, entre autres.
2. Espace de l’usine : Agencement correct des positions spécifiques des équipements de la ligne de production, optimisation des mécanismes, prise en compte de l’ergonomie, facilité d’utilisation manuelle et maintenabilité.
3. Conception de l’équipement : Plus la structure est simple, plus l’opération est facile.
4. Répartition du rythme de la chaîne de production : L’accent est mis sur l’efficacité des postes de travail goulot. Si l’efficacité n’est pas atteinte, les postes de travail uniques peuvent être modifiés en postes de travail doubles ou multiples. Des performances de sécurité élevées et un rendement au premier passage sont également des considérations clés.
5. Méthode de positionnement du produit : Différentes méthodes de positionnement du produit sont utilisées pour différentes exigences des clients, telles que le positionnement latéral, le positionnement de base sur deux côtés et le positionnement des fixations.
6. Dispositif de prévention de la poussière : Dans la chaîne d’assemblage de batteries cylindriques, chaque appareil nécessitant un dépoussiérage est équipé d’installations correspondantes, telles que des dépoussiéreurs et des brosses.
7. Conception logistique au sein de l’équipement : Cela comprend le transport interne de l’équipement et le transport entre les équipements.
8. Inspection de la qualité : L’ensemble de la chaîne d’assemblage comprend l’inspection CCD, la mesure de l’épaisseur des cellules, l’inspection de l’isolation, la détection de court-circuit, etc.
9. Cohérence dans l’apparence de la ligne de production : Maintenir l’aspect esthétique de l’ensemble de l’équipement.
02 Composition de l’équipement et structure des clés
La disposition générale de la ligne d’assemblage de batteries au lithium à coque en aluminium est la suivante :
(1) Dimensions de l’ensemble de la ligne : longueur × largeur × hauteur = 3700 mm × 7000 mm × 2400 mm (la hauteur n’inclut pas les voyants d’alarme), hauteur de la surface de fonctionnement 900 mm, espacement des équipements 800 ~ 1000 mm.
(2) Apparence : Le châssis porteur de contraintes adopte une structure soudée en tube carré, le cadre d’étanchéité supérieur adopte une structure de profil en alliage d’aluminium et est scellé avec du plexiglas. L’ensemble du couvercle de l’équipement est recouvert de tôle.
(3) Interface de fonctionnement : Chaque appareil est équipé d’un écran tactile fonctionnant indépendamment, et les écrans tactiles de tous les appareils sont intégrés.
(4) Disposition de la ligne entière : La disposition de la ligne d’assemblage de la batterie à coque de plomb est illustrée à la figure.
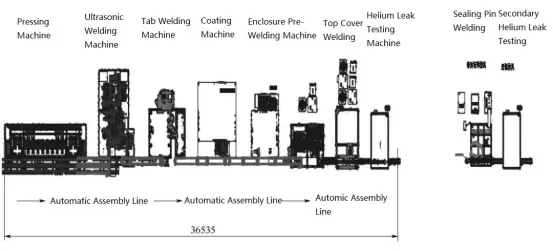
Cette ligne de production est une chaîne d’assemblage entièrement automatisée qui comprend l’ensemble du processus de production des batteries en aluminium, de l’enrouleur à la machine d’essai d’étanchéité à l’hélium. Le processus comprend : l’enroulement vers la ligne de convoyage de pressage à chaud (avec 6 ensembles de robots de manutention sur la bobineuse) → machine de pressage à chaud → machine de soudage par ultrasons → machine de soudage laser à languette → machine d’emballage de cellules → boîtier et machine de soudage par points → machine de soudage laser de couvercle → machine d’essai d’étanchéité à l’air.
2.1 Machine de pressage à chaud
La machine de pressage à chaud est utilisée pour le moulage par compression thermique de cellules de batterie bobinées. Ses principales fonctions comprennent la lecture de codes-barres de cellules, le chargement automatique de cellules A/B, le pressage à chaud, les tests Hi-pot et le rejet des produits défectueux. La température, la pression, le temps, les paramètres d’essai Hi-pot et les résultats du pressage à chaud sont associés au code-barres correspondant et téléchargés dans le système MES. L’équipement se compose principalement de modules pour le chargement/déchargement des cellules, la détection et le pressage à chaud. Cet équipement est le premier processus d’assemblage de cellules de batterie en aluminium, et la qualité de la cellule pressée à chaud affecte directement la qualité des produits traités par la suite. Par conséquent, l’efficacité, la précision de travail et le niveau d’automatisation de cet équipement d’assemblage sont des considérations cruciales. La disposition de l’équipement et le flux de travail sont indiqués dans le diagramme.
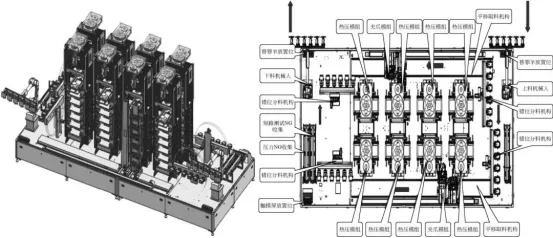
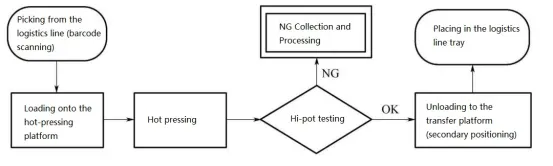
À partir du schéma, il est clair de voir le processus de fonctionnement des cellules de batterie enroulées sur la machine de pressage à chaud. Au cours du processus de travail, l’équipement effectue le pressage à chaud et les tests ultérieurs des cellules de batterie enroulées. Les résultats des tests, y compris la température de pressage à chaud, la pression, le temps et le Hi-pot, sont téléchargés sur le système MES pour une surveillance et un retour d’information en temps réel. Les produits défectueux sont rejetés pour garantir la qualité de traitement.
D’après le schéma de disposition de l’équipement, on peut voir que des composants clés tels que les bras robotisés de chargement et de déchargement, les convoyeurs de transfert, les robots de transfert, les mécanismes de séparation des désalignements et les modules de pressage à chaud jouent un rôle crucial dans l’assemblage des produits semi-finis. Fournissons des explications détaillées pour certains de ces composants.
(1)Mécanisme de distribution des dislocations. La figure montre le mécanisme de distribution des matériaux mal aligné. La fonction du module de positionnement de retournement est la suivante : le mécanisme de retournement utilise un servomoteur de courroie pour réaliser le retournement de la pince et le retournement synchrone de la plaque de connexion. La pince reste toujours horizontale et le retournement est fluide et fiable. Le dispositif de positionnement utilise un cylindre de mâchoire de serrage et un cylindre à double lien pour le serrage et le positionnement ; la surface de contact avec le noyau de la batterie utilise un matériau POM.
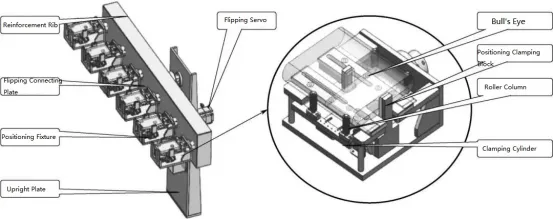
(2)Déplacez le module de haut en bas. Le module de chargement et de déchargement est illustré sur la figure. Ses principales actions sont : la translation à l’aide d’un module d’asservissement à courroie synchrone et d’un entraînement à double courroie pour augmenter la douceur du mouvement du module de chargement et de déchargement ; le module de chargement et de déchargement utilise un servo de courroie pour l’entrée et la sortie des matériaux, et une servocommande indépendante ; les mâchoires de serrage sont levées et abaissées à l’aide d’un cylindre à vis ; Le mécanisme de changement de pas utilise un mécanisme de liaison servocommandé, utilisant le bras central comme référence de positionnement pour réaliser un changement de pas synchrone. Le servo peut contrôler la taille équidistante des mâchoires de serrage pour obtenir différentes conditions de travail de la presse à chaud. Le module de traduction de position synchronise le chargement et le déchargement des matériaux.
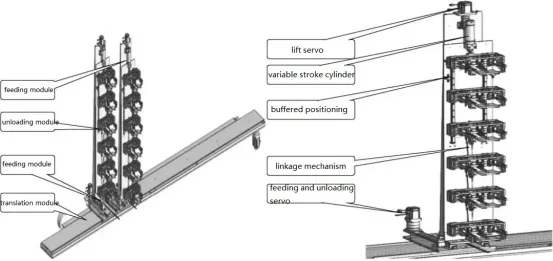
(3) Composants de pressage à chaud. Les composants de pressage à chaud de l’équipement de presse à chaud sont illustrés sur la figure, et leur description détaillée est la suivante :
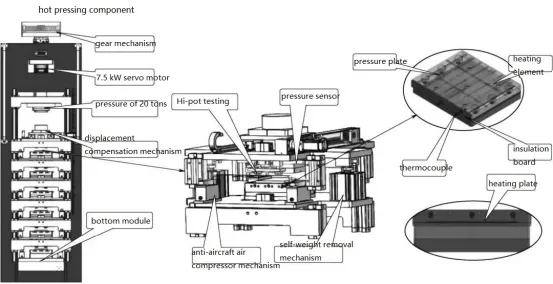
Composants principaux : Cylindre de suralimentation (pression de 20 t, 6 couches), tube chauffant, régulateur de température, capteur de pression, etc.
Mode opératoire : Effectuez des tests de pressage à chaud et de Hi-pot sur les cellules de la batterie.
2.2 Machine de soudage par ultrasons
La machine de soudage par ultrasons complète principalement le soudage par ultrasons des cellules de batterie grâce à des processus tels que le balayage des cellules, l’appariement automatisé des cellules par des bras robotisés, l’étalonnage des cellules et la détection de polarité, la détection et l’étalonnage de la polarité de la plaque d’adaptation, les dispositifs de soudage de la plaque d’adaptation, les dispositifs de soudage des cellules, le placement du couvercle de protection, le soudage par ultrasons et l’extraction de la poussière, la mise en forme des marques de soudure, l’application d’adhésif et l’inspection de l’adhésif, et déchargement automatique. Cet équipement réalise le balayage cellulaire, le soudage par ultrasons, l’application d’adhésif et la liaison d’informations de l’appariement des cellules à l’encapsulation. Il comprend principalement des fonctions telles que le balayage des cellules à l’arrivée, l’étalonnage et l’alimentation des cellules, l’étalonnage et l’alimentation des plaques d’adaptation, l’inspection de l’adhésif et le téléchargement d’informations dans le système MES.
Le mécanisme de préhension est équipé d’un capteur de couleur pour identifier les languettes de polarité des cellules de la batterie, garantissant ainsi que les languettes ne sont pas mal couplées. Les cellules de la batterie sont saisies par le bras robotique sur le tapis roulant entrant. Après avoir subi un positionnement secondaire, ils sont placés dans le plateau, assurant une erreur de désalignement de ≤±0,2 mm pour les languettes de polarité des cellules A/B. Les cellules de la batterie sont placées dans le plateau avec un alignement central. Avant de placer les cellules, les clips élastiques autour du plateau sont ouverts, puis le bras robotique place les cellules dans le plateau, après quoi les clips se ferment, positionnant les cellules au centre du plateau.
Composition de l’équipement et structures clés
Module de chargement de cellule, ligne de cycle de soudage par ultrasons de cellule et module de fixation, feuille d’adaptation, module de chargement de feuille de protection, module de chargement et de déchargement de couverture de feuille de protection, module de soudage à électrode positive et négative par ultrasons, module d’aplatissement d’estampage de soudure, module de collage de noyau de batterie Le module de colle de protection, le module de colle de protection de cellule de batterie, le module de déchargement de cellule de batterie et la détection de colle sont relativement critiques et jouent un rôle essentiel dans l’ensemble assemblé Produit semi-fini. Plusieurs de ces mécanismes sont sélectionnés pour une introduction détaillée.
(1) Module de chargement du noyau de la batterie (comme indiqué sur l’image). Il a les fonctions de chargement automatique des cellules de batterie, de dépoussiérage des matériaux entrants, de prévention anti-fool des matériaux entrants, de tamponnage des matériaux entrants et de fonctions d’alarme de pénurie. Il a également la fonction de scanner le code pour lier les cellules de la batterie.
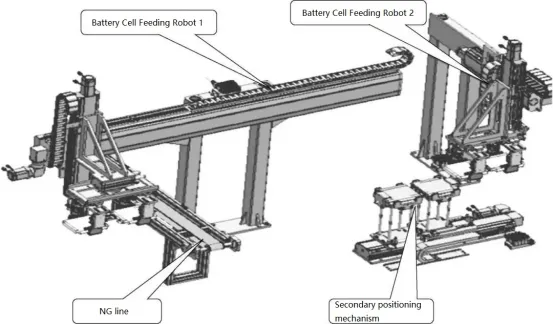
un. Composants principaux : Mécanisme de translation + mécanisme de levage, pince de cellule de batterie, etc.
b. Mode d’emploi : Le processus d’alimentation et de manipulation des cellules de batterie utilise un module de courroie. Le robot d’alimentation 1 saisit un groupe de cellules de batterie de la palette sur la ligne logistique du client et les place dans le mécanisme de positionnement secondaire. Une fois les cellules de la batterie positionnées secondairement, le robot de manutention 2 saisit les cellules et les place sur la ligne de cycle. Si, au cours du processus d’alimentation, il est détecté qu’une paire de cellules de batterie a une seule cellule NG (non bonne), le robot de manutention 1 replacera la cellule NG sur la ligne NG, tandis que la cellule OK (bonne) sera placée dans le mécanisme d’appariement pour une correspondance ultérieure.
(2) Cellule de batterie, ligne de cycle de soudage par ultrasons et module de fixation.
un. Composants principaux : Ligne de cycle, module, blocs de positionnement des bords longs et courts, cylindres, rails de guidage, etc.
b. Mode opératoire (description fonctionnelle sans étapes de fonctionnement spécifiques) : Le robot de manutention 2 introduit les cellules de la batterie dans le dispositif de la ligne de cycle, qui serre les cellules. Le mécanisme de translation déplace le luminaire vers le poste de travail suivant.
Le schéma de principe de la ligne de cycle de soudage par ultrasons est illustré sur la figure.
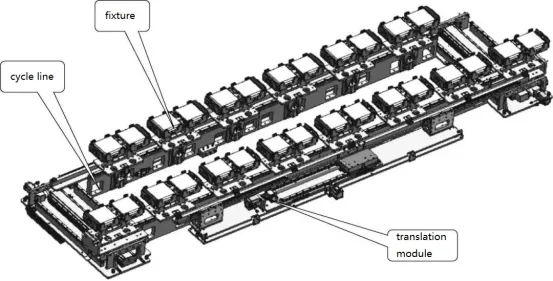
(3) Le module de chargement des plaques d’adaptation et des films de protection (comme indiqué sur le schéma).
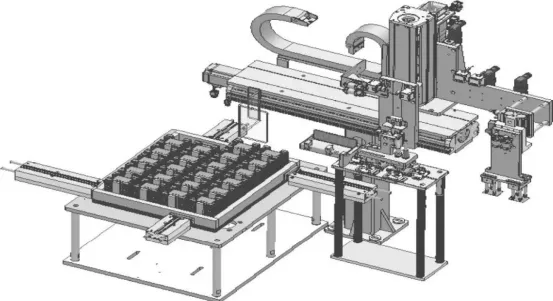
un. Le chargement des plaques d’adaptation cuivre-aluminium comprend des mesures visant à prévenir les erreurs de placement ou d’insertion inversée, telles que la détection de polarité, afin d’éviter les erreurs humaines.
b. Le chargement des plaques de connexion est équipé d’une brosse pour éviter une aspiration inappropriée ou la prise de plusieurs plaques. Il comprend également des fonctions telles que le soufflage d’air et l’agitation sous vide pour assurer une séparation et une détection correctes de plusieurs plaques. Il existe un mécanisme d’élimination des déchets pour stocker les plaques multiples rejetées.
c. La préparation des plateaux de film de protection implique un chargement manuel dans le porte-clip. La buse d’aspiration récupère à chaque fois un ensemble de films protecteurs, ce qui épuise l’alimentation à l’extrémité de l’alimentation. Le plateau tournant (ou le module mobile) pivote jusqu’à la position suivante pour assurer une alimentation ininterrompue en films de protection.
d. Les composants clés comprennent le servomoteur, la vis-mère, le cylindre et la ventouse.
e. La préparation des plateaux de plaques d’adaptation implique que la buse d’aspiration prélève à chaque fois un ensemble de plaques d’adaptation, ce qui épuise l’alimentation à l’extrémité de l’alimentation. Le plateau pivote jusqu’à la position suivante pour assurer une alimentation ininterrompue des plaques d’adaptation.
f. Un seul chargement peut maintenir la production pendant 40 minutes.
(4) Le module de chargement et de déchargement des housses de film de protection (comme indiqué sur le schéma).
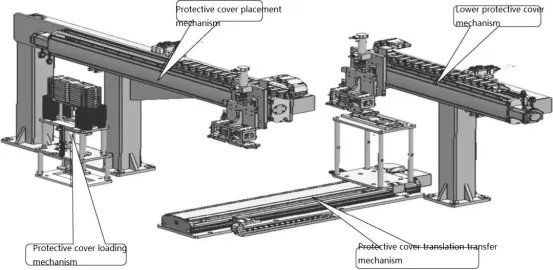
un. Composants clés : servomoteur, vis-mère, cylindre, rail de guidage, etc.
b. Mode opératoire : Dans l’état initial, les capots de protection sont placés manuellement dans le mécanisme de préparation du capot de protection supérieur. Le mécanisme de placement du capot de protection supérieur saisit un ensemble de capots de protection et les déplace vers le poste de travail du capot de protection supérieur, garantissant ainsi que toutes les plaques de protection sont en boucle continue sur la chaîne de montage. Lors du retrait du capot de protection inférieur, le mécanisme du capot de protection inférieur récupère le couvercle du dispositif sur la ligne de montage 2. La plate-forme déplace le couvercle de protection vers le mécanisme de transfert du couvercle de protection, qui se déplace ensuite vers la position supérieure du couvercle de protection. Le mécanisme de placement du capot de protection supérieur récupère le capot de protection et le place dans le dispositif correspondant sur la ligne d’assemblage 1.
c. Un seul chargement peut maintenir la production pendant 40 minutes.
(5) Module de soudage par ultrasons à électrodes positives et négatives (comme indiqué sur le schéma).

un. Composants clés : Plate-forme, machine à souder par ultrasons, cylindre, etc.
b. Processus de fonctionnement : Après le positionnement du montage, le cylindre de levage de l’axe Z monte et la tête de soudage par ultrasons descend pour terminer le processus de soudage. La translation de l’axe X et de l’axe Y est ajustée à l’aide de servomoteurs pour positionner la machine à souder et faciliter le changement d’outillage. La course de l’axe X et de l’axe Y garantit le respect des exigences dimensionnelles pour le changement d’outillage.
(6) Module d’aplatissement de l’empreinte de soudure (comme indiqué sur le schéma). Ce module garantit que le film protecteur reste plat et que les languettes des bornes ne sont pas pliées. Le bloc de pression est fait d’un matériau résistant à l’usure appelé polyéther éther cétone (PEEK).
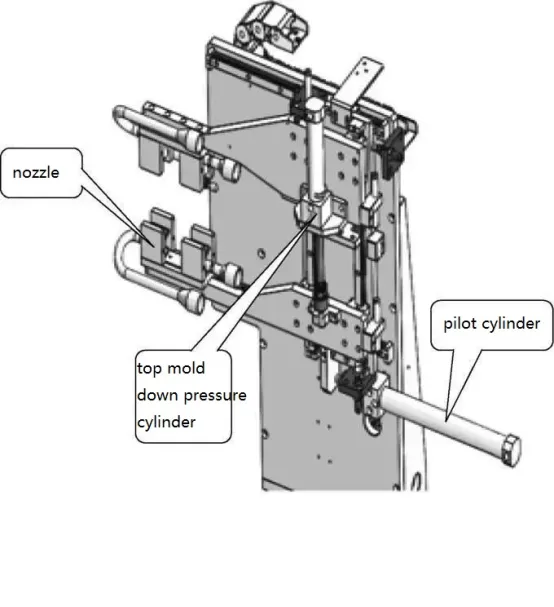
un. Composants principaux : rail coulissant, cylindre, etc.
b. Processus d’action : Une fois que la pince sur le corps de la ligne de circulation est en place, le cylindre d’évitement entraîne les moules supérieur et inférieur pour s’étendre vers l’avant, puis le moule inférieur est poussé vers le haut, le moule supérieur est pressé vers le bas et la marque de soudure est nivelée. Par la suite, le moule supérieur se déplace vers le haut, le moule inférieur se déplace vers le bas et le cylindre d’évitement entraîne les moules supérieur et inférieur pour rétracter la pince d’évitement de position.
2.3 Machine de soudage laser de plaque d’adaptation
1) Composition de l’équipement
Les principales fonctions de l’équipement de la machine de soudage laser de plaque d’adaptation comprennent le chargement automatique du capot supérieur et des cellules de batterie, et le soudage de la pièce de connexion et du capot supérieur en un seul corps par soudage au laser, le déchargement automatique après dépoussiérage et l’application de colle, comme indiqué sur la figure.
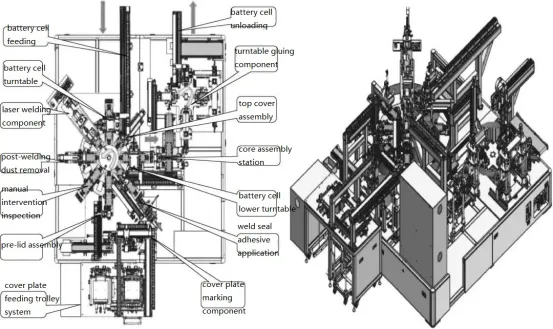
Dimensions de l’équipement : Longueur × Largeur × Hauteur = 2800mm × 3800mm × 2300mm.
Apparence : Le châssis porteur adopte une structure de soudage à tube carré et le cadre d’étanchéité supérieur adopte une structure de profil en alliage d’aluminium, scellée avec du verre organique.
Interface de fonctionnement : L’équipement est équipé d’un écran tactile indépendant pour le fonctionnement, et tous les écrans tactiles de l’équipement sont intégrés.
2) Structures clés
Sur le schéma ci-dessus, on peut voir que le mécanisme d’alimentation de la plaque de recouvrement, l’ensemble du couvercle supérieur, le module de soudage laser, le mécanisme de dépoussiérage post-soudage et le composant d’application de l’adhésif de soudure sont cruciaux et jouent un rôle essentiel dans l’assemblage du produit semi-fini. Nous fournirons des introductions et des explications détaillées pour certains de ces mécanismes.
(1) Mécanisme d’alimentation de la plaque de recouvrement
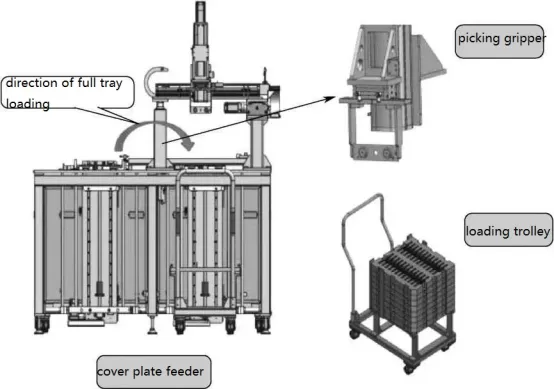
a.Fonction : Le mécanisme d’alimentation de la plaque de recouvrement permet l’alimentation des plaques de couverture et comprend des fonctionnalités telles que le positionnement et le transfert du plateau.
b. Composants clés : Mécanisme de levage, mécanisme de positionnement du plateau, petit chariot, etc.
c. Exigences : Chargement unique pour répondre à la production continue de l’équipement pendant 30 minutes ; un chariot de chargement en service et un chariot de rechange, et trois chariots de déchargement ; Précision de positionnement secondaire du plateau de ≤0,1 mm.
(2) Ensemble du couvercle supérieur
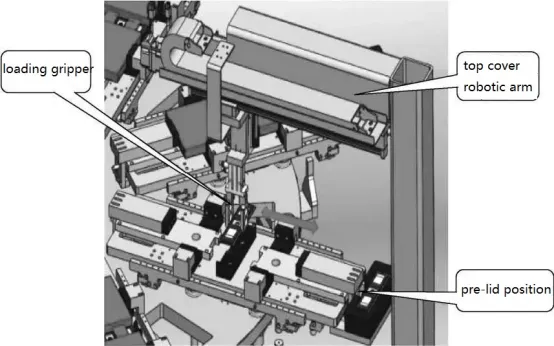
a.Fonction : Pour saisir la plaque de recouvrement codée et la placer sur le plateau tournant.
b. Composants clés : module de courroie synchrone de translation, module de vis de levage, griffe de préhension, etc.
c. Exigences : Saisie fiable sans chute ni dommage de matériau, précision répétitive du fonctionnement du mécanisme ≤±0,05 mm, conception flexible du bras robotique, les pièces sans contact du bras robotique qui entrent en contact avec le produit doivent utiliser des matériaux non contaminants.
(3) Module de soudage laser (comme indiqué sur le schéma).
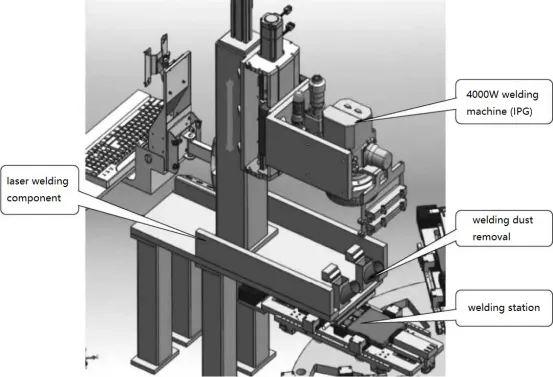
a. Fonction : Pour souder la plaque de recouvrement et la languette ensemble à l’aide de la machine de soudage laser.
b. Composants clés : Plate-forme de soudage, support de cellule, etc.
(4) Mécanisme de dépoussiérage post-soudage (Figure 21) : Le cylindre de levage s’abaisse, couvrant la zone de soudage pour créer un espace étanche pour l’extraction de la poussière. La vitesse du flux d’air d’aspiration est de ≥12 m/s et la vitesse est réglable en continu dans la plage maximale.
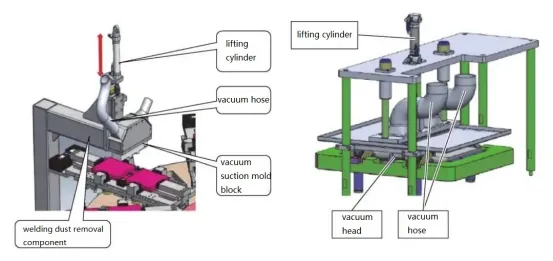
un. Composants clés : Vérin de levage, moteur rotatif, orifice d’aspiration, etc.
b. Processus de fonctionnement : Le luminaire se déplace vers la station de dépoussiérage ; Le cylindre descend et le moteur tourne pour effectuer le dépoussiérage.
(5) Composant d’application de l’adhésif de soudure (comme indiqué sur le schéma).
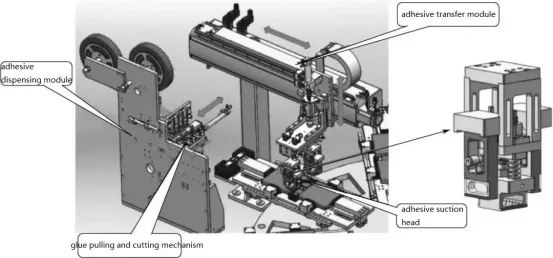
a.Fonction : Appliquez un adhésif protecteur sur le dessus de la zone de soudage de la languette.
b. Composants principaux : Mécanisme de tirage de colle, mécanisme de coupe de colle, mécanisme d’application de colle, ensemble de rouleau de colle, etc.
c. Exigences : Longueur du ruban réglable et placement de l’adhésif ; détection du vide et avertissement en cas de bande de sauvegarde défectueuse ; fonction de détection de présence de bande ; dispositif de mise en forme de la zone de soudage avant l’application de la colle ; rendement d’application de l’adhésif ≥99,8 %.
2.4 Machine d’emballage de film
1. Principales fonctions de l’équipement :
La machine d’emballage de film est principalement utilisée pour le façonnage automatique des cellules de batterie, l’alimentation automatique du séparateur et du plateau inférieur, l’emballage de la cellule avec le séparateur, l’application d’adhésif sur les surfaces latérales et inférieures, les tests CCD, etc. La disposition de l’équipement est illustrée dans le schéma.
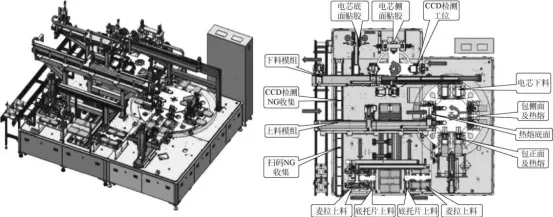
Voici les spécifications de base de l’équipement :
· Dimensions extérieures de l’équipement : 3100mm × 4000mm × 2300mm.
· Rendement de l’équipement : ≥99,8 % (hors matériaux défectueux entrants).
· Disponibilité de l’équipement : ≥98 % (en se référant uniquement aux pannes causées par des problèmes liés à l’équipement).
2) Structures clés
D’après le schéma d’implantation de la machine d’emballage de film, on peut observer que le mécanisme d’application de l’adhésif inférieur, le mécanisme de séparation et le mécanisme d’alimentation du plateau inférieur, le mécanisme du film d’emballage avant, le mécanisme d’application de l’adhésif inférieur et le mécanisme du plateau tournant d’application latérale de l’adhésif sont tout à fait cruciaux et jouent un rôle essentiel dans l’assemblage du produit semi-fini. Expliquons en détail certains de ces mécanismes.
(1) Disposition du séparateur et de l’alimentation du plateau inférieur (comme indiqué sur le schéma).
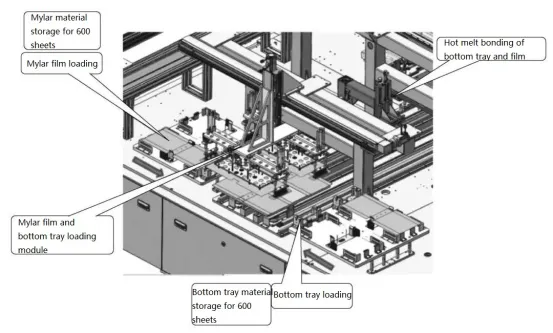
un. Composants clés : Ensemble d’alimentation manuel en Mylar (1 ensemble), bras robotique d’alimentation en Mylar (1 ensemble), boîte de matériau du plateau inférieur (1 ensemble), bras robotique d’alimentation du plateau inférieur (1 ensemble), plate-forme thermofusible du plateau inférieur en Mylar (1 ensemble), mécanisme de fusion chaude (1 ensemble).
b. Processus de fonctionnement : Le bras robotique place le plateau inférieur sur le dispositif thermofusible → Le bras robotique d’alimentation en Mylar place le film sur le dispositif thermofusible → Le dispositif thermofusible est déplacé vers la station de thermofusion → Processus de fusion à chaud → Le bras robotique d’alimentation et de déchargement du film de la table tournante attend à la position de récupération.
(2) Station de film d’habillage frontal (comme indiqué sur le schéma). La disposition de l’emballage de film et du plateau tournant thermofusible est illustrée dans le schéma.
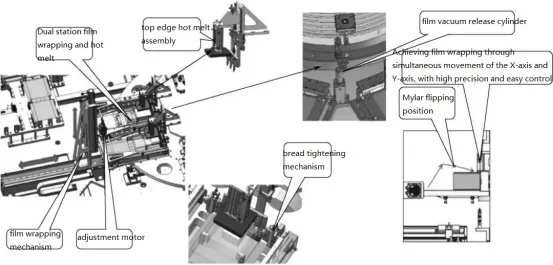
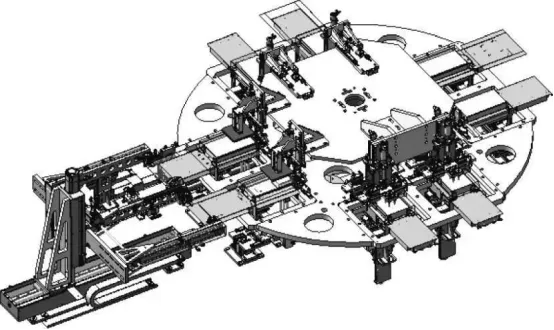
un. Composants clés : Fixations de poste de travail (8 ensembles), ensemble thermofusible (1 ensemble), ensemble d’emballage de film (1 ensemble), mécanisme de film pliant (1 jeu), mécanisme d’ouverture de luminaire (3 jeux).
b. Processus de fonctionnement : Chargement du film → Chargement de la cellule → Thermofusible de la surface inférieure → Emballage du film avant → → Pliage du film latéral → Thermofusible de la surface latérale → Déchargement.
(3) Mécanisme d’application de l’adhésif par le bas (comme indiqué sur le schéma).
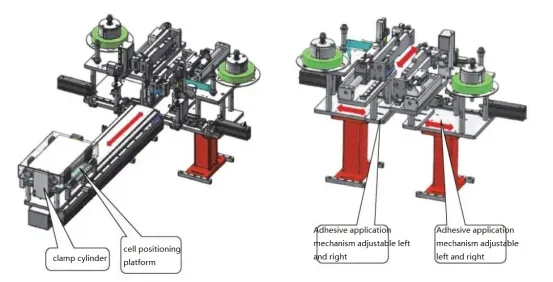
un. Il y a des rubans adhésifs en forme de L des deux côtés du fond ; La longueur et la position des bandes peuvent être ajustées, avec des positions adhésives symétriques et un écart de ±0,5 mm. Le processus adhésif ne doit pas provoquer de pression ou de rayures sur la cellule de la batterie.
b. Un mauvais support adhésif peut être détecté et dispose d’une fonction d’avertissement. Après l’application de la colle, la présence ou l’absence de la colle est inspectée à l’aide d’un capteur de marque de couleur.
c. La sauvegarde manuelle de l’adhésif est effectuée à la main.
d. Fonction : Après avoir enveloppé la cellule de batterie, un adhésif est appliqué pour la fixer sur le plateau inférieur en forme de « L ».
e. Composants clés : Rouleau de colle, application de colle et assemblage de coupe, etc.
f. Exigences : Taux de défauts d’adhésif ≥ 99,6 % ; l’application de l’adhésif doit être continue sans aucun cas de rupture du ruban ; Les rubans adhésifs doivent être appliqués sur la cellule de la batterie sans plis ni décollement.
(4) Plateau tournant d’application d’adhésif latéral (comme indiqué sur le schéma).
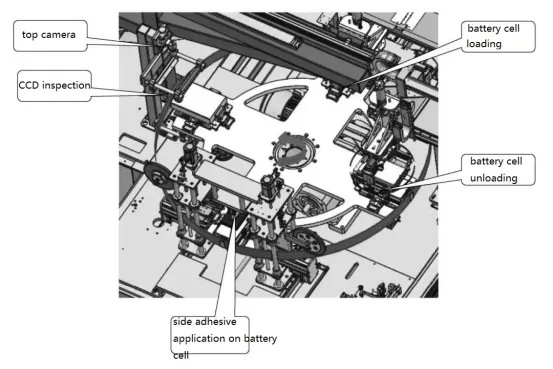
a.Il y a une bande de ruban adhésif de chaque côté.
b. La longueur et la position du ruban peuvent être ajustées, avec des positions d’adhésif symétriques et un écart de ±0,5 mm.
c. Le processus adhésif ne doit pas provoquer de pression ou de rayures sur la cellule de la batterie.
d. Un mauvais support adhésif peut être détecté et dispose d’une fonction d’avertissement.
e. Après l’application de la colle, la présence ou l’absence de la colle est inspectée à l’aide d’un capteur de marque de couleur.
f. Le support manuel de l’adhésif est effectué à la main.
g. Fonction : Après avoir enveloppé la cellule de batterie, un adhésif est appliqué des deux côtés de la cellule de batterie pour la fixer en forme de « U ».
h. Composants clés : Rouleau de colle, application de colle et assemblage de coupe, assemblage de vis mère sur l’axe X, etc.
i. Exigences : Taux de défauts d’adhésif ≥ 99,6 % ; l’application de l’adhésif doit être continue sans aucun cas de rupture du ruban ; Les rubans adhésifs doivent être appliqués sur la cellule de la batterie sans plis ni décollement.
2.5 Machine de pré-soudage de la coque
1) Fonction principale de l’équipement
La disposition de la machine de pré-soudage de la coque est illustrée dans le schéma.
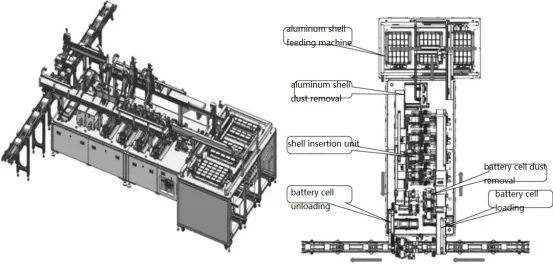
L’équipement de la machine de pré-soudage d’insertion de boîtier est utilisé pour insérer automatiquement des piles de boîtier en aluminium prismatique dans le boîtier. La fonction principale
Les NS de l’équipement comprennent : le chargement du boîtier en aluminium, le chargement automatique de la batterie et la lecture de code, le dépoussiérage du boîtier en aluminium et du noyau de la batterie, l’insertion du noyau de la batterie, le déchargement de la batterie, la liaison et le téléchargement d’informations (MES), etc.
Principaux paramètres techniques de l’équipement.
Dimensions hors tout de l’équipement : 2850mm×1900mm×2500mm.
Taux de rendement de l’équipement : ≥99,8 % (ne se réfère qu’aux défauts causés par l’équipement).
Taux de disponibilité des équipements : ≥99% (ne concerne que les pannes causées par les équipements).
Intervalle de temps de chargement de la coque en aluminium : ≥25 min ; Les paramètres de dépoussiérage sont automatiquement enregistrés, et le noyau de la batterie et la coque en aluminium ne seront pas endommagés pendant le processus de dépoussiérage. Pas de particules visibles qui peuvent être essuyées.
Pour contrôler l’épaisseur de la cellule, la force de serrage doit être augmentée : 10 ~ 50 kgf (1 kg f = 9,81 N) est réglable, la précision de débogage est de ±5 kgf, et la pression de serrage et la valeur de vide sont réglables numériquement.
Précision du contrôle de la poussée pendant le processus de tubage : ±5 % de la valeur de réglage ; Le boîtier et les cellules de la batterie sont positionnés deux fois avant d’être insérés dans le boîtier et ont pour fonction d’élargir l’ouverture de la coque. Le noyau de la batterie adopte un mécanisme de guidage entièrement enveloppant pour guider le noyau de la batterie dans le boîtier. L’embouchure de la coquille en aluminium ne peut pas être touchée du tout.
Écart de positionnement : 0,5 mm.
Répétabilité du fonctionnement du mécanisme : écart ≤±0,05 mm.
2)Structures clés
À partir du schéma de disposition de l’équipement de la machine de pré-soudage de coque illustré ci-dessus, plusieurs structures clés peuvent être identifiées, notamment le mécanisme d’alimentation de la coque en aluminium, la coque en aluminium et la cellule de batterie, le mécanisme de nettoyage du capot supérieur, le mécanisme d’insertion de la cellule de batterie et le mécanisme d’alimentation des cellules de batterie. Ces structures jouent un rôle essentiel dans l’assemblage du produit final. Donnons des explications détaillées pour quelques mécanismes sélectionnés.
(1) Module d’alimentation en coque en aluminium (comme indiqué sur le schéma)
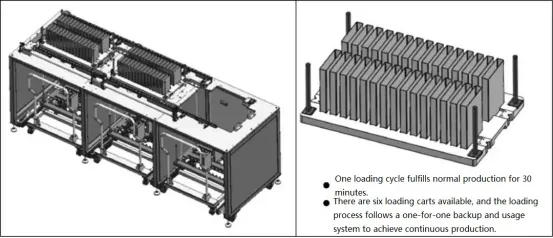
un. Fonction : réalise l’alimentation des coques en aluminium et dispose de fonctions telles que le positionnement et le transfert de palettes.
b. Composants principaux : dispositif de chargement automatique de palette de coque en aluminium d’empilage, palette de coque en aluminium, chariot de transport de matériaux, etc.
c. Exigences : L’intervalle d’alimentation de la coquille en aluminium est ≥ 20 minutes ; Équipé d’un mécanisme de guidage et d’un mécanisme de positionnement fiables.
(2) Noyau de la batterie et mécanisme de dépoussiérage du boîtier (comme indiqué sur la figure).
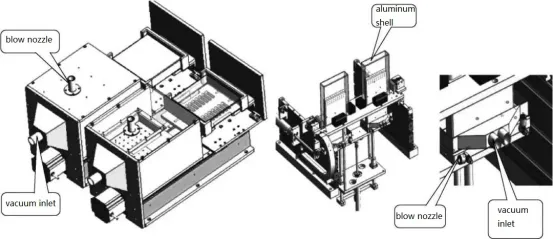
a.Fonction : Le boîtier est nettoyé verticalement et le processus de soufflage couvre tous les angles sans angles morts évidents. L’ouverture de la coque est traitée de manière ciblée.
b. Composants principaux : Mécanisme de dépoussiérage, mécanisme de translation de cylindre, etc.
3. Mécanisme d’insertion de la cellule de batterie (comme indiqué sur le schéma).
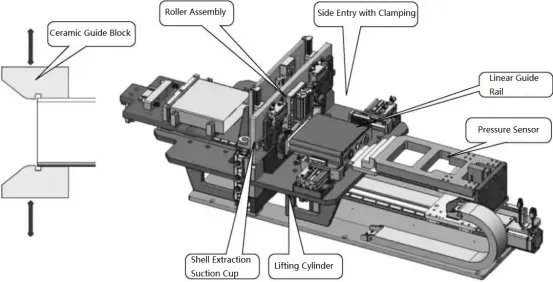
Lors de l’insertion de la coque, la coque en aluminium est sécurisée et la cellule de batterie est serrée et poussée vers l’avant pour protéger les languettes de la cellule.
b. Le processus d’insertion de la coque utilise des blocs de guidage en céramique avec un grand angle d’inclinaison pour éviter le grattage de la coque en aluminium, ainsi que l’endommagement ou la rayure du séparateur.
c. Des matériaux céramiques sont utilisés dans la zone de contact avec la coque en aluminium.
d. Après l’insertion, un espace de 4 mm est maintenu pour la station de pressage suivante, ce qui nécessite que le support pénètre dans la coque et assure une profondeur d’insertion constante de la coque.
e. Précision de positionnement : Avec une structure d’extraction de la coque à ventouse, la coque est fermement positionnée, atteignant une précision de positionnement de ±0,1 mm. L’ensemble du processus d’insertion de la coque est surveillé pour la pression, et un poids standard est fourni pour l’étalonnage sans démonter le capteur.
f. Le mécanisme de nettoyage nettoie la surface de soudure de la cellule de batterie et du couvercle de la coque en soufflant par les côtés supérieurs et en aspirant par le bas.
g. L’angle et la hauteur de soufflage de la buse peuvent être librement ajustés, assurant un flux d’air uniforme et formant un rideau d’air efficace.
h. Pressage du couvercle : Principalement utilisé pour les tests Hi-pot de la cellule de batterie après l’insertion. Avant d’appuyer sur la pression, la poussière autour de la plaque de recouvrement est retirée et la plaque de couverture est pressée dans la coque.
i. Fonction : Pour insérer la cellule de batterie dans la coque.
j. Composants principaux : mécanisme d’insertion de la coque, ensemble de vis mère, mécanisme d’aspiration par extraction de la coquille, etc.
4. Mécanisme d’alimentation des cellules de batterie (comme indiqué sur le schéma).
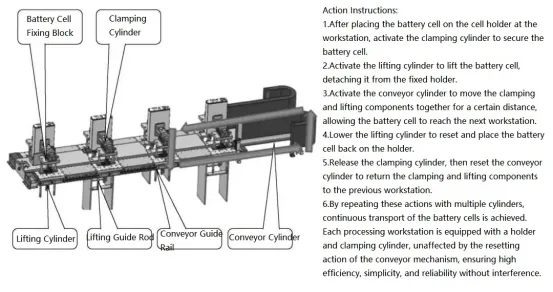
a. Fonction : Utilisé pour le transport des cellules de batterie après insertion dans la coque.
b. Composants principaux : mécanisme de serrage de cellule de batterie, cylindre de levage, mécanisme de convoyeur, etc.
