Generally speaking, there are two major production steps in battery manufacture.
1.Battery cell: the battery cell is composed of positive electrode material, negative electrode material, electrolyte, separator, additives…… and is packaged together by aluminum-plastic film or shell. It is just a combination of various materials and only have current and voltage, cannot be used directly.
2.Pack: Pack is to connect the battery cells in series or in parallel to meet the final design voltage and current requirements, and has the function of intelligent management. In special cases, the cells are neither connected in series nor in parallel, and are used directly after pack processing, such as mobile phone battery. This article will roughly describe the mobile phone battery pack flow steps.
The main materials involved in mobile phone battery packing are roughly as follows. Each brand has different requirements, and the materials may be slightly different. Some brands even require low-pressure injection molding, some have to stick the entire label at the end, and some only require pad printing, which does not affect the main steps of the mobile phone battery pack.
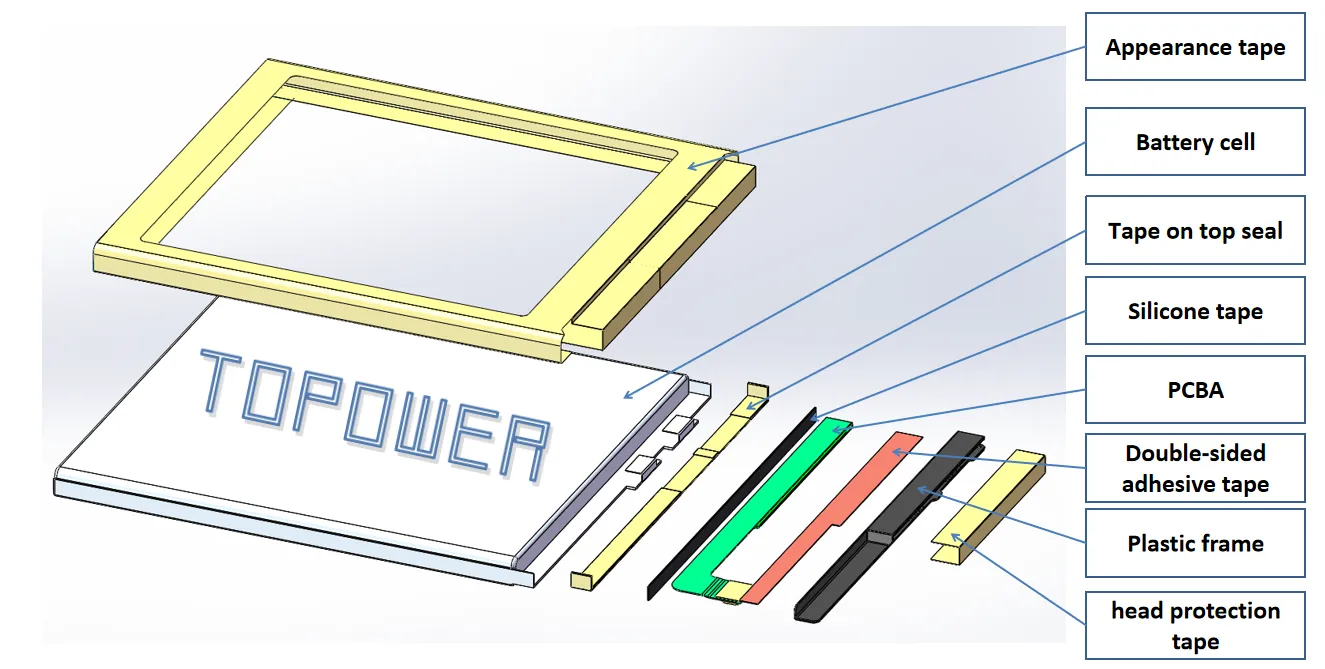
Mobile phone cell is as below:
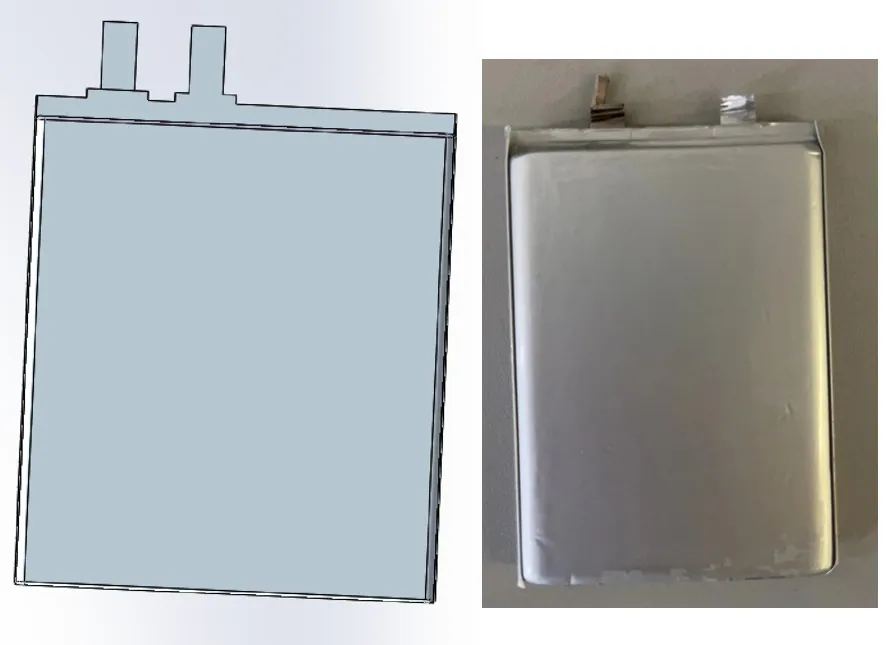
The main steps are as below:
1.Stick Top Seal:
The top seal needs to be pasted with tape, and the material is Mylar tape, which plays a role in protecting the seal. This step can be done manually, but the accuracy is not high and the speed is slow. Using automatic machine to stick can get high-precision and fast results
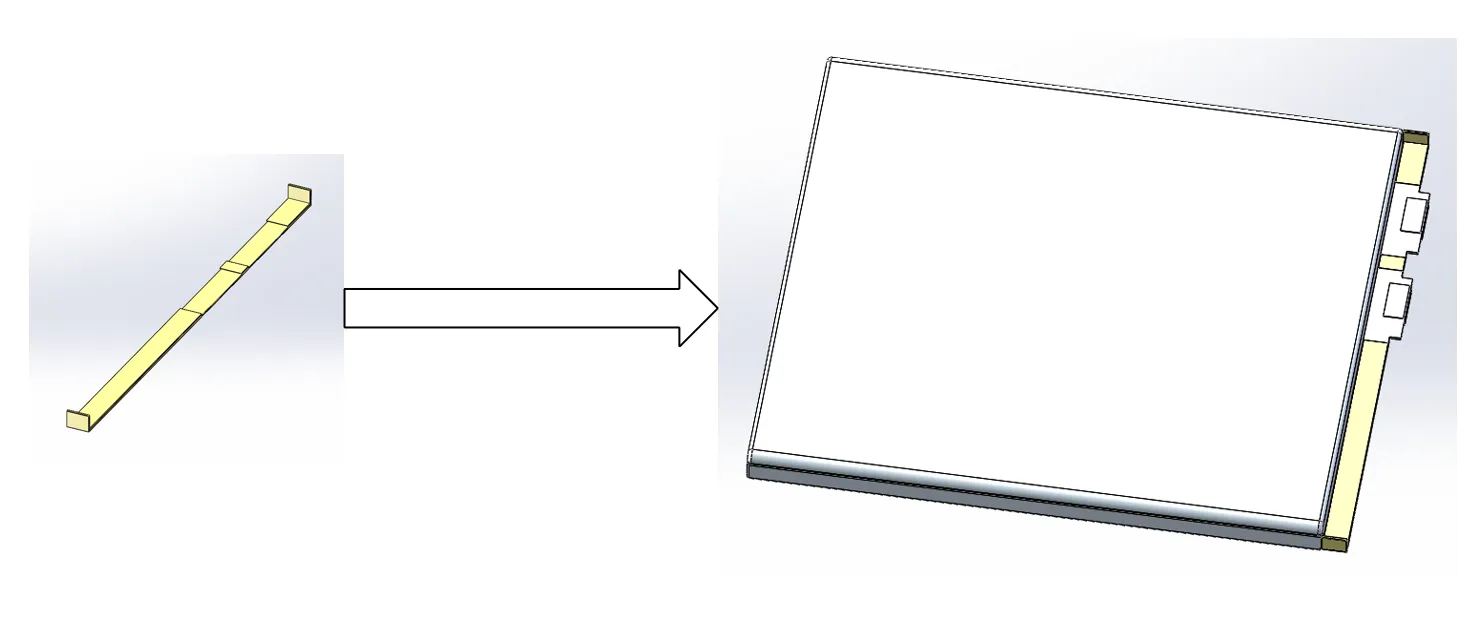
2.Stick Silicone tape:
Silicone tape needs to be pasted here to play a buffer role when the tabs are folded.This step can be done manually, but the accuracy is not high and the speed is slow. Using automatic machine to stick can get high-precision and fast results.
