角型電池とは、アルミケーシングの電池を指します。彼らはレーザーシーリング技術を使用しており、完全に密閉されたアルミニウムケーシング技術はすでに高度に成熟しています。ガスの生成や膨張などの材料技術指標の要件が低いため、中国で早くから普及したパワーバッテリーの形態となっています。他の 2 つの形式のリチウム電池(円筒形とポーチ) と比較して、角型電池には、市場での使用において次のような顕著な利点があります。
(1)実装信頼性が高い。
(2)システム統合の効率が高い。
(3)比較的軽量でエネルギー密度が高い。
(4)シンプルな構造と便利なスケーラビリティにより、大容量の個々のセルの主要な選択肢となっています。
(5)個々のセル容量が高く、システム構造がシンプルで、バッテリー管理が簡単です。
01主な機能と設備の説明
アルミケーシングリチウム電池組立ラインは、パワーバッテリーの中期組立に使用され、パワーバッテリーの製造プロセスの重要な部分です。これは、バッテリーの性能と精度に大きな影響を与えます。その結果、この組立ラインの自動化レベルと運用精度は、ますます市場の注目を集めています。このセクションでは、認知され受け入れられている、高度に成熟した市場で実績のあるバッテリー組立ラインを紹介します。組立ラインには、次の特性があります。
1.強力な互換性:お客様の要件に応じて、さまざまなシリーズの製品と互換性を持つことができます。
2.モジュラー設計:短い切り替え時間、より少ない部品、および低コスト。
3.高い組み立て精度:視覚的および機械的な方法を使用したデュアルポジショニングにより、位置決め精度を向上させます。
4.さまざまなセルタイプと顧客固有のプロセスルートのカスタマイズにより、完全に自動化された組立ラインを実現します。
5.合理的な機器レイアウト:省スペース、完全自動化ライン、および低人件費。
6.高い製造品質保証:完全なパラメータテストと監視。
7.バッテリーの安全性と一貫性の製造保証。
この自動化された生産ラインは、巻線後の角型アルミニウムケースのリチウムイオンパワーバッテリーセルの自動組み立てに使用されます。生産ラインは主に次の主要コンポーネントで構成されています:ホットプレス試験機、X線装置、ペアリング機、超音波溶接機、タブ溶接機、コアアライメントマシン、フィルム/ヒートシール/接着機、ケーシング用プレスポット溶接機、レーザー蓋溶接機、ヘリウム漏れ試験機。バッテリーセルの熱プレス、X線検査、電極タブの予備溶接とペアリング、タブコネクタの溶接、裏面接着塗布、カバープレートのレーザー溶接、接着剤塗布、タブ折り畳みとコアアライメント、カプセル化、ケーシング、蓋シーリング溶接などの機能を実現し、プロセス全体での完全な自動化を可能にします。
1.2組立ラインの今後の開発動向
アルミシェル(角柱)電池の生産ラインは長い間使用されており、対応する技術は非常に成熟しており、既存の組立ラインも似ています。将来の開発動向は、材料の改良を続け、高性能セル材料を見つけることに加えて、バッテリー組立生産ラインの高効率と低コストが、パワーリチウム電池の将来の開発の方向性です。既存の市場開発の概要まとめると、次の点に注目してください。
(1)バッテリー本体の性能(バッテリーサイズ、エネルギー密度、マルチタブ構造など)
(2)組立生産効率、設備コストが大きく変わらないようにしながら、生産効率を継続的に改善します。
(3)バッテリー組立ラインの自動化は改善を続けており、生産歩留まりの管理が容易です。各プロセスの製造時間は合理的に制御されているため、リチウム電池の生産時間を効果的に短縮し、労働者の労働集約度が高く、生産コストが高いという問題を大幅に改善します。
(4)互換性が高く、幅広い製品に適しています。
(5)モジュラーテクノロジーは、効率を向上させるための重要な方法です。
1.3 アルミシェルの設計(プリズム)リチウム電池の製造および組立ライン
アルミケース(角柱)リチウム電池製造組立ラインを設計する際には、顧客の要件に基づいてさまざまな設計が考慮されます。生産プロセスで遭遇する問題とそれに対応する慣行を考慮に入れると、主に次の側面が考慮されます。
1.製品プロセス:これには、バッテリーのサイズ、タブサイズ、溶接厚さなどが含まれます。
2.工場スペース:生産ライン設備の特定の位置の適切な配置、メカニズムの最適化、人間工学の考慮、手動操作の容易さ、および保守性。
3.機器の設計:構造がシンプルなほど、操作が簡単になります。
4.生産ラインのリズムの割り当て:ボトルネックワークステーションの効率に重点が置かれています。効率が満たされない場合は、シングルワークステーションをデュアルワークステーションまたはマルチワークステーションに変更できます。高い安全性能と初回通過率も重要な考慮事項です。
5.製品の位置決め方法:側面の位置決め、両側のベースラインの位置決め、固定具の位置決めなど、さまざまな顧客の要件に対して、さまざまな製品の位置決め方法が使用されます。
6.防塵装置:円筒形の電池組立ラインでは、集塵機やブラシなどの除塵が必要な各装置には、対応する設備が装備されています。
7.機器内の物流設計:これには、内部機器の搬送と機器間の搬送が含まれます。
8.品質検査:組立ライン全体には、CCD検査、セル厚さ測定、絶縁検査、短絡検出などが含まれます。
9.生産ラインの外観の一貫性:機器の全セットの美的外観を維持します。
02設備構成と主要構成
アルミシェルリチウム電池組立ラインの全体的なレイアウトは次のとおりです。
(1)全線の寸法:長さ×幅×高さ= 3700mm×7000mm×2400mm(高さには警報灯は含まれていません)、操作面の高さ900mm、機器の間隔800~1000mm。
(2)外観:ストレスベアリングシャーシは角管溶接構造を採用し、上部シーリングフレームはアルミニウム合金プロファイル構造を採用し、プレキシガラスでシールされています。機器カバー全体は板金で覆われています。
