Au cours du processus de fabrication des batteries lithium-ion, trois facteurs cruciaux doivent être strictement contrôlés : la poussière, les particules métalliques et l’humidité. Un mauvais contrôle de la poussière et des particules métalliques peut entraîner directementcourts-circuits interneset les accidents d’incendie dans la batterie. De même, un contrôle inadéquat de l’humidité peut également causer des dommages importants aux performances de la batterie et entraîner de graves accidents de qualité. Par conséquent, il est essentiel de maintenir un contrôle strict de la teneur en eau des matériaux clés tels que les électrodes, les séparateurs et les électrolytes tout au long du processus de fabrication, sans aucun relâchement. Ce qui suit fournira une explication détaillée de trois aspects : les dangers de l’humidité dans les batteries au lithium, les sources d’humidité pendant laProcessus de fabricationet le contrôle de l’humidité pendant le processus de fabrication.
01Les méfaits de l’humidité sur les batteries au lithium
- Gonflement et fuite de la batterie
Si la teneur en humidité d’une batterie lithium-ion est trop élevée, elle peut réagir avec le sel de lithium dans l’électrolyte, générant du HF (fluorure d’hydrogène) :
H2O + LiPF6 → POF3 + LiF + 2HF
Le fluorure d’hydrogène (HF) est un acide hautement corrosif qui peut causer des dommages importants aux performances des batteries. HF peut corroder les composants métalliques internes de la batterie, le boîtier de la batterie et les joints, entraînant des fuites et finalement provoquant la rupture de la batterie.
HF peut également perturber le film d’interface électrolytique solide (SEI) à l’intérieur de la batterie. HF peut réagir avec les principaux composants du film SEI :ROCO2Li + HF → ROCO2H + LiFLi2CO3 + 2HF → H2CO3 + 2LiF
Enfin, la formation de précipitations de LiF à l’intérieur de la batterie entraîne des réactions chimiques irréversibles entre les ions lithium et l’électrode négative, entraînant une consommation d’ions lithium actifs et une réduction de l’énergie de la batterie.
Lorsqu’il y a une quantité importante d’humidité, la génération de gaz augmente, ce qui entraîne une augmentation de la pression interne à l’intérieur de la batterie. Cela peut entraîner la déformation de la batterie en raison de la force appliquée, entraînant des risques tels que le gonflement et les fuites de la batterie.
Les cas de gonflement de la batterie ou d’ouverture du couvercle de l’appareil, couramment rencontrés sur les smartphones ou les produits électroniques numériques sur le marché, sont principalement causés par une teneur élevée en humidité et une génération de gaz dans la batterie lithium-ion.
- La résistance interne de la batterie augmente
La résistance interne est l’un des paramètres de performance les plus importants d’une batterie. Il sert d’indicateur principal de la facilité ou de la difficulté du transport d’ions et d’électrons dans la batterie, ce qui a un impact direct sur la durée de vie et l’état de fonctionnement de la batterie. Une résistance interne plus faible entraîne une chute de tension plus faible lors de la décharge de la batterie, ce qui permet une sortie d’énergie plus élevée.
Lorsque la teneur en eau augmente, cela peut entraîner la formation de POF3 et le LiF précipite à la surface du film d’interface électrolytique solide (SEI) dans la batterie. Cela perturbe la compacité et l’uniformité du film SEI, augmentant progressivement la résistance interne de la batterie. Par conséquent, la capacité de décharge de la batterie diminue continuellement.
- Durée de vie du cycle raccourcie
Lorsque la teneur en eau est trop élevée, elle endommage le film SEI de la batterie, entraînant une augmentation progressive de la résistance interne. En conséquence, la capacité de décharge de la batterie diminue et le temps d’utilisation par charge complète devient également plus court. Le nombre de cycles de charge-décharge que la batterie peut subir avant de subir une dégradation diminue naturellement, ce qui entraîne une durée de vie globale plus courte de la batterie.
02 Sources d’humidité dans le processus de production des batteries au lithium
-
Humidité apportée par les matières premières
- 1Matériaux des électrodes positives et négativesLes matériaux actifs dans les électrodes positives et négatives des batteries sont constitués de particules à l’échelle micro et nanométrique, qui sont très susceptibles d’absorber l’humidité de l’air. Cela est particulièrement vrai pour les matériaux d’électrodes positives ternaires ou binaires à forte teneur en nickel (Ni), car ils ont une surface relativement grande qui facilite l’absorption de l’humidité et les réactions ultérieures. Une fois les électrodes revêtues, si elles sont stockées dans un environnement très humide, le revêtement de surface des électrodes peut rapidement absorber l’humidité de l’air.
- 2Électrolyte:Le composant solvant de l’électrolyte peut subir des réactions chimiques avec les molécules d’eau. De plus, les sels de lithium solutés dans l’électrolyte sont également susceptibles d’absorber l’humidité et de subir des réactions chimiques. En conséquence, il y a une certaine quantité d’eau présente dans l’électrolyte. Si l’électrolyte est stocké pendant une période prolongée ou dans un environnement à haute température, la teneur en eau de l’électrolyte peut augmenter.
- 3Séparateur:Le séparateur est un film plastique poreux (en matériau PP / PE), et il a une capacité d’absorption d’eau importante.
- Humidité ajoutée à la mise en pâte de la feuille d’électrode :Lors de la préparation de la suspension d’électrode négative, de l’eau est ajoutée et mélangée aux matières premières avant le processus de revêtement. En conséquence, la feuille d’électrode négative elle-même contient de l’eau. Dans le processus de revêtement ultérieur, bien qu’il y ait chauffage et séchage, une quantité importante d’humidité est toujours absorbée dans le revêtement de la feuille d’électrode.
La teneur en humidité de l’air est généralement mesurée à l’aide de l’humidité relative. L’humidité relative peut varier considérablement en fonction des saisons et des conditions météorologiques. Au printemps et en été, l’air a tendance à être plus humide, avec une humidité relative supérieure à 60%. En automne et en hiver, l’air est relativement sec, avec une humidité inférieure à 40%. Les jours de pluie, l’humidité de l’air est plus élevée, tandis que les jours ensoleillés, l’humidité de l’air est plus faible. