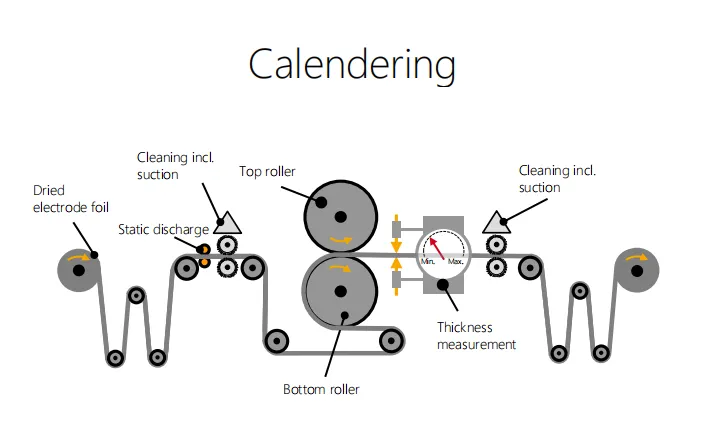
圧延の重要性は、電極シートを圧縮し、バッテリーのエネルギー密度を高めることです。電極シートを前のプロセスでコーティングして乾燥させた後、活物質と箔の間の剥離強度は非常に低いため、活物質と箔との接着強度を高めるために丸めて、電解液に浸るのを防ぎ、使用中に電極シートを巻く必要があります。適切な圧縮密度により、バッテリーの放電容量を増やし、内部抵抗を減らし、分極損失を減らし、バッテリーのサイクル寿命を延ばし、リチウムイオン電池の利用率を向上させることができます。電極シートの圧延は、一般に、2つの鋳鋼圧縮ローラー、モーター、およびトランスミッションシャフトで構成されるダブルローラープレスによって完了します。ローリングモードをオンにした後、モーターは上下のローラーを同時に回転させるために駆動し、巻線機構は電極シートを引っ張ってローリングギャップを着実に通過し、最終的に必要な圧縮密度に押し込まれます。
ローリングプロセスは、セルの性能に大きな影響を与えます。圧延プロセスでは、いくつかの典型的な問題が発生します:(1)電極シートの厚さが一貫していない。厚さが一定でないということは、活物質の密度が一定でなく、電極シート内のリチウムイオンと電子の透過率と伝導率が異なることを意味します。電流密度が異なると、リチウム樹状突起の沈殿が非常に容易になり、バッテリーセルの性能に悪影響を及ぼします。また、電極シートの厚みが異なると、活物質と集電体との接触抵抗も異なります。電極シートが厚いほど、内部抵抗が大きくなり、バッテリーの分極が深刻になり、バッテリーの容量に影響を与えます。(2)電極シートの一部に過電圧が発生します。コーティング中の一部の部品の厚さが大きすぎるため、圧延後に過圧が発生する場合があります。活物質粒子は過電圧の位置で壊れ、活物質粒子間の接触は密集しています。バッテリーセルの充電および放電プロセス中に、電子伝導率は向上しますが、イオン移動チャネルが減少またはブロックされ、容量開発に役立たず、放電プロセス中に、分極が増加し、電圧が低下し、容量が減少します。同時に、過電圧は電解液の濡れ効果に影響を与え、これもバッテリーの性能に大きな影響を与えます。
技術的プロセスの観点から、圧延の品質は、その後の電極シート加工効果に直接影響します。圧延後の電極シートの理想的な状態は、電極シートの表面が平らで、光沢が一定で、ブランク部分に明らかな波がなく、電極シートに大きな反りがないことです。しかし、実際の生産では、操作性や設備の運用により、どうしても問題が生じ、後工程での電極シートのスリットに影響が出る結果となり、スリット電極シートの幅がバラバラになったり、電極シートのバリが発生したりします。圧延の結果は、電極シートの巻線にも影響します。激しい反りは、電極シートの巻線プロセス中に電極シートとダイヤフラムの間に大きなギャップを引き起こします。ホットプレス後、多層ダイヤフラムの一部が重ね合わされ、これが応力集中点となり、セルの性能に影響を与えます。
ローラープレス技術の高度なレベルを測定するには、主に表面密度と圧縮密度に依存します。現在の主要な機器は、リン酸鉄リチウムカソード材料の比容量を200 mAh / gに到達させ、リン酸鉄リチウムカソード材料の圧縮密度を1.5 g / cm ^ 3に到達させることができます。