(3)操作インターフェース:各デバイスには独立して操作されるタッチスクリーンが装備されており、すべてのデバイスのタッチスクリーンが埋め込まれています。
(4)全ラインレイアウト:鉛シェルバッテリー組立ラインのレイアウトを図に示します。
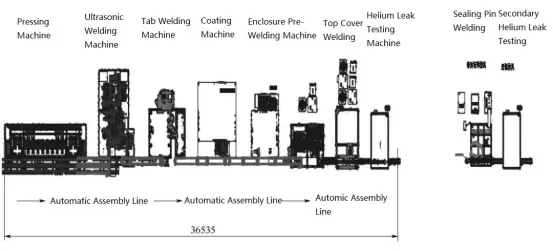
この生産ラインは、巻線機からヘリウムリーク試験機まで、アルミケース電池の全生産工程を含む全自動組立ラインです。このプロセスには、ホットプレスコンベアラインへの巻き取り(巻線機に6セットのマテリアルハンドリングロボットを使用)、→ホットプレス機→超音波溶接機→タブレーザー溶接機、セル包装機→→エンクロージャー、プレスポット溶接機→蓋レーザー溶接機→気密性試験機が含まれます。
2.1ホットプレス機
ホットプレス機は、巻線型バッテリーセルの熱圧縮成形に使用されます。その主な機能には、セルバーコードスキャン、A / Bセルの自動ロード、ホットプレス、ハイポットテスト、および不良品の拒否が含まれます。ホットプレスの温度、圧力、時間、ハイポットテストパラメータ、および結果は、対応するバーコードに関連付けられ、MESシステムにアップロードされます。この装置は、主にセルのロード/アンロード、検出、およびホットプレス用のモジュールで構成されています。この装置は、アルミニウムケースのバッテリーセルを組み立てる最初のプロセスであり、ホットプレスされたセルの品質は、その後の加工製品の品質に直接影響します。したがって、この組立装置の効率、作業精度、および自動化のレベルは重要な考慮事項です。機器のレイアウトとワークフローは図の通りです。
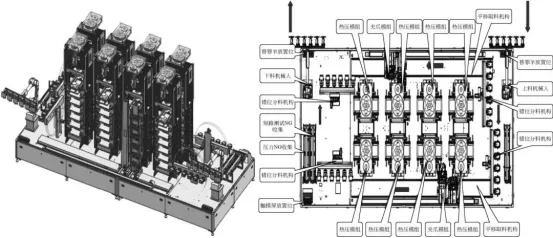
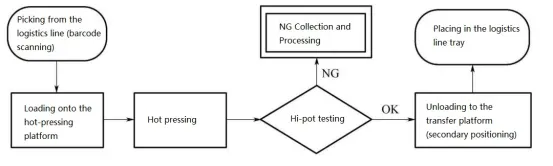
この図から、ホットプレス機での巻線型バッテリーセルの動作プロセスが明らかです。作業プロセス中、機器は巻線型バッテリーセルのホットプレスとその後のテストを実行します。ホットプレスの温度、圧力、時間、Hi-potなどのテスト結果は、リアルタイムの監視とフィードバックのためにMESシステムにアップロードされます。不良品は、処理品質を確保するために拒否されます。
機器のレイアウト図から、ローディングおよびアンロードロボットアーム、トランスファーコンベヤー、トランスファーロボット、ミスアライメント分離メカニズム、ホットプレスモジュールなどの主要コンポーネントが、半製品の組み立てに重要な役割を果たしていることがわかります。これらのコンポーネントの一部について詳しく説明しましょう。
(1)転位分布メカニズム。図は、ずれた材料分布メカニズムを示しています。フリップポジショニングモジュールの機能は、フリップメカニズムがベルトサーボドライブを使用して、クランプの反転と接続プレートの同期フリップを実現することです。クランプは常に水平に保たれ、フリップは滑らかで信頼性があります。位置決め治具は、クランプジョーシリンダーとダブルリンクシリンダーを使用してクランプと位置決めを行います。バッテリーコアとの接触面にはPOM素材を使用しています。
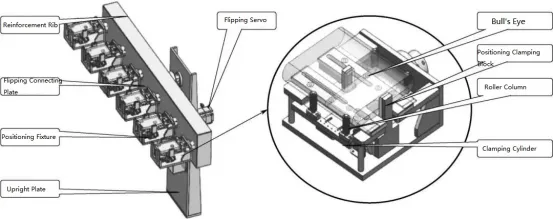
(2)モジュールを上下に動かします。ローディングおよびアンロードモジュールを図に示します。その主なアクションは、同期ベルトサーボモジュールとデュアルベルトドライブを使用した翻訳で、ロードおよびアンローディングモジュールの動きの滑らかさを向上させます。ローディングおよびアンローディングモジュールは、入出庫材料用のベルトサーボと、独立したサーボ制御を使用します。クランプジョーは、スクリューシリンダーを使用して昇降します。ピッチ変更機構は、サーボ駆動のリンケージ機構を使用し、ミドルリンクを位置決め基準として同期ピッチ変更を実現します。サーボは、クランプジョーの等距離サイズを制御して、ホットプレスのさまざまな作業条件を実現できます。位置変換モジュールは、材料のロードとアンロードを同期します。
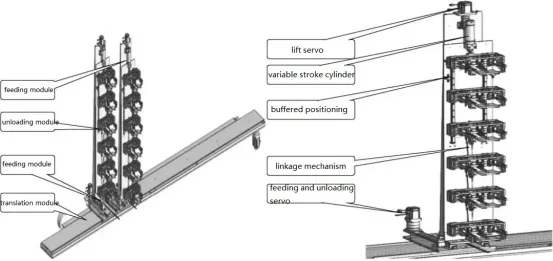
(3)ホットプレス部品。ホットプレス装置のホットプレスコンポーネントを図に示し、その詳細な説明は次のとおりです。
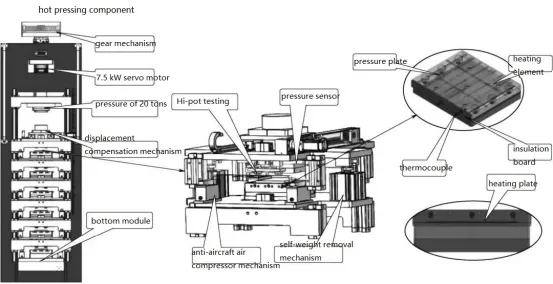
主要部品:昇圧シリンダー(圧力20t、6層)、加熱管、温度調節器、圧力センサーなど
操作手順:バッテリーセルでホットプレスとハイポットテストを実行します。
2.2超音波溶接機
超音波溶接機は、主にセルスキャン、ロボットアームによる自動セルペアリング、セルキャリブレーションと極性検出、アダプタープレート極性検出とキャリブレーション、アダプタープレート溶接治具、セル溶接治具、保護カバーの配置、超音波溶接とダスト抽出、溶接マーク成形、接着剤塗布と接着剤検査、自動アンロードなどのプロセスを通じて、バッテリーセルの超音波溶接を完了します。この装置は、セルスキャン、超音波溶接、接着剤塗布、およびセルペアリングからカプセル化までの情報バインディングを実現します。主に、到着時のセルスキャン、セルキャリブレーションと供給、アダプタープレートのキャリブレーションと供給、接着剤検査、MESシステムへの情報バインディングアップロードなどの機能が含まれています。
グリップ機構には、バッテリーセルの極性タブを識別するためのカラーセンサーが装備されており、タブが誤ってペアリングされていないことを確認します。バッテリーセルは、入ってくるコンベアベルトからロボットアームによってつかまれます。二次位置決めを行った後、トレイに配置され、A/Bセル極性タブで≤±0.2mmのミスアライメント誤差を確保します。バッテリーセルは、中央揃えでトレイに配置されます。細胞を配置する前に、トレイの周りの弾性クリップを開き、次にロボットアームが細胞をトレイに配置し、その後クリップが閉じて細胞をトレイの中央に配置します。
