Lithium battery materials are located at the upstream of the entire lithium battery industry chain and mainly consist of four major materials: cathode materials, anode materials, separators, and electrolytes.
Cathode materials are the determining factor for the electrochemical performance of lithium batteries, directly influencing the battery’s energy density and safety, and thus affecting the overall performance of the battery. Although this segment has a high output value, it faces pressure from both upstream resources and downstream battery manufacturers in terms of bargaining power.
Since the proportion of cathode materials in the cost of lithium battery materials is around 30-40%, their cost directly determines the overall cost of the battery. Therefore, cathode materials play a crucial role in lithium batteries and directly lead the development of the lithium battery industry.
At the current stage, a Matthew effect is forming among various types of cathode materials. Products are becoming stratified, and in the mainstream product lines, a dynamic game has emerged among several leading manufacturers.
1.Classification of lithium battery cathode material systems
Lithium batteries can be divided into different technological routes based on the cathode material system. The main routes include lithium cobalt oxide (LCO), lithium manganese oxide (LMO), lithium iron phosphate (LFP), and ternary materials (nickel cobalt manganese oxide (NCM) and nickel cobalt aluminum oxide (NCA)).
Lithium cobalt oxide (LCO) has higher costs and a shorter lifespan, primarily used in consumer electronic products (3C products). Lithium manganese oxide (LMO) has lower energy density, a shorter lifespan, but lower costs, mainly used in specialized vehicles. Lithium iron phosphate (LFP) has a longer lifespan, good safety, and lower costs, primarily used in commercial vehicles. Ternary materials, especially NCM, have high energy density, good cycling performance, and a longer lifespan, mainly used in passenger vehicles.
High nickel content represents a new starting point, significantly raising the entry barrier for ternary materials. Currently, high nickel materials are further developing from the 8-series to the ultra-high nickel 9-series.
2. Competitive landscape of lithium battery cathode materials
China is the major hub for cathode material production, accounting for approximately 60% of global capacity. The domestic production capacity for cathode materials is substantial, and there is a gradual trend towards concentration among leading companies.
There are 11 representative enterprises in the battery materials industry in China, with four major players in the cathode material sector, namely, Easpring, Ronbay, ssgf, and dynanonic.
Currently, the global capacity layout of cathode material companies is no longer limited to their home countries but has become more globalized. Many companies are planning for the long term and expanding their presence in areas such as high-nickelization, high-voltage, and solid-state battery materials.
The customer structure for domestic cathode materials is further optimized, with a focus on leading battery manufacturers both domestically and overseas.
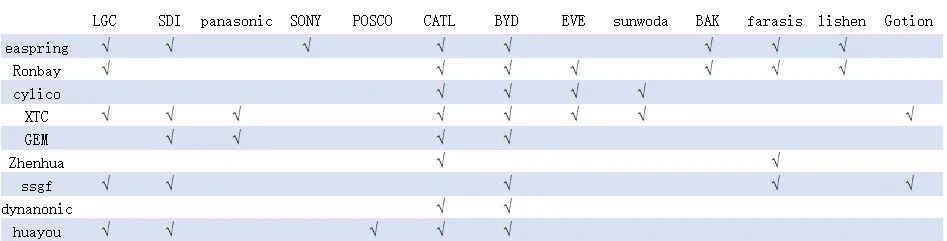
. 3. Ternary materials
Ternary materials have gained significant importance in the field of power applications due to their high energy density, and the development of power batteries has driven the increased demand for ternary materials. There are numerous participants in the domestic ternary cathode industry. However, due to the high capital expenditure and rapid technological iterations associated with investing in ternary material production capacity, the barriers to conventional ternary cathode manufacturing processes are relatively low. Additionally, there are a wide variety of derivative models, leading to technological divergence. As a result, the concentration of the ternary cathode industry has remained relatively low.
Competition among ternary material manufacturers is intense, and the market landscape is relatively fragmented. The market share gap between major players is small, but from a dynamic perspective, the industry concentration is showing an upward trend.
In the domestic ternary cathode market, companies such as Ronbay Lithium battery, Changyuan Lico, Hunan Shanshan, Easpring, Xiamen Tungsten, Zhenhua New Material, and Tianjin B&M still hold a major position.