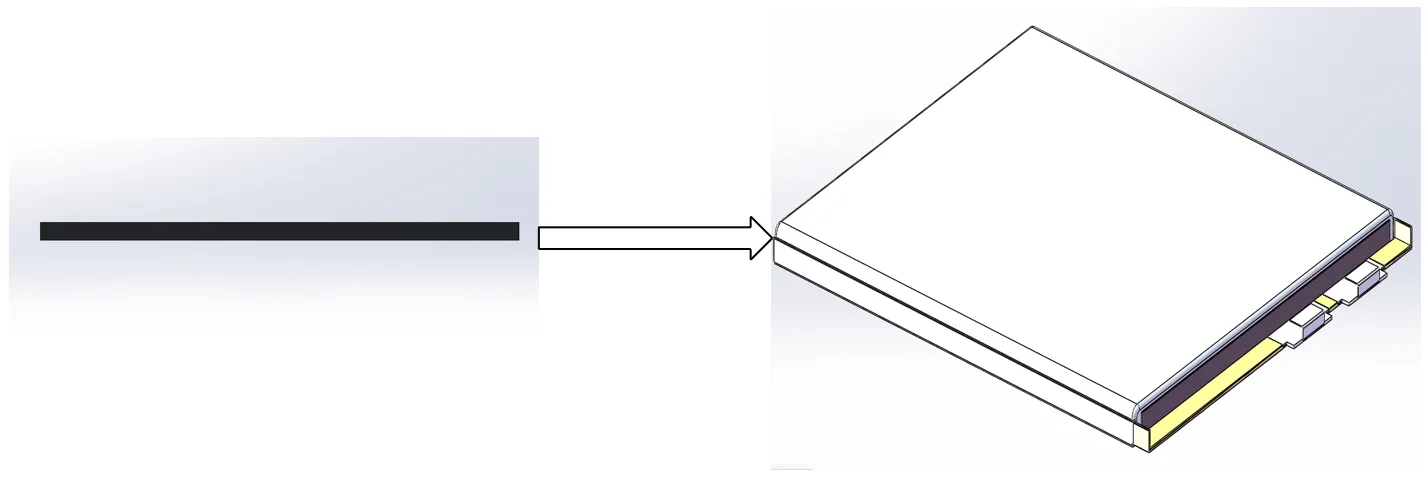
3. PCBA welding:
Weld the PCBA(BMS) to the positive and negative electrodes of the cell with laser welding machine. It requires accurate welding position, precise control of welding current, no false welding, no over welding, this is the most important step in packing. This step can be done manually, but the accuracy is not high and the speed is slow. Using automatic machine to stick can get high-precision and fast results