機器の構成と主要な構造
セルローディングモジュール、セル超音波溶接サイクルラインおよびフィクスチャモジュール、アダプターシート、保護シートローディングモジュール、保護シートカバーローディングおよびアンローディングモジュール、超音波正極および負極溶接モジュール、はんだスタンピング平坦化モジュール、バッテリーコア貼り付けモジュール保護接着剤モジュール、バッテリーセル保護接着剤モジュール、バッテリーセルアンローディングモジュール、および接着剤検出は比較的重要であり、組み立てられた全体で重要な役割を果たします半製品。これらのメカニズムのいくつかは、詳細な導入のために選択されています。
(1)バッテリーコアローディングモジュール(写真のように)。バッテリーセルの自動ロード、入荷材料の除塵、流入材料のアンチフール防止、入荷材料のバッファリング、不足警報機能の機能があります。また、コードをスキャンしてバッテリーセルを結合する機能もあります。
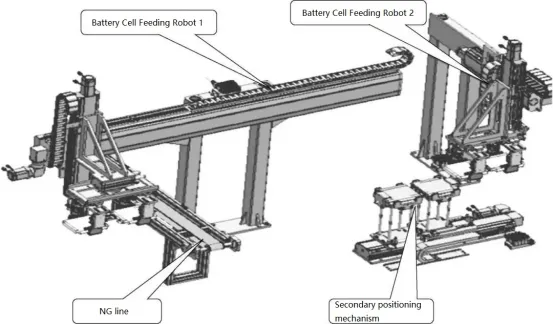
ある。主要部品:並進機構+昇降機構、バッテリーセルグリッパーなど
b.操作手順:バッテリーセルの供給および取り扱いプロセスは、ベルトモジュールを使用します。供給ロボット1は、顧客の物流ライン上のパレットから一群の電池セルを掴み、それらを二次位置決め機構に載せる。バッテリセルを二次的に位置決めした後、ハンドリングロボット2がセルをつかんでサイクルライン上に置く。給電プロセス中に、一対のバッテリセルが単一のNG(不良)セルを持っていることが検出された場合、ハンドリングロボット1はNGセルをNGラインに戻します。一方、OK(良好)セルはペアリングメカニズムに配置されてさらにマッチングされます。
(2)バッテリーセル超音波溶接サイクルラインとフィクスチャモジュール。
ある。主なコンポーネント:サイクルライン、モジュール、長短エッジ位置決めブロック、シリンダー、ガイドレールなど
b.操作手順(特定の操作手順を省略した機能説明):ハンドリングロボット2は、バッテリーセルをサイクルラインフィクスチャに供給し、セルをクランプします。変換メカニズムにより、フィクスチャが次のワークステーションに移動します。
超音波溶接サイクルラインの概略図を図に示します。
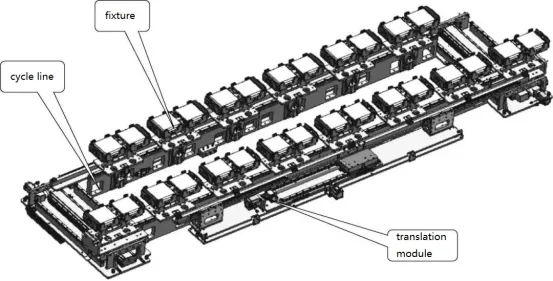
(3)アダプタープレートと保護フィルムを装填するためのモジュール(図を参照)。
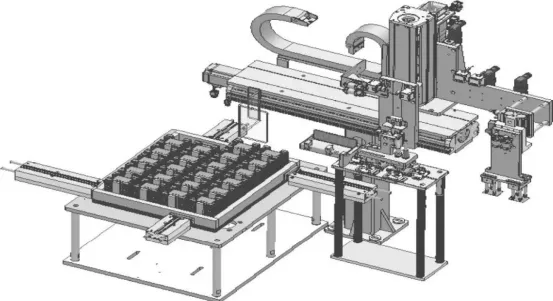
ある。銅-アルミアダプタプレートの装填には、人為的ミスを避けるための極性検出など、置き忘れや逆挿入を防ぐための対策が含まれています。
b.コネクタプレートの装填には、不適切な吸引や複数のプレートのピックアップを防ぐためのブラシが装備されています。また、複数のプレートの適切な分離と検出を確保するためのエアブローや真空振とうなどの機能も含まれています。不合格となった複数のプレートを保管するための廃棄物処理機構があります。
保護フィルムトレイの準備には、クリップホルダーへの手動ロードが含まれます。吸引ノズルは毎回保護フィルムのセットをピックアップし、供給端の供給を枯渇させます。ターンテーブル(または移動モジュール)は次の位置に回転し、保護フィルムの供給が途切れないようにします。
主要コンポーネントには、サーボモーター、リードスクリュー、シリンダー、およびサクションカップが含まれます。
e.アダプタープレートトレイの準備には、吸引ノズルが毎回アダプタープレートのセットをピックアップし、供給端での供給を枯渇させることが含まれます。トレイは次の位置に回転し、アダプタープレートの供給が途切れないようにします。
f.1回のローディングで40分間生産を維持できます。
(4)保護フィルムカバーのロードおよびアンロード用のモジュール(図に示すように)。
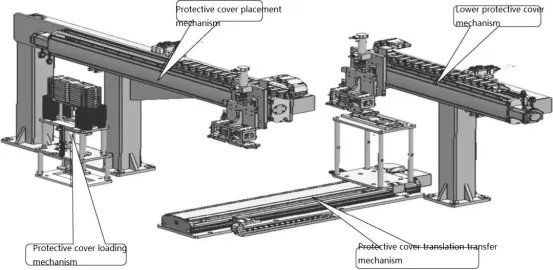
ある。主要部品:サーボモーター、リードスクリュー、シリンダー、ガイドレールなど
b.操作手順:初期状態では、保護カバーは手動で上部保護カバー準備機構に配置されます。上部保護カバー配置機構は、保護カバーのセットをつかんで上部保護カバーワークステーションに移動し、すべての保護カバープレートが組立ライン上で連続ループになるようにします。下部保護カバーを取り外すと、下部保護カバー機構が組立ライン2の固定具からカバーを取り出します。プラットフォームは保護カバーを保護カバートランスファーメカニズムに移動し、保護カバートランスファーメカニズムは上部保護カバーの位置に移動します。上部保護カバー配置機構は、保護カバーを取り出し、組立ライン1の対応する固定具に配置します。
c. 1回のローディングで40分間生産を維持できます。
(5)超音波正極および負極溶接モジュール(図に示すように)。

ある。主要コンポーネント:プラットフォーム、超音波溶接機、シリンダーなど
b.操作プロセス:固定具の位置決め後、Z軸リフティングシリンダーが上昇し、超音波溶接ヘッドが下降して溶接プロセスが完了します。X軸とY軸の平行移動は、サーボモーターを使用して調整され、溶接機の位置を調整し、工具交換を容易にします。X軸とY軸の移動量は、ツーリング変更の寸法要件への準拠を保証します。
(6)溶接印象平坦化モジュール(図に示すように)。このモジュールは、保護フィルムが平らに保たれ、端子タブが曲がっていないことを確認します。圧力ブロックは、ポリエーテルエーテルケトン(PEEK)と呼ばれる耐摩耗性材料でできています。
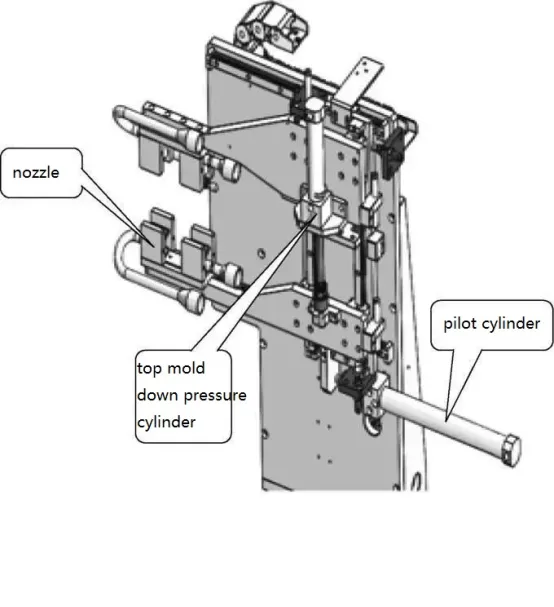
ある。主要部品:スライドレール、シリンダーなど
b.アクションプロセス:循環ライン本体のクランプが所定の位置に配置された後、回避シリンダーが上部と下部の金型を駆動して前方に伸び、次に下部金型が押し上げられ、上部金型が押し下げられ、溶接マークが水平になります。続いて、上型が上向きに移動し、下型が下向きに移動し、回避シリンダーが上型と下型を駆動して位置回避クランプを後退させます。
2.3アダプタープレートレーザー溶接機
1)装置構成
アダプタープレートレーザー溶接機装置の主な機能には、図に示すように、トップカバーとバッテリーセルの自動ロード、レーザー溶接による接続ピースとトップカバーの1つのボディへの溶接、ダスト除去後の自動アンロード、接着剤塗布が含まれます。
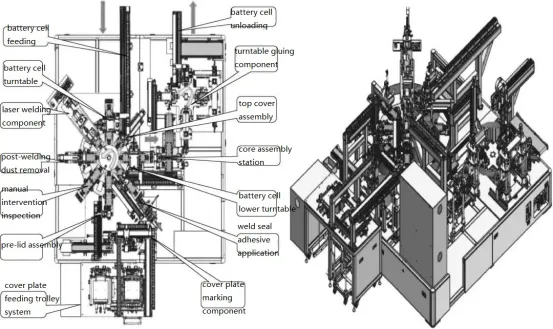
機器の寸法:長さ×幅×高さ= 2800mm × 3800mm×2300mm。
外観:耐荷重シャーシは正方形のチューブ溶接構造を採用し、上部シーリングフレームは有機ガラスでシールされたアルミニウム合金プロファイル構造を採用しています。
操作インターフェース:機器には操作用の独立したタッチスクリーンが装備されており、機器のすべてのタッチスクリーンが埋め込まれています。
2)キー構造
上の図から、カバープレートの供給メカニズム、トップカバーアセンブリ、レーザー溶接モジュール、溶接後の除塵メカニズム、および溶接シール接着剤塗布コンポーネントが重要であり、半製品の組み立てに重要な役割を果たしていることがわかります。これらのメカニズムの一部について、詳細な紹介と説明を提供します。
(1)カバープレート送り機構
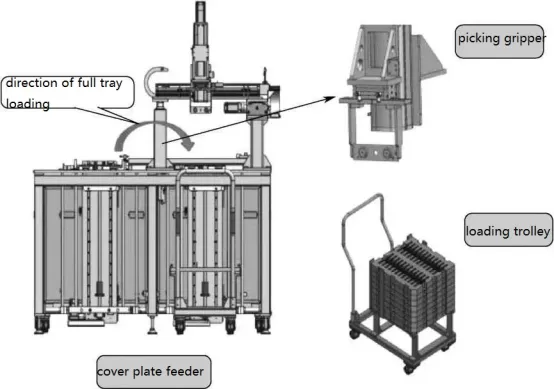
機能:カバープレートの供給メカニズムは、カバープレートの供給を実現し、トレイの位置決めや移動などの機能を備えています。
b.主要部品:リフティング機構、トレイ位置決め機構、小型カートなど
要件:30分間の機器の連続生産に対応するための1回限りのローディング。使用中のローディングカート1台とスペアローディングカート1台、アンローディングカート3台。トレイの二次位置決め精度は≤0.1mm。
(2)トップカバー組立
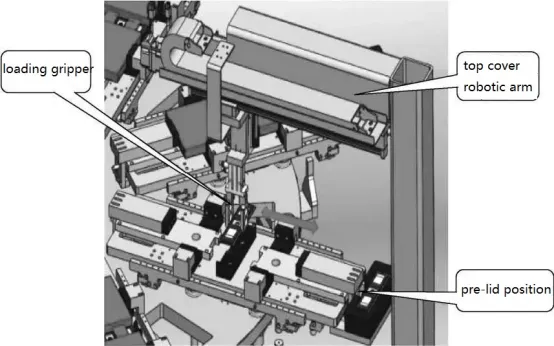
機能:コード化されたカバープレートをつかんでターンテーブルに置きます。
b.主要コンポーネント:並進同期ベルトモジュール、リフティングスクリューモジュール、グリップクローなど
要件:材料の落下や損傷のない信頼性の高いグラブ、メカニズム操作の繰り返し精度≤±0.05mm、ロボットアームの柔軟な設計、製品と接触するロボットアームの非接触部品は、非汚染材料を使用する必要があります。
(3)レーザー溶接モジュール(図に示すように)。
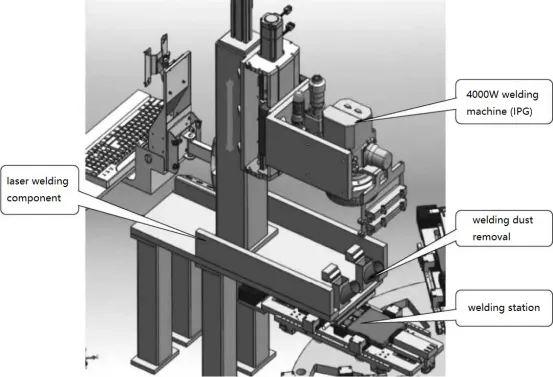
機能:レーザー溶接機を使用してカバープレートとタブを溶接します。
b.主要コンポーネント:溶接プラットフォーム、セルキャリアなど
(4)溶接後の除塵機構(図21):リフティングシリンダーが下降し、溶接領域を覆い、集塵のための密閉空間を作り出します。吸引気流速度は≥12m / sで、速度は最大範囲内で無段階に調整可能です。
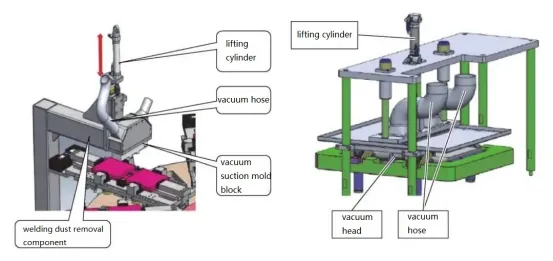
ある。主要部品:リフティングシリンダー、ロータリーモーター、サクションポートなど
b.操作プロセス:フィクスチャは除塵ステーションに移動します。シリンダーが下降し、モーターが回転して除塵を行います。
(5)ウェルドシール接着剤塗布部品(図参照)。
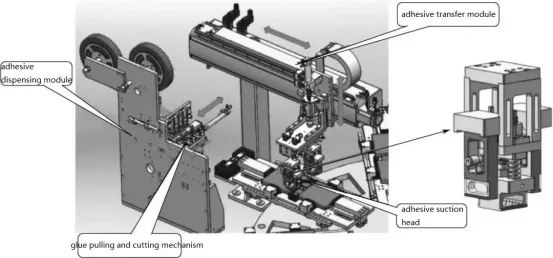
機能:タブ溶接領域の上部に保護接着剤を塗布します。
b.主なコンポーネント:接着剤引っ張り機構、接着剤切断機構、接着剤塗布機構、接着剤ローラーアセンブリなど。
要件:調整可能なテープの長さと接着剤の配置。バックアップテープの欠陥に対する真空検出と警告。テープの存在検出機能。接着剤塗布前の溶接領域の成形装置。接着剤塗布の歩留まりは≥99.8%です。
2.4 フィルムラッピングマシン
1.機器の主な機能:
フィルム包装機は、主にバッテリーセルの自動成形、セパレーターとボトムトレイの自動供給、セルをセパレーターで包む、側面と底面に接着剤を塗布する、CCDテストなどに使用されます。機器のレイアウトを図に示します。
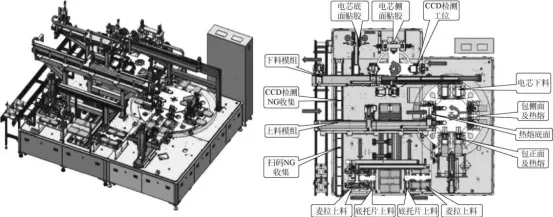
機器の基本仕様は次のとおりです。
·装置の外形寸法:3100mm×4000mm×2300mm。
·機器の歩留まり:≥99.8%(入荷不良材料を除く)。
·機器の稼働時間:≥98%(機器関連の問題による故障のみを参照)。
2)キー構造
フィルム包装機のレイアウト図から、底面接着剤塗布機構、セパレーターおよび底部トレイ供給レイアウト機構、前面包装フィルム機構、底面接着剤塗布機構、および側面接着剤塗布ターンテーブル機構が非常に重要であり、半製品の組み立てにおいて重要な役割を果たしていることがわかります。これらのメカニズムのいくつかについて詳しく説明しましょう。
(1)セパレーターとボトムトレイの供給のレイアウト(図に示すように)。
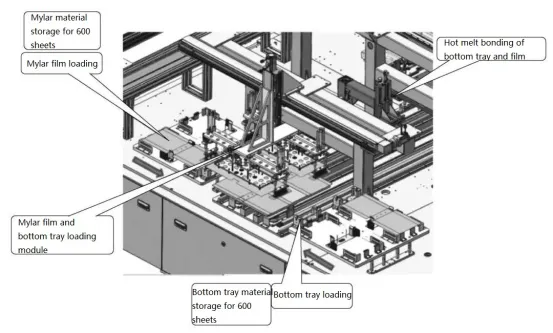
ある。主要コンポーネント:手動マイラー供給アセンブリ(1セット)、マイラー供給ロボットアーム(1セット)、ボトムトレイ材料ボックス(1セット)、ボトムトレイ供給ロボットアーム(1セット)、マイラーボトムトレイホットメルトプラットフォーム(1セット)、ホットメルトメカニズム(1セット)。