4. High nickel ternary
The competition for conventional-type products in the ternary materials sector, where the level of homogeneity is high, is becoming increasingly fierce. This has forced companies to accelerate the development of new series products such as high-nickel and single-crystal materials, while also expanding their presence among leading battery enterprises. Although China accounts for over half of the global ternary materials production capacity, there is still room for improvement for domestic ternary material companies in the high-nickel market.
There are not many domestic companies that can achieve bulk shipments of high-nickel ternary materials. The companies with higher shipment volumes are mainly Ronbay, B&M, BTR, and Brunp. According to data from Huatai Securities, Ronbay’s high-nickel production accounts for about 70% of the market, placing it in a leading position in the high-nickel ternary industry. B&M, BTR, and Brunp are in the second-tier of the industry, while companies like Easpring, Changyuan Lico, Shanshan, and Zhenhua New Material are in the third tier, with some distance from the top four companies.
Considering the current supply pattern of domestic high-nickel ternary materials, the top companies in the first and second tiers are expected to continue expanding their shipment volumes, thus achieving a position as world-class high-nickel ternary material manufacturers. For companies in the third tier, the key goal for future development is to correctly grasp customer demands and produce differentiated products.
Due to the impact of the pandemic, many European and American automakers chose to shut down their factories. Companies like Panasonic, LG, and Samsung also closed their battery plants in Europe and the United States. Toyota and Panasonic are also considering or shutting down their domestic factories in Japan, which to some extent, suppresses the demand for high-nickel ternary materials from Japanese and Korean companies in overseas markets.
5. Lithium Iron Phosphate
Although ternary lithium batteries are slightly inferior to lithium iron phosphate batteries in terms of safety and stability, they have advantages in battery energy density, material cost, and driving range that other batteries cannot match. Lithium iron phosphate batteries are mainly used in the domestic power sector, but their development has been almost stagnant in the past due to subsidy standards. However, with the outstanding cost-effectiveness of lithium iron phosphate batteries, their applications in non-power fields such as energy storage have been rapidly expanding.
At the cell level, lithium iron phosphate batteries have a significant cost advantage, and their overall cost is still significantly lower than that of ternary batteries. They have a cost advantage of over 50% in the cathode and over 20% at the cell level. Additionally, since they do not contain expensive metals such as cobalt and nickel, the price fluctuations of lithium iron phosphate are much smaller than that of ternary batteries, which is beneficial for cost control.
Leading companies in the lithium iron phosphate battery industry are increasing their technological advantage through differentiated innovation. From the perspective of production capacity planning, the concentration of the lithium iron phosphate industry will significantly increase, and it has already entered a phase of fierce competition among leading manufacturers.
Among the mainstream companies, BYD and Gotion mainly use lithium iron phosphate batteries for self-use, while Dynanonic, BTR, Hunan Yueneng, and Hbwanrun sell them to foreign customers.
From the perspective of battery pack and structural innovation, lithium iron phosphate batteries have an advantage due to their maturity and stability in “blade” and “CTP” structures, as well as grouping efficiency. However, with the technological development and maturity of ternary, especially high-nickel ternary batteries, there is also room for improvement, and the gap will narrow.
CATL’s “CTP” technology can increase the energy density of lithium iron phosphate batteries to over 160Wh/kg, and when applied to ternary batteries, it can increase it to over 200Wh/kg.
Apart from CATL and BYD, which have high market shares in both ternary and lithium iron phosphate battery routes, other competitors mostly focus on one technology route. For example, there are companies like Lishen, CALB, and Farasis Energy focusing on ternary batteries, and companies like Gotion and EVE Energy focusing on lithium iron phosphate batteries. Previous power battery suppliers such as OptimumNano and BAK Battery have gradually reduced their market shares and their production capacity has been cleared out.
6. Lithium cobalt oxide material
Lithium cobalt oxide is mainly used in the consumer electronics sector and its market performance is closely related to the prosperity of the consumer electronics industry. The competitive landscape of lithium cobalt oxide materials has been largely established, and the future introduction of high-voltage lithium cobalt oxide and other products may further increase barriers to entry, leading to a differentiation of demand between high-end and low-end segments. In the future, high-nickel ternary and lithium iron phosphate batteries will respectively dominate the major share of the domestic power battery market due to their performance and price advantages. This will change the current situation where nickel-cobalt-manganese ternary batteries are predominant. It is expected that by 2025, the combined market share of high-nickel ternary and lithium iron phosphate batteries will exceed 80%.