2.6 Machine de pré-soudage
1. Fonctions principales de l’équipement
La disposition de la machine de pré-soudage est illustrée dans le schéma.
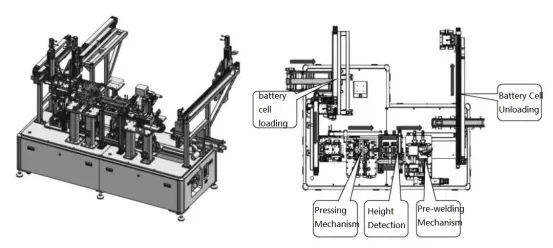
La disposition de l’équipement de la machine de pré-soudage est utilisée pour le pré-soudage de la coque en aluminium prismatique et de la plaque de recouvrement. Les principales fonctions de l’équipement comprennent l’alimentation et le balayage automatiques de la batterie, le pressage, la détection de hauteur, le soudage laser, le déchargement de la batterie et la liaison/le téléchargement d’informations vers le MES (Manufacturing Execution System).
(1) Principaux paramètres techniques de l’équipement :
Dimensions hors tout : 3000mm × 1800mm × 2500mm.
Rendement de l’équipement : ≥99,8 % (en référence aux défauts causés uniquement par des raisons d’équipement).
Taux d’utilisation de l’équipement : ≥99 % (en référence à la défaillance de l’équipement causée uniquement par des raisons d’équipement).
Hi-pot testing : Temps de test allant de 0,5 s à 5 s, réglable dans la plage de 1 s à 100 s. La marque utilisée est Hioki avec une précision de ±5%. La tension d’essai (DC) entre les bornes positives et négatives est de 100 V, avec une plage (DC) de 0 V à 500 V et des incréments de 50 V.
Écart de positionnement : 0,5 mm.
Répétabilité du fonctionnement du mécanisme : Déviation ≤±0,05 mm.
2) Structures clés
D’après le schéma d’implantation de l’équipement de la machine de pré-soudage, on peut voir que le mécanisme de mise en forme et de pré-pression des cellules de batterie, le module d’essai par étapes et de court-circuit, le mécanisme de pressage, le mécanisme de pré-soudage, ainsi que le mécanisme d’étanchéité et de pressage du couvercle sont essentiels et jouent un rôle crucial dans l’assemblage du produit semi-fini. Expliquons en détail certains de ces mécanismes.
(1) Mécanisme de mise en forme et de pré-pressage des cellules de batterie (2 ensembles, comme indiqué sur la figure)
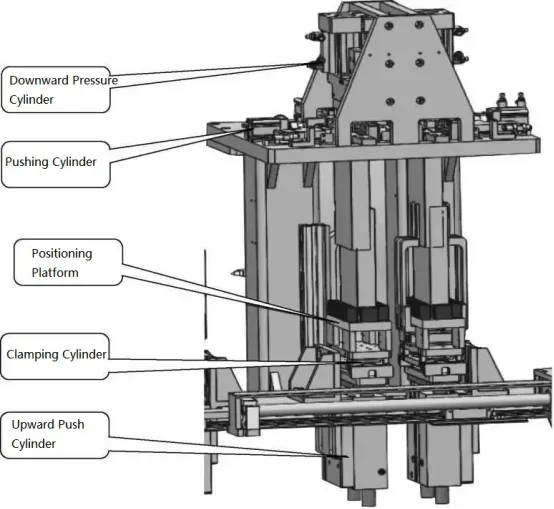
a. Fonction : Pour façonner et appuyer sur le couvercle supérieur de la cellule de la batterie après l’avoir insérée dans le boîtier.
b. Composants principaux : Positionnement des composants, montage de levage et de pré-pressage, etc.
c. Exigences : Il doit être capable de prérégler la limite supérieure de pression, de fournir une fonction d’alarme et d’arrêt lorsque la limite est dépassée pour éviter d’endommager la cellule et le boîtier de la batterie. La plage de réglage de la pression doit être de 200 à 1000N. Après avoir appuyé, le couvercle supérieur ne doit pas avoir de dommages ou de débris, et il ne doit pas y avoir de bavures, de bavures ou de rayures autour de l’ouverture du boîtier. Le module de pressage doit être conçu avec une modularité pour un changement facile et commode.
(2) Mécanisme d’étanchéité et de pressage du couvercle (comme indiqué sur la figure)
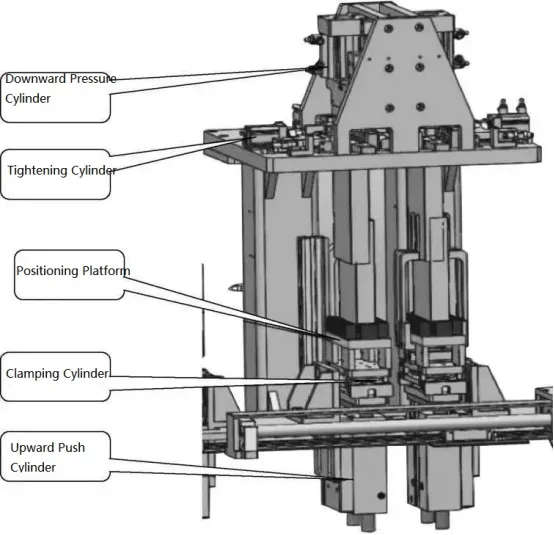
La séquence de fonctionnement spécifique du mécanisme d’étanchéité et de pressage du couvercle est la suivante :
Action du cylindre de serrage : Serre la cellule de la batterie tandis que le cylindre de poussée vers le haut soulève la cellule en position d’assemblage.
b. Action du cylindre de centrage : Serre la cellule de la batterie, l’aligne dans la bonne position et libère le cylindre de serrage.
c. Action du cylindre de serrage : Sécurise la coque et la plaque de recouvrement à l’intérieur du moule de pressage, en veillant à ce que l’étape soit à moins de 0,20 mm. Le moule a des dimensions précises, une grande douceur, permettant un mouvement fluide de la coque et de la plaque de recouvrement à l’intérieur.
d. Action d’assemblage de la ventouse : Maintient la coquille et la tire vers l’extérieur pour éviter une déformation significative vers l’intérieur.
e. Action du cylindre de pression vers le bas : guidé par le moule de pressage, presse la plaque de recouvrement dans la coque, tout en incorporant des limiteurs mécaniques pour éviter une pression excessive.
f. Chaque cylindre a une longueur de course réglable et les pièces clés sont équipées de coussins hydrauliques et de limiteurs de réglage fin.
(3) Mécanisme de pré-soudage (comme indiqué sur la figure)
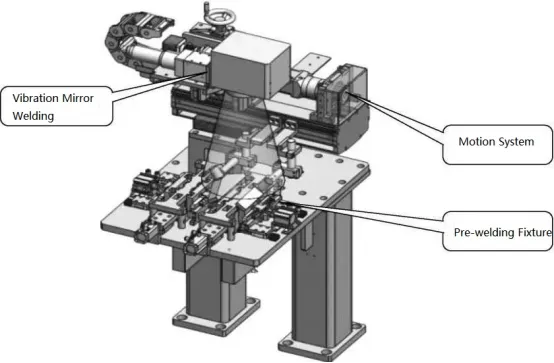
Le « mécanisme de pré-soudage » est principalement composé d’un système de mouvement et d’un dispositif de pré-soudage.
a. Fonction : Mise au point laser, mesure de défocalisation, protection contre les gaz de soudage et le système de mouvement fait glisser la tête laser pour scanner la trajectoire de soudage.
b. Composants principaux : Les axes X et Y du système de mouvement adoptent des servomoteurs, des machines de soudage laser, etc. Le capteur de détection de pas utilise un profilomètre 2D, avec une précision de détection de pas de ±0,02 mm et des pas inférieurs à 0,2 mm.
2.7 Machine de soudage laser à capot supérieur
1) Fonctions principales de l’équipement
La disposition de la machine de soudage laser du capot supérieur est illustrée dans la figure ci-dessous. Cet équipement est principalement utilisé pour le soudage au laser du couvercle supérieur de la cellule de batterie après pré-soudage et pour les tests Hi-pot. Ses principales fonctions comprennent la lecture automatique de codes-barres pour le chargement et le déchargement des cellules, la manipulation automatique des plaques de protection, le serrage et le positionnement, le soudage par scellage laser, les tests Hi-pot, la mise en tampon NG et le transport du processus.
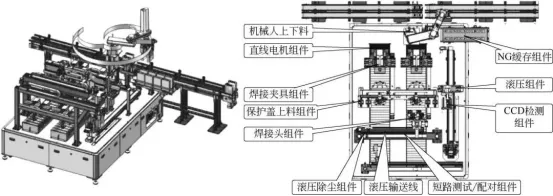
Dimensions hors tout de l’équipement : 3000mm×4500mm×2200mm.
Le taux de rendement de l’équipement pour la première fois est de ≥98,5 %, le taux excellent pour la deuxième fois est de ≥99,5 % (hors matériaux entrants défectueux) et le taux d’utilisation est de ≥98 %.