b.操作プロセス: ロボットアームは、ホットメルトフィクスチャにボトムトレイを置きます → マイラー供給ロボットアームは、ホットメルトフィクスチャにフィルムを置きます → ホットメルトフィクスチャはホットメルト→ステーションに移動します ホットメルトプロセス → ターンテーブルフィルムの供給と荷降ろしは、回収位置で待機します。
(2)フロントラッピングフィルムステーション(図に示すように)。フィルムラッピングとホットメルトターンテーブルのレイアウトを図に示します。
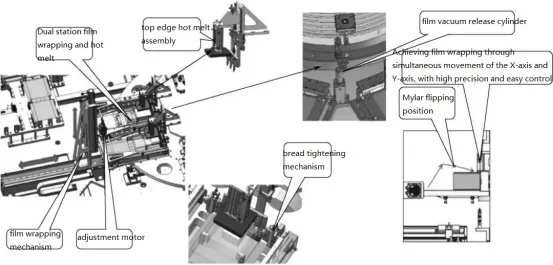
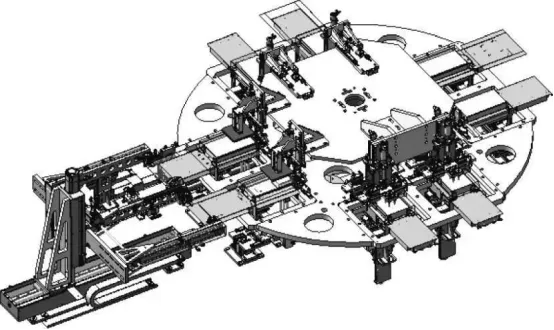
ある。主要部品:ワークステーション用治具(8セット)、ホットメルト組立(1セット)、フィルムラッピング組立(1セット)、折り畳みフィルム機構(1セット)、固定具開封機構(3セット)
b.操作プロセス: フィルムローディング→セルローディング→底面ホットメルト→ フロントフィルムラッピング → フロント面ホットメルト → サイドフィルムフォールディング → サイド面ホットメルト→アンロード。
(3)底面接着剤塗布メカニズム(図に示すように)。
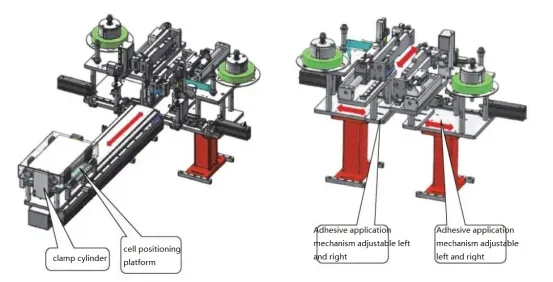
ある。底の両側にL字型の粘着テープがあります。テープの長さと位置は、対称的な接着位置と±0.5mmの偏差で調整できます。接着プロセスにより、バッテリーセルに圧力や傷が付かないようにする必要があります。
b.接着剤のバックアップ不良を検出でき、警告機能を備えています。接着剤を塗布した後、カラーマークセンサーを使用して接着剤の有無を検査します。
c.手動の接着剤バックアップは手作業で行われます。
機能:バッテリーセルを包んだ後、接着剤を塗布して下部トレイに「L」字型に固定します。
e.主要部品:グルーローラー、接着剤塗布、切断組立など
要件:接着剤の欠陥率≥99.6%。接着剤の塗布は、テープの破損のインスタンスなしで連続して行う必要があります。粘着テープは、しわや剥がれなしにバッテリーセルに貼り付ける必要があります。
(4)側面接着剤塗布ターンテーブル(図に示すように)。
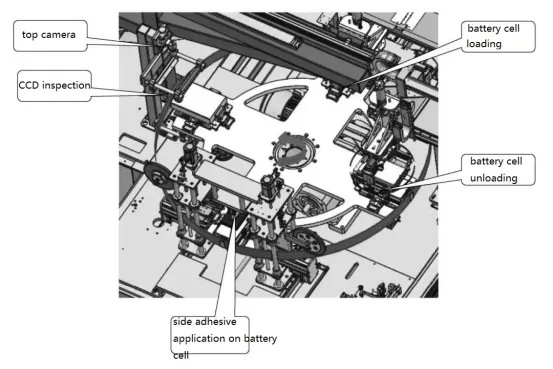
a.テープは片面に1枚ずつ貼られています。
b.テープの長さと位置は、対称的な接着位置と±0.5mmの偏差で調整できます。
接着プロセスは、バッテリーセルに圧力や引っかき傷を引き起こさないようにする必要があります。
d.不十分な接着剤のバックアップは検出でき、警告機能があります。
e.接着剤を塗布した後、カラーマークセンサーを使用して接着剤の有無を検査します。
f.手動の接着剤バックアップは手作業で行われます。
機能:バッテリーセルを包んだ後、バッテリーセルの両側に接着剤を塗布して「U」字型に固定します。
h.主要部品:グルーローラー、接着剤塗布および切断アセンブリ、X軸リードスクリューアセンブリなど
要件:接着剤の欠陥率≥99.6%。接着剤の塗布は、テープの破損のインスタンスがなく、連続している必要があります。粘着テープは、しわや剥がれなしにバッテリーセルに貼り付ける必要があります。
2.5シェルプレ溶接機
1)機器の主な機能
シェルプレ溶接機のレイアウトを図に示します。
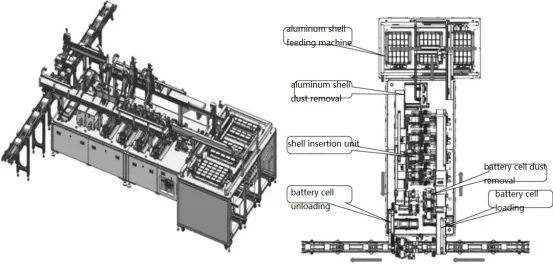
ケース挿入プレ溶接機装置は、角柱状のアルミニウムケースのバッテリーをケースに自動的に挿入するために使用されます。メイン機能
機器のnsには、アルミニウムケースのロード、自動バッテリーロードとコードスキャン、アルミニウムケースとバッテリーコアのほこり除去、バッテリーコアの挿入、バッテリーのアンロード、情報バインディングとアップロード(MES)などが含まれます。
機器の主な技術的パラメータ。
装置の全体寸法:2850mm×1900mm×2500mm。
設備の歩留まり率:≥99.8%(設備に起因する欠陥のみを指します)。
機器稼働率:≥99%(機器に起因する故障のみを指します)。
アルミニウムシェルの装填時間間隔:≥25分;除塵パラメータは自動的に記録され、除塵プロセス中にバッテリーコアとアルミニウムシェルが損傷することはありません。拭き取ることができる目に見える粒子はありません。
セルの厚さを制御するには、クランプ力を増やす必要があります:10~50kgf(1kgf = 9.81N)は調整可能で、デバッグ精度は±5kgfで、クランプ圧力と真空値はデジタルで調整可能です。
ケーシングプロセス中の推力制御精度:設定値の±5%。ケーシングとバッテリーセルは、ケーシングに挿入される前に2回配置され、シェルの開口部を拡張する機能を持っています。バッテリーコアは、バッテリーコアをケーシングにガイドするために、完全に周囲を囲むガイド機構を採用しています。アルミシェルのシェル口は一切触れることができません。
位置決め偏差:0.5mm。
メカニズム動作の再現性:偏差≤±0.05mm。
2)主要な構造
上に示したシェルプレ溶接機の機器レイアウト図から、アルミニウムシェル供給メカニズム、アルミニウムシェルとバッテリーセル、トップカバークリーニングメカニズム、バッテリーセル挿入メカニズム、バッテリーセル供給メカニズムなど、いくつかの主要な構造を特定できます。これらの構造は、最終製品の組み立てにおいて重要な役割を果たします。いくつかの選択されたメカニズムの詳細な説明を提供しましょう。
(1)アルミシェルフィーディングモジュール(図に示すように)
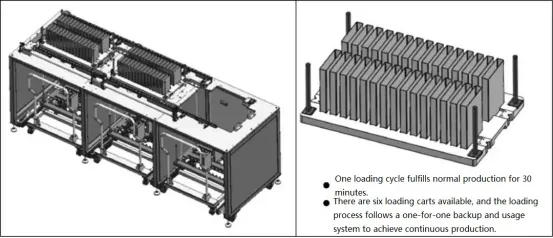
ある。機能:アルミシェルの供給を実現し、パレットの位置決めや移動などの機能を備えています。