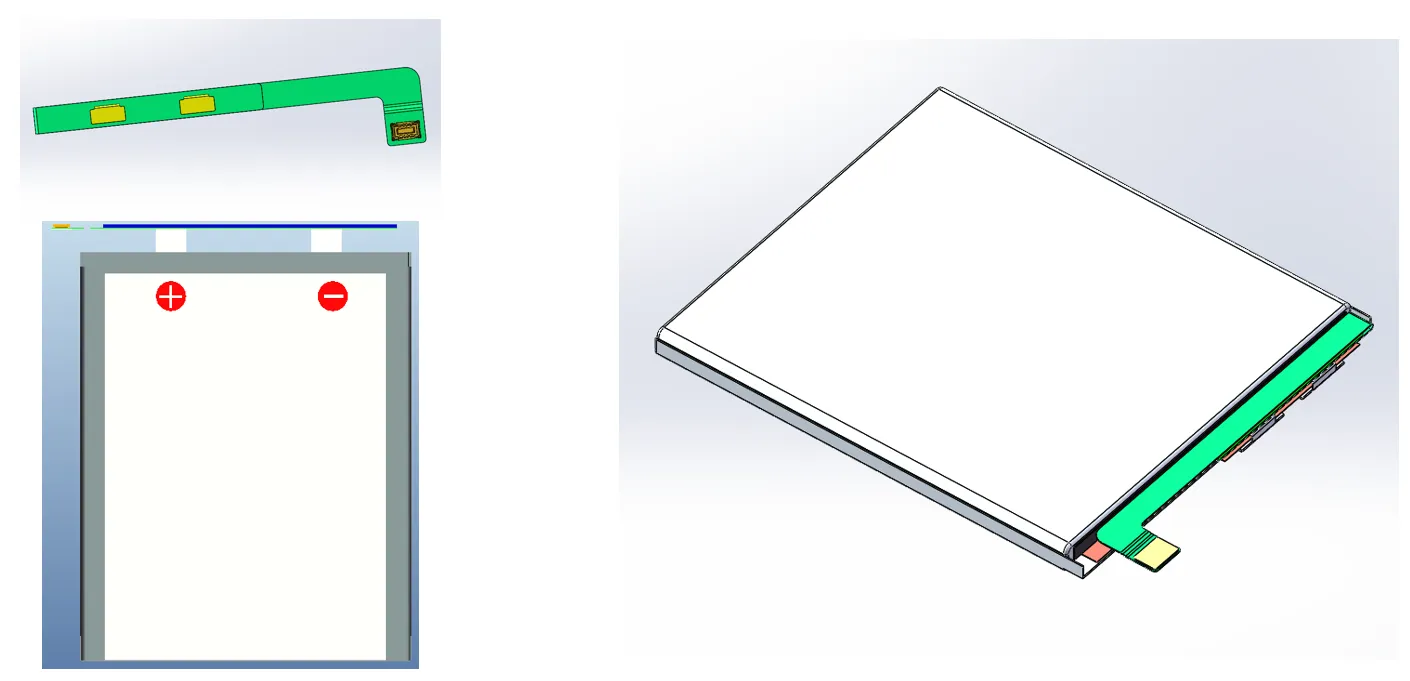
4.Stick Double-sided adhesive tape:
The function of pasting the double-sided adhesive tape is to stick the bent PCBA and prevent it from returning, likewise, automated machine operations can achieve high speed and high precision
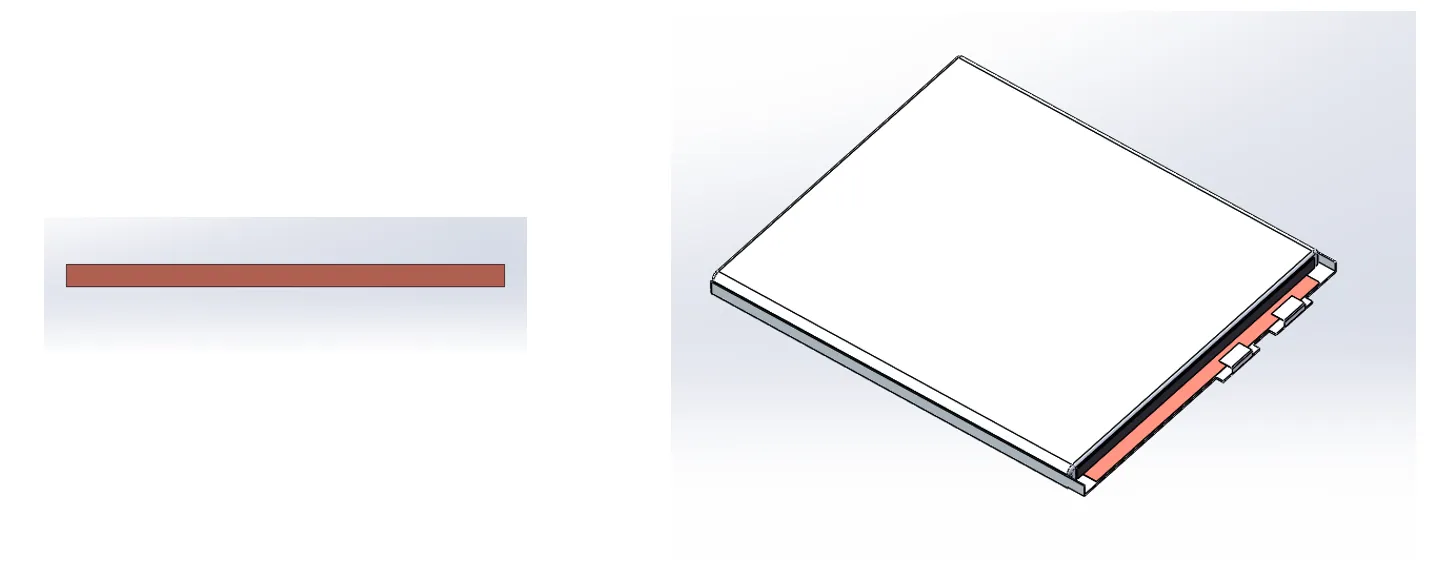
5. Tab bending:
The PCBA after laser welding is bent to location of the top seal together with the tabs to protect the PCBA, bend machine will be used here.