Vitesse de soudage ≥150mm/s, CMK≥1.33.
Résistance à la pression de soudage laser>10kgf, CMK≥1.33.
Puissance de sortie de la machine de soudage laser et précision du contrôle de la pression du luminaire : valeur de consigne ±5%, CMK≥1,33.
Qualité de soudage (précision de positionnement du soudage ±0,1 mm, écart de largeur de soudure ≤±0,1 mm), cohérence CMK ≥1,33.
La propreté environnementale de la cavité de protection en contact avec le produit pendant le processus de soudage au laser est supérieure à l’exigence de niveau 100 000.
Les fonctions de l’équipement peuvent répondre aux besoins d’organisation, de communication et d’amarrage des équipements de traitement avant et arrière.
2) Structures clés
À partir du schéma d’aménagement de la machine de soudage laser du capot supérieur, nous pouvons identifier plusieurs composants critiques tels que le mécanisme d’alimentation, l’ensemble de positionnement, le composant d’alimentation du couvercle de protection, la mise en tampon NG, le composant d’inspection mobile, le composant d’inspection CCD, le composant de manutention NG, le composant de déchargement et le composant de tête de soudage. Ces composants jouent un rôle crucial dans l’assemblage du produit semi-fini. Présentons en détail quelques mécanismes sélectionnés.
(1) Mécanisme d’alimentation de la machine de soudage laser du capot supérieur (comme indiqué sur la figure).
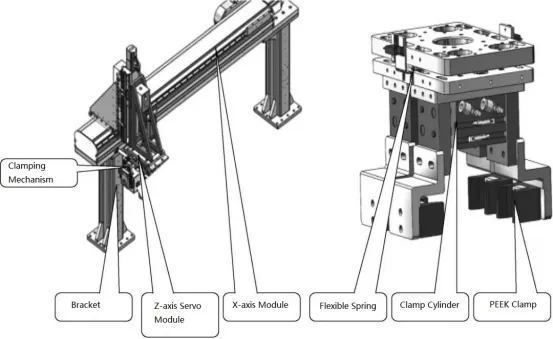
un. Le mécanisme de chargement comprend un support de chargement, un module d’axe X, un module d’axe Z, un mécanisme de serrage, etc. Utilisez la pince de chargement pour saisir les noyaux de batterie sur la ligne logistique de matériaux entrants. Prenez deux piles à la fois et placez-les sur le dispositif de soudage. Il y a 4 ensembles de dispositifs de soudage. Deux piles sont placées à chaque fois et les piles sont déchargées deux fois.
b. Le mécanisme de levage du manipulateur est protégé de manière flexible. Lorsqu’il rencontre une résistance avant d’atteindre la position réglée pendant le processus de descente, il se lève immédiatement et émet une alarme sonore et visuelle.
c. Le manipulateur a une fonction de protection contre l’alimentation et les gaz. Lorsque la batterie est serrée et que la batterie est coupée, la batterie ne tombera pas pendant au moins 30 minutes.
d. Positionnez et fixez le noyau de la batterie de manière à ce que sa position soit précise et fiable pendant le soudage. Le bloc de serrage est fabriqué à partir de matériaux résistants aux hautes températures. La précision de positionnement de la soudure est de ±0,1 mm et l’écart de largeur de la soudure est de ≤±0,1 mm.
e. La direction de la hauteur du noyau de la batterie est positionnée en fonction de la surface supérieure du capot supérieur. Une fois le noyau de la batterie positionné et serré, la hauteur de la surface supérieure du couvercle supérieur du noyau de la batterie dépasse la surface supérieure du bloc de serrage de 1,5 ~ 2 mm (déterminée par le client). L’erreur de niveau de la surface supérieure est de ≤0,1 mm, l’erreur de répétabilité dans le sens de la hauteur est de ≤0,05 mm.
f. Pendant le processus de positionnement et de serrage du noyau de la batterie, le bloc de serrage ne produit pas de frottement de glissement avec le noyau de la batterie. Un dispositif suiveur est utilisé pour éviter de pincer ou de rayer le noyau de la batterie. Une fois le noyau de la batterie positionné et serré, l’espace entre le bloc de serrage et le noyau de la batterie est de ≤0,05 mm (pièce standard).
g. La pression du cylindre de positionnement et de serrage de la cellule est réglable et la valeur de la pression d’air fluctue <0,05 MPa.
(2) Composant de positionnement supérieur (comme indiqué sur l’image).
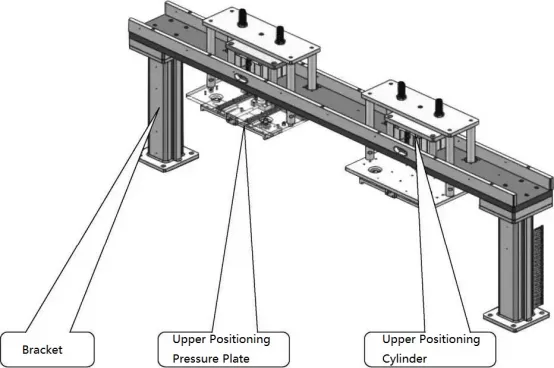
Le processus d’action spécifique est le suivant :
un. La pince de la batterie se déplace en position de positionnement supérieure via le moteur linéaire A/B.
b. Contrôlez l’électrovanne du cylindre de positionnement des côtés long et court de la pince de batterie pour passer en position de décharge moyenne.
c. Le cylindre mobile de positionnement supérieur entraîne la plaque de pression de positionnement supérieure pour appuyer sur le positionnement de la batterie.
d. Une fois le positionnement supérieur terminé, les électrovannes latérales longues et courtes passent à la pression normale et le cylindre mobile de positionnement supérieur monte.
(3) Ensemble de chargement du couvercle de protection (comme indiqué sur l’image).
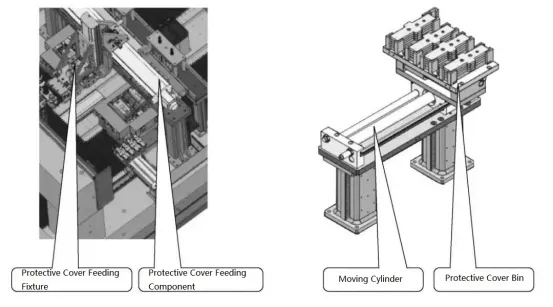
Les mesures spécifiques sont les suivantes :
un. Une fois le positionnement supérieur terminé, la batterie est déplacée vers la position du couvercle de protection supérieur pour l’alimentation du couvercle de protection.
b. Une fois le soudage terminé, le système se met en position de déchargement pour retirer le couvercle de protection et décharger la batterie.
Remarque : Le couvercle de protection peut être remplacé sans arrêter la machine. Le couvercle de protection est utilisé pour protéger la colonne d’électrodes, empêchant la contamination de la colonne d’électrodes, du code QR, du film antidéflagrant et du trou d’injection des éclaboussures de soudage.
(4) Composante d’inspection CCD (comme le montre la figure).
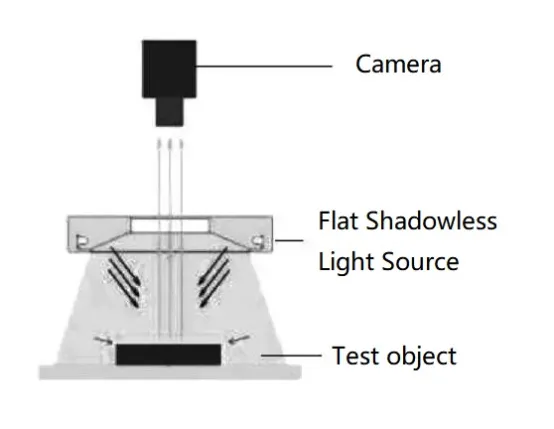
Après le soudage, les cellules de la batterie sont transportées vers le composant d’inspection mobile à l’aide du module de bras robotisé. Le composant d’inspection mobile est équipé de deux jeux de pinces et dispose de trois stations : position d’alimentation, position d’inspection et position de déchargement. Le composant d’inspection CCD est équipé d’une caméra permettant de détecter les défauts tels que les piqûres, les évents, les discontinuités de soudure, la porosité et les soudures incomplètes dans le cordon de soudure (comme le montre la figure).