b.主なコンポーネント:アルミシェルパレット自動ローディング装置、アルミシェルパレット、材料輸送トロリーなどのスタッキング。
要件:アルミニウムシェルの供給間隔は≥20分です。信頼性の高いガイド機構と位置決め機構を装備。
(2)バッテリーコアとケースのダスト除去機構(図参照)。
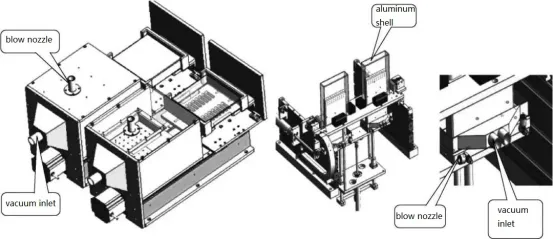
機能:ケーシングは垂直に清掃され、ブロープロセスは明らかな死角なしにすべての角度をカバーします。シェルの開口部は特に処理されます。
b.主な構成部品:除塵機構、シリンダー並進機構など
3.バッテリーセルの挿入メカニズム(図に示すように)。
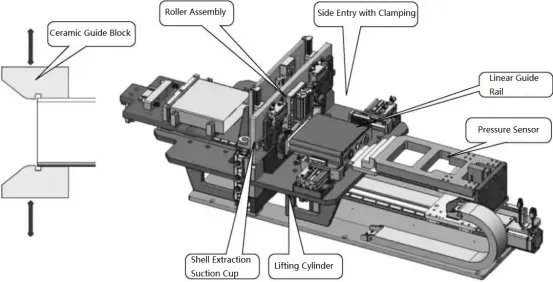
シェル挿入時には、アルミシェルを固定し、バッテリーセルをクランプして前方に押し出してセルタブを保護します。
b.シェル挿入プロセスでは、傾斜角度の大きいセラミックガイドブロックを使用して、アルミニウムシェルの削り取り、セパレーターの損傷や引っかき傷を防ぎます。
c. アルミシェルとの接触部にはセラミック材料を使用しています。
d.挿入後、後続のプレスステーションには4mmの隙間が保たれ、サポートブラケットがシェルに入り、シェルの挿入深さが一定になるようにする必要があります。
e.位置決め精度:吸盤シェル抽出構造により、シェルをしっかりと配置し、±0.1mmの位置決め精度を実現します。シェル挿入プロセス全体の圧力が監視され、センサーを分解せずにキャリブレーション用の標準ウェイトが提供されます。
f.クリーニング機構は、バッテリーセルとシェルカバーの溶接面を上側から吹き付け、下側から吸引することで洗浄します。
g.ノズルの吹き出し角度と高さは自由に調整でき、均一な空気の流れを確保し、効果的なエアカーテンを形成します。
h.カバープレス:主に挿入後のバッテリーセルのハイポットテストに使用されます。プレスする前に、カバープレートの周りのほこりを取り除き、カバープレートをシェルに押し込みます。
機能:バッテリーセルをシェルに挿入します。
j.主なコンポーネント:シェル挿入機構、リードスクリューアセンブリ、シェル抽出吸引機構など
4.バッテリーセルの供給メカニズム(図に示すように)。
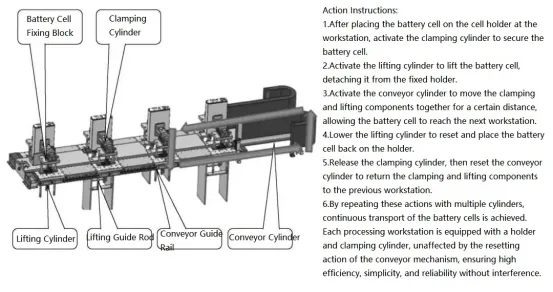
機能:シェルに挿入した後、バッテリーセルを搬送するために使用されます。
b.主要部品:バッテリーセルクランプ機構、リフティングシリンダー、コンベア機構など
2.6プレ溶接機
1.機器の主な機能
プレ溶接機のレイアウトを図に示します。
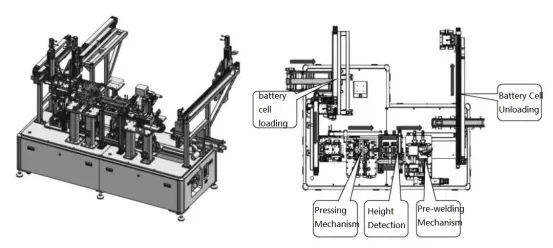
プレ溶接機装置のレイアウトは、プリズムアルミニウムシェルとカバープレートのプレ溶接に使用されます。装置の主な機能には、自動バッテリー供給とスキャン、プレス、高さ検出、レーザー溶接、バッテリーアンロード、およびMES(Manufacturing Execution System)への情報バインディング/アップロードが含まれます。
(1)機器の主な技術パラメータ:
全体寸法:3000mm×1800mm×2500mm。
機器の歩留まり:≥99.8%(機器の理由のみに起因する欠陥を参照)。
設備稼働率:≥99%(設備の故障のみによるもの)
ハイポットテスト:テスト時間は0.5秒から5秒の範囲で、1秒から100秒の範囲で調整可能です。使用した銘柄は±5%の精度を持つ日置電機です。正端子と負端子の間のテスト電圧(DC)は100Vで、範囲(DC)は0V〜500Vで、50V刻みです。
位置決め偏差:0.5mm。
メカニズム動作の再現性:偏差≤±0.05mm。
2)キー構造
プレ溶接機装置のレイアウト図から、バッテリーセルの成形およびプリプレス機構、ステップおよび短絡試験モジュール、プレス機構、プレ溶接機構、ならびにカバーシールおよびプレス機構が重要であり、半製品の組み立てにおいて重要な役割を果たすことがわかります。これらのメカニズムのいくつかについて詳しく説明しましょう。
(1)バッテリーセルの成形とプリプレス機構(図に示すように2セット)
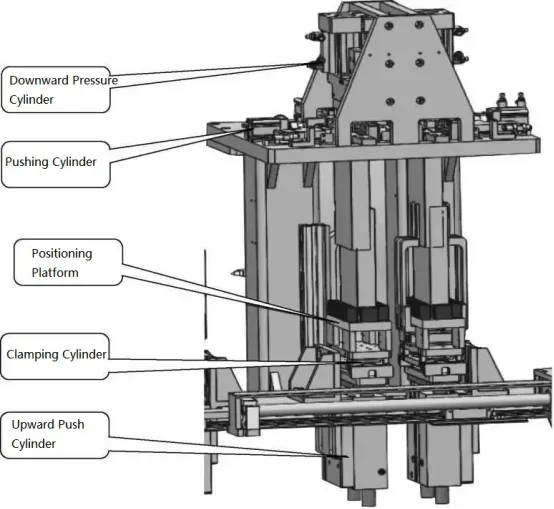
機能:バッテリーセルをケーシングに挿入した後、バッテリーセルの上部カバーを形作って押します。
b.主なコンポーネント:コンポーネントの位置決め、アセンブリの持ち上げとプリプレスなど。
要件:圧力の上限を事前設定し、限界を超えたときにアラームと停止機能を提供して、バッテリーセルとケーシングの損傷を防ぐことができる必要があります。圧力調整範囲は200〜1000Nである必要があります。プレス後、トップカバーに損傷や破片がないこと、ケーシングの開口部の周りにバリ、バリ、傷がないこと。プレスモジュールは、簡単で便利な切り替えのためにモジュール性で設計する必要があります。
(2)カバーシール・プレス機構(図参照)
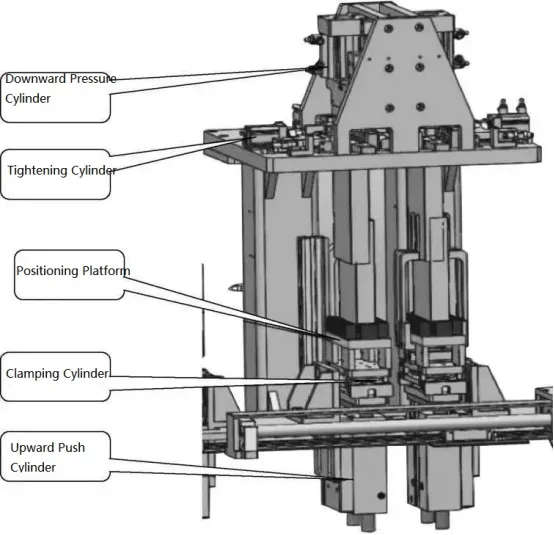
カバーのシーリングおよびプレス機構の具体的な操作順序は次のとおりです。
a. クランプシリンダーアクション:クランプ上向きのプッシュシリンダーがセルを組み立て位置まで持ち上げながら、バッテリーセルをクランプします。
b. センタリングシリンダーアクション:クランプ バッテリーセルを正しい位置に位置合わせし、クランプシリンダーを解放します。
c. シリンダー アクションの締め付け: シェルとカバー プレートをプレス金型内に固定し、ステップが 0.20mm以内であることを確認します。金型は正確な寸法と高い滑らかさを備えているため、内部のシェルとカバープレートをスムーズに動かすことができます。
吸盤アセンブリアクション:シェルを保持して外側に引っ張り、大幅な内側の変形を防ぎます。