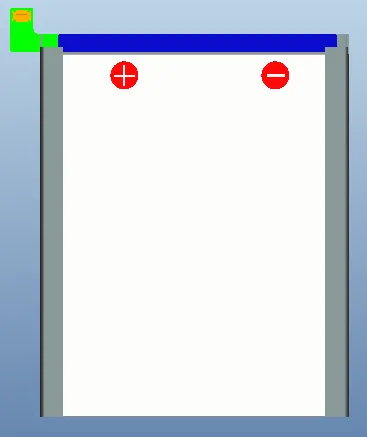
6. Stick head protection tape and appearance tape:
If use machine to finish this step, 2~4 set machine will be used here.
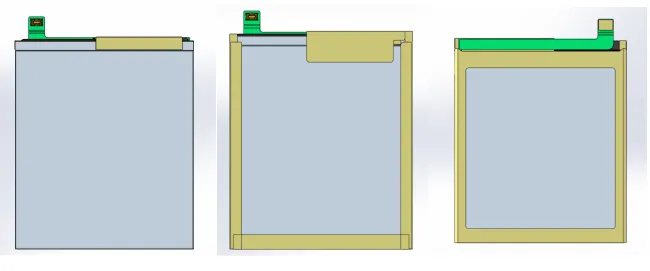
7.Battery Inspection:
So far, the pack processing of the battery has been completed, followed by routine inspection, each battery must be inspected, including battery size inspection, performance inspection, liquid leakage inspection. In addition, the battery should be tested for safety, reliability and environment, such as cycles high temperature and high humidity, rapid temperature shock, high and low temperature changes, vibration test, heavy object shock, thermal abuse, overcharge, forced discharge, short circuit, mechanical shock, temperature cycling, ESD (Electrostatic Discharge), constant damp heat, vibration, free fall, low air pressure…… these items are not tested by per battery, they might be done by batch or several batches, and different brands have different requirements.
We have been producing this kind of production line since 2015, and now we have developed to the fifth generation technology. According to customer requirements, we make full use of our years of accumulated experience to avoid practical problems encountered in production, can realize complete automation of the above, save you time, save your cost.
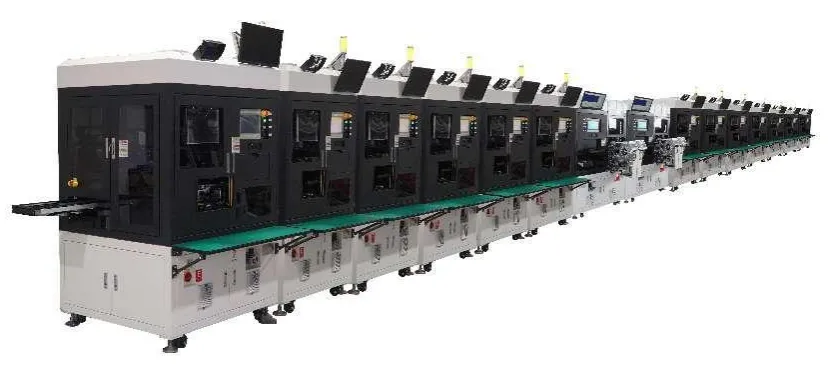