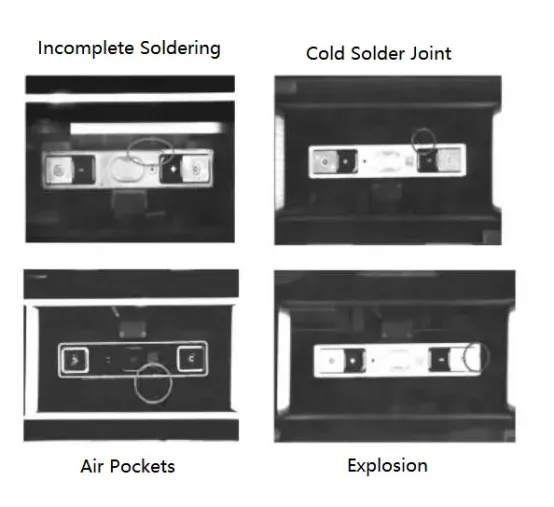
2.8 Testeur de fuite d’hélium à pression positive
1. Fonctions principales de l’équipement
Le schéma ci-dessous illustre l’équipement d’essai d’étanchéité à l’hélium à pression positive. Cet équipement est principalement utilisé pour tester les performances d’étanchéité des cellules de batterie à coque en aluminium prismatique après le soudage au laser du couvercle supérieur. Il utilise une méthode sous vide pour détecter l’état d’étanchéité du couvercle supérieur après le soudage. Le processus de travail est le suivant : une fois le capot supérieur soudé au laser, les cellules de batterie testées sont introduites dans la machine via un convoyeur d’alimentation et le code QR du capot supérieur est lu. Le bras robotisé de tri place ensuite les cellules de batterie testées dans la chambre d’essai. La chambre est évacuée jusqu’à ce que la valeur de pression négative définie soit atteinte, puis la source de vide externe est fermée. Le testeur d’étanchéité aux gaz est utilisé pour tester l’étanchéité interne aux gaz de la cellule de la batterie. Cet appareil permet de déterminer si les pièces testées sont qualifiées.
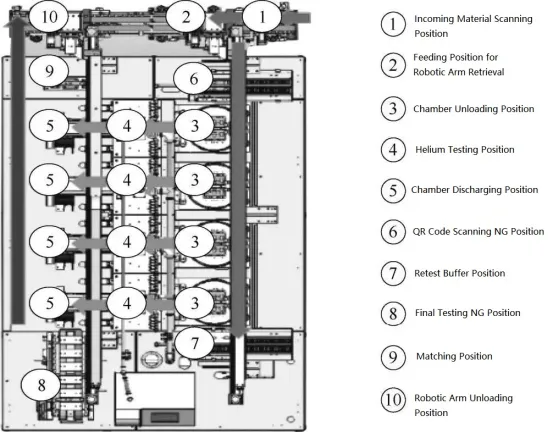
Le système est conçu et fabriqué en stricte conformité avec les exigences de l’acheteur, en utilisant une conception modulaire, en tenant pleinement compte des exigences de détection des fuites de l’acheteur et en utilisant autant que possible des modules et des composants standardisés pour assurer la fiabilité et la maintenabilité du système et répondre aux exigences du fabricant. Spécifiez les indicateurs techniques.
Les indicateurs de base de l’équipement sont les suivants :
Taux de rendement de l’équipement : ≥99,8 % (sauf matériaux entrants défectueux).
Taux d’utilisation de l’équipement : ≥99% ; Taux de fausses détections : ≤0,3%.
Norme d’inspection à l’hélium : ≤9,9×10-7Pa·m3/s.
2) Structure des clés
Cet équipement se compose des dispositifs suivants : dispositif manipulateur d’entrée/sortie de pièce, glissière de boîte, dispositif d’évacuation/remplissage d’hélium, dispositif de détection de fuite de boîte à vide, dispositif de remplissage et d’élimination de l’hélium et dispositif de contrôle électrique. Le schéma de configuration de l’équipement d’inspection de l’hélium à pression positive de la figure 48 montre que le manipulateur d’entrée/sortie de la pièce, le dispositif d’évacuation/de remplissage d’hélium, etc. sont essentiels et jouent un rôle essentiel dans l’ensemble du produit semi-fini assemblé. Plusieurs de ces mécanismes sont sélectionnés pour plus de détails. Introduction.
(1) Vérifiez le plateau tournant. La fonction principale de la plaque tournante de détection est de charger et de décharger les batteries et de les détecter en même temps, maximisant ainsi l’efficacité et l’efficience du détecteur d’étanchéité à l’air. Le module est principalement composé d’une plaque tournante, d’un diviseur à came et d’un dispositif de détection, comme le montre la figure.
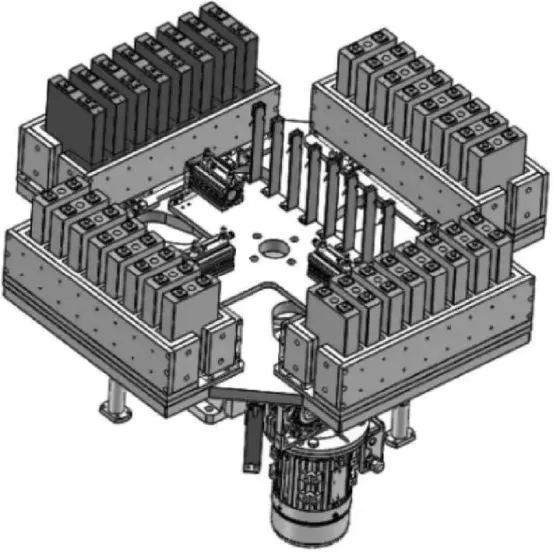
(2) Mécanisme de pompage à vide (comme indiqué ci-dessous). Les pièces d’évacuation et de remplissage d’hélium sont principalement composées de pompes à vide, d’électrovannes, de capteurs de pression et de canalisations. La pièce peut être évacuée et remplie d’hélium dans un délai défini.
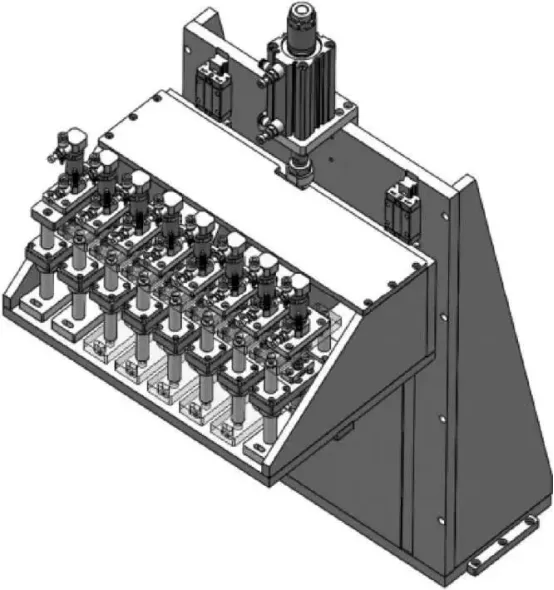
un. La pression de remplissage d’hélium (pression absolue) est de 0,05 ~ 0,15 MPa, ce qui est réglable dans cette plage.
b. Le système dispose d’une surveillance de la pression et de la concentration d’hélium et de fonctions de réapprovisionnement automatique en hélium. Lorsque le système détecte que la concentration ou la pression d’hélium est inférieure à la valeur définie, il ouvre automatiquement la vanne pour réapprovisionner en hélium de haute pureté.
c. Système de récupération : marque de pompe à vide, Leybold ; quantité, 1 pompe à vide, SV16B ; 1 pompe de récupération (pompe sèche), Leybold.
d. Mesureur de concentration d’hélium : La norme de concentration peut être définie.
e. Le taux de récupération du système de récupération est de >80%.
f. La fonction de nettoyage automatique de l’hélium est intacte et permet d’éliminer rapidement et efficacement l’hélium résiduel dans la boîte et les tuyaux. La précision et la répétabilité de la détection des fuites sont fiables. La partie B fournira des trous de fuite standard.
03 Sélection de l’équipement et cas d’application
Un client a les exigences suivantes en ce qui concerne la taille des cellules de batterie.
(1)Les clients fournissent des informations techniques. Le plan d’étage du modèle d’équipement est illustré dans la figure, ainsi que son nom de code et ses dimensions dans le tableau.
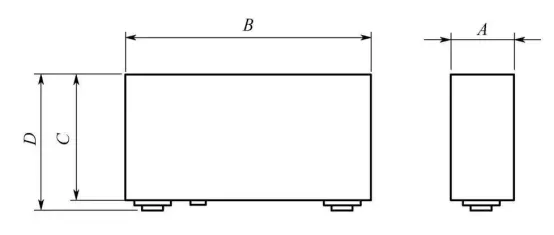

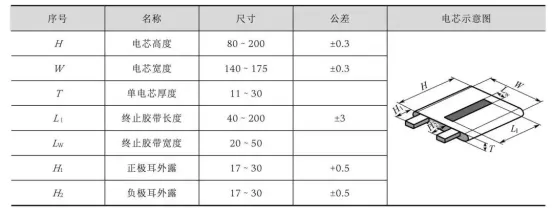
Selon les besoins du client, les spécifications de la cellule sont serrées en ajustant la main de serrage partagée. Si nécessaire, les tampons nécessaires peuvent être remplacés pour réaliser la production de cellules de différentes spécifications (telles que des gabarits, des montages, des plateaux). Spécifications de la taille des cellules La plage de variation ne doit pas dépasser la plage de taille maximale de l’appareil.
Cette ligne de production automatique est utilisée pour réaliser l’assemblage automatique de cellules de batterie d’alimentation lithium-ion à coque en aluminium prismatique après enroulement. La ligne de production se compose principalement des pièces suivantes : presse à chaud, machine de soudage par ultrasons, machine de soudage laser de plaque d’adaptation et machine d’emballage. , machine à décortiquer, machine de soudage par points par points, machine de soudage laser à capot supérieur et lignes de transmission logistique entre divers équipements, etc.