下向き圧力シリンダーアクション:プレス金型に導かれて、カバープレートをシェルに押し込み、過度のプレスを防ぐための機械的なリミッターを組み込みます。
f.各シリンダーにはストローク長を調整でき、主要部品には油圧クッションと微調整リミッターが装備されています。
(3)プレ溶接機構(図参照)
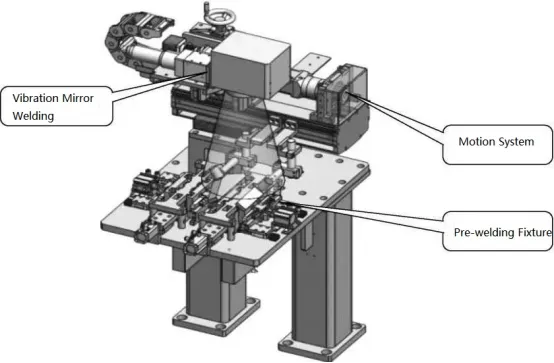
「プレ溶接機構」は、主にモーションシステムとプレ溶接治具で構成されています。
機能:レーザーフォーカシング、焦点ぼけ測定、溶接ガス保護、およびモーションシステムはレーザーヘッドをドラッグして溶接経路をスキャンします。
b.主なコンポーネント:モーションシステムのX軸とY軸は、サーボモーター、レーザー溶接機などを採用しています。歩数検出センサーは、2Dプロファイラー(表面形状測定機)を使用しており、歩数検出精度は±0.02mm、歩数は0.2mm未満です。
2.7 トップカバーレーザー溶接機
1)機器の主な機能
トップカバーレーザー溶接機のレイアウトを下図に示します。この装置は、主に予備溶接後のバッテリーセルの上部カバーのレーザー溶接とハイポットテストに使用されます。その主な機能には、セルのロードとアンロードのための自動バーコードスキャン、保護カバープレートの自動ハンドリング、クランプと位置決め、レーザーシーリング溶接、ハイポットテスト、NGバッファリング、およびプロセス輸送が含まれます。
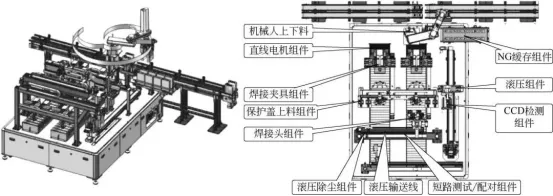
装置の全体寸法:3000mm×4500mm×2200mm。
設備の初回歩留まりは≥98.5%、2回目の優良率は≥99.5%(不良品の入荷を除く)、稼働率は≥98%です。
溶接速度≥150mm / s、CMK≥1.33。
レーザー溶接圧力強度>10kgf、CMK≥1.33。
レーザー溶接機の出力電力と固定具の圧力制御精度:設定値±5%、CMK≥1.33。
溶接品質(溶接位置決め精度±0.1mm、溶接幅偏差≤±0.1mm)、一貫性CMK≥1.33。
レーザー溶接プロセス中に製品と接触する保護キャビティの環境清浄度は、100,000レベルの要件よりも高くなっています。
機器機能は、組織化、通信、およびフロントとリアのプロセス機器のドッキングのニーズを満たすことができます。
2)キー構造
トップカバーレーザー溶接機のレイアウト図から、供給機構、位置決めアセンブリ、保護カバー供給部品、NGバッファリング、移動検査部品、CCD検査部品、NGハンドリング部品、荷降ろし部品、溶接ヘッド部品など、いくつかの重要なコンポーネントを特定できます。これらのコンポーネントは、半製品の組み立てにおいて重要な役割を果たします。いくつかの選択されたメカニズムを詳しく紹介しましょう。
(1)トップカバーレーザー溶接機の送り機構(図を参照)。
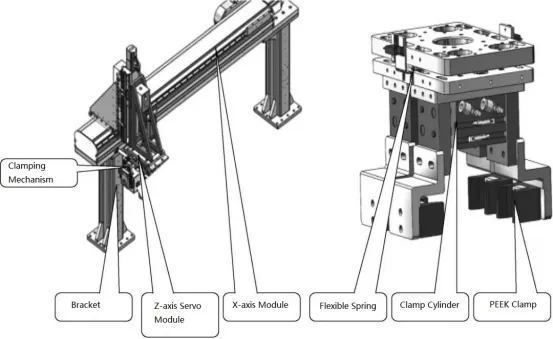
ある。ローディング機構には、ローディングブラケット、X軸モジュール、Z軸モジュール、クランプ機構などが含まれます。ローディングクランプを使用して、入荷する材料物流ラインのバッテリーコアをつかみます。一度に2つのバッテリーをつかみ、溶接固定具に置きます。溶接治具は4セットあります。バッテリーは一度に2個ずつ配置され、バッテリーは2回放電されます。
b. マニピュレーターのリフティングメカニズムは柔軟に保護されています。下降プロセス中に設定位置に到達する前に抵抗に遭遇すると、すぐに上昇し、音と視覚的なアラームを発します。
マニピュレーターには、電源とガスの保護機能があります。バッテリーがclの場合amp バッテリーを切断すると、バッテリーは少なくとも30分間落下しません。
d. バッテリーコアを配置してクランプし、溶接中にその位置が正確で信頼できるようにします。クランプブロックは、耐熱性材料で作られています。溶接位置決め精度は±0.1mm、溶接幅の偏差は≤±0.1mmです。
e.バッテリーコアの高さ方向は、トップカバーの上面を基準に配置しています。バッテリー コアを配置してクランプした後、バッテリー コアの上部カバーの上面の高さは、クランプ ブロックの上面を 1.5 ~ 2mm上回ります (お客様が決定)。上面レベル誤差は≤0.1mm、高さ方向の再現性誤差は≤0.05mmです。
f.バッテリーコアの位置決めおよびクランププロセス中、クランプブロックはバッテリーコアとの滑り摩擦を生じさせません。フォロワーデバイスは、バッテリーコアを挟んだり引っかいたりしないようにするために使用されます。バッテリーコアを配置してクランプした後、クランプブロックとバッテリーコアの間のギャップは≤0.05mm(標準ピース)です。
g.セルの位置決めとクランプシリンダーの圧力は調整可能で、空気圧値は<0.05MPa変動します。
(2)上部位置決めコンポーネント(写真に示すように)。
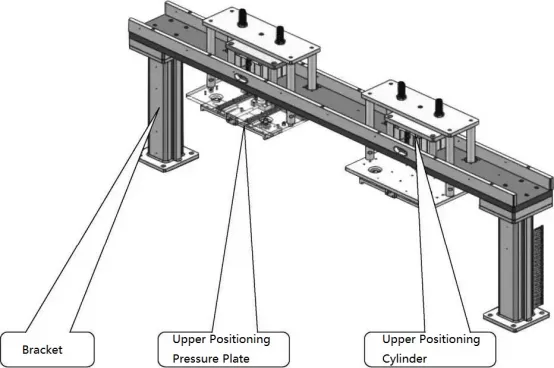
具体的なアクションプロセスは次のとおりです。
ある。バッテリークランプは、A / Bリニアモーターを介して上部位置決め位置に移動します。
b.バッテリークランプの長辺と短辺の位置決めシリンダーの電磁弁を制御して、中放電位置に切り替えます。
上部位置決め移動シリンダーは、上部位置決め圧力プレートを駆動して押し下げてバッテリーを配置します。
上部位置決めが完了すると、長辺と短辺のソレノイドバルブが常圧に切り替わり、上部位置決め移動シリンダーが上昇します。
(3)保護カバーローディングアセンブリ(写真を参照)。
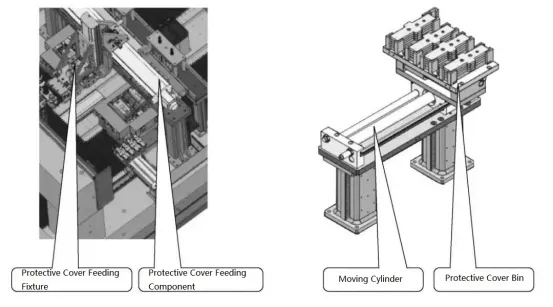
具体的なアクション手順は次のとおりです。
ある。上部の位置決めが完了すると、バッテリーは保護カバーの供給のために上部保護カバーの位置に移動します。
b.溶接が完了すると、システムはアンロード位置に移動して保護カバーを取り外し、バッテリーをアンロードします。
注意:保護カバーは、機械を停止せずに交換できます。保護カバーは電極カラムを保護するため、電極カラム、QRコード、防爆フィルム、注入穴の溶接スパッタによる汚染を防ぎます。
(4)CCD検査部品(図参照)。
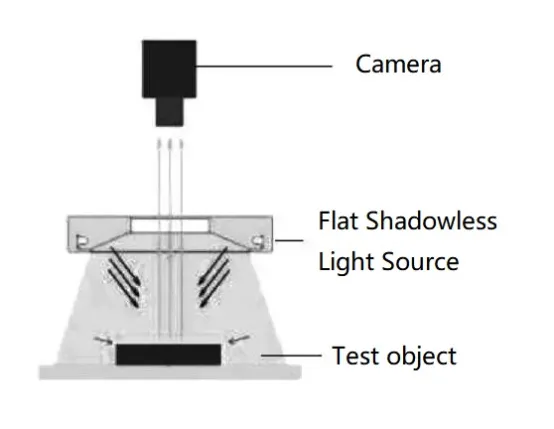
溶接後、バッテリーセルはロボットアームモジュールを使用して移動検査コンポーネントに運ばれます。移動検査部品には2セットのクランプが装備されており、供給位置、検査位置、荷降ろし位置の3つのステーションがあります。CCD検査部品には、溶接シームのピット、ブローホール、はんだ付けの不連続性、多孔性、不完全なはんだ付けなどの欠陥を検出するためのカメラが装備されています(図を参照)。
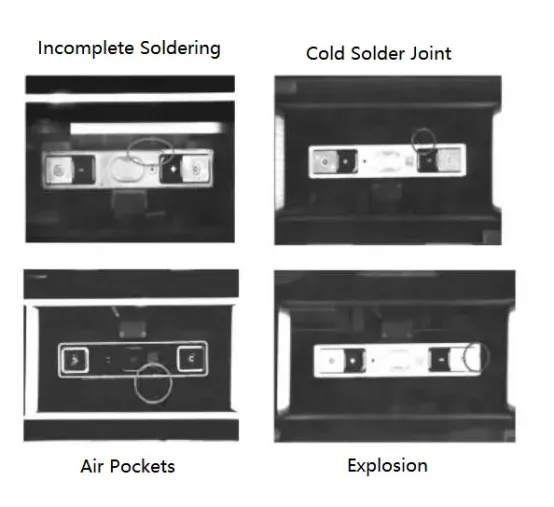
2.8正圧ヘリウムリークテスター
1.機器の主な機能
以下に示すレイアウト図は、正圧ヘリウムリークテスト装置を示しています。この装置は、主にトップカバーレーザー溶接後の角柱状アルミニウムシェルバッテリーセルのシール性能をテストするために使用されます。溶接後のトップカバーのシール状態を検出するために真空方式を採用しています。作業プロセスは次のとおりです:トップカバーがレーザー溶接された後、テストされたバッテリーセルは供給コンベヤーを介して機械に供給され、トップカバーのQRコードが読み取られます。次に、選別ロボットアームが、テストされたバッテリーセルをテストチャンバーに配置します。チャンバーは、設定された負圧値に達するまで排気され、その後、外部真空源が閉じられます。気密性試験機は、バッテリーセルの内部気密性をテストするために使用されます。このデバイスは、テストされたワークピースが適格であるかどうかを判断するのに役立ちます。
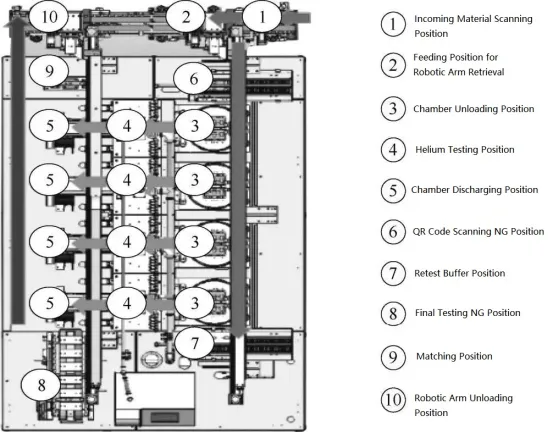
このシステムは、購入者の要件に厳密に従って設計および製造されており、モジュラー設計を使用し、購入者のリーク検出要件を十分に考慮し、標準化されたモジュールとコンポーネントを可能な限り使用して、システムの信頼性と保守性を確保し、メーカーの要件を満たしています。テクニカル指標を指定します。
機器の基本的な指標は次のとおりです。
設備歩留まり率:≥99.8%(不良品入荷を除く)
設備利用率:≥99%;誤検出率:≤0.3%。
ヘリウム検査基準:≤9.9×10-7Pa・m3/s。
2)キー構造
この装置は、ワークインレット/アウトレットマニピュレーター装置、ボックススライド、排気/ヘリウム充填装置、真空ボックスリーク検出装置、ヘリウム充填および除去装置、および電気制御装置で構成されています。図48の正圧ヘリウム検査装置のレイアウト図から、ワーク入口/出口マニピュレータ装置、排気/ヘリウム充填装置などが重要であり、組み立てられた半製品全体で重要な役割を果たしていることがわかります。これらのメカニズムのいくつかは、詳細のために選択されています。紹介。
(1)ターンテーブルを確認します。検出ターンテーブルの主な機能は、バッテリーのロードとアンロードを同時に検出し、気密性検出器の有効性と効率を最大化することです。モジュールは、図に示すように、主にターンテーブル、カムディバイダー、検出治具で構成されています。
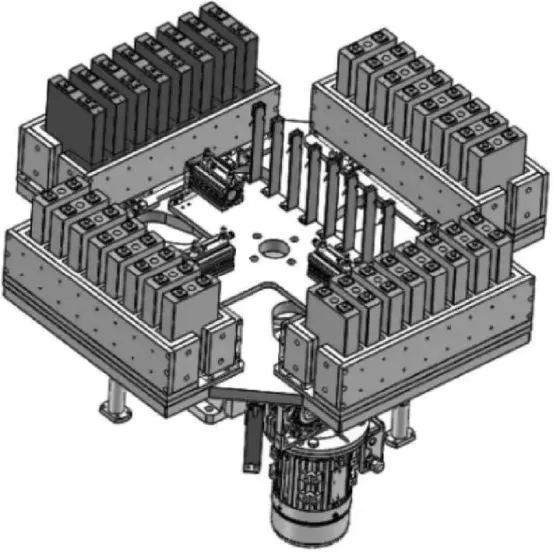
(2)真空排気機構(下図参照)排気およびヘリウム充填部品は、主に真空ポンプ、電磁弁、圧力センサー、パイプラインで構成されています。ワークピースは、設定された時間内に排気し、ヘリウムを充填することができます。
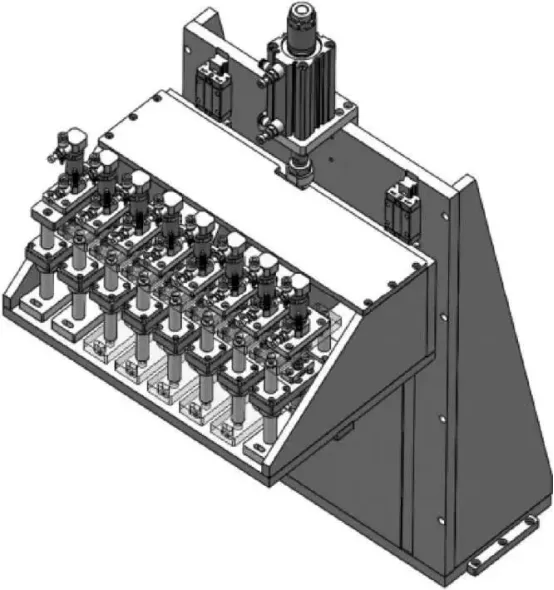
ある。ヘリウム充填圧力(絶対圧)は0.05~0.15MPaで、この範囲で調整可能です。
b.このシステムには、ヘリウム圧力と濃度の監視、およびヘリウム自動補充機能があります。ヘリウムの濃度や圧力が設定値より低いことを検知すると、自動的にバルブが開き、高純度のヘリウムが補充されます。
c.回収システム:真空ポンプブランド、ライボルト。数量、真空ポンプ1台、SV16B;回収ポンプ(ドライポンプ)1台、ライボルト。
ヘリウム濃度計:濃度基準を設定できます。
e.復旧システムの回収率は>80%です。
f.自動ヘリウム洗浄機能はそのままで、ボックスやパイプに残留するヘリウムを迅速かつ効果的に除去できます。リーク検出精度と再現性は信頼性があります。パーティーBは、標準のリークホールを提供します。
03装置選定・適用事例
お客様には、バッテリーセルサイズに関する次の要件があります。
(1)お客様から技術情報を提供します。機器モデルの間取り図を図に示し、そのコード名と寸法を表に示します。
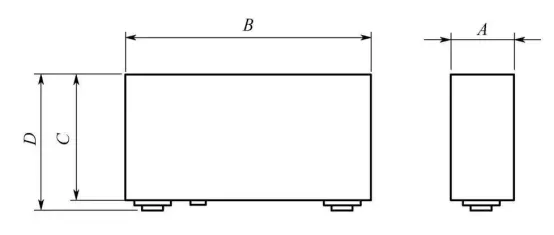

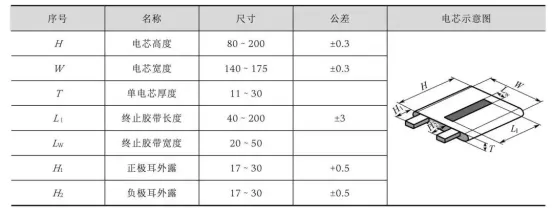
お客様のニーズに応じて、セルの仕様は共有のクランプハンドを調整することでクランプします。必要に応じて、必要なパッドを交換して、さまざまな仕様のセル(治具、固定具、トレイなど)の生産を実現できます。セルサイズの仕様変動範囲は、デバイスの最大サイズ範囲を超えてはなりません。
この自動生産ラインは、巻線後の角型アルミニウムシェルリチウムイオンパワーバッテリーセルの自動組み立てを実現するために使用されます。生産ラインは、主にホットプレス機、超音波溶接機、アダプタープレートレーザー溶接機、包装機で構成されています。、シェル機、プレスポット溶接機、トップカバーレーザー溶接機、各種機器間の物流伝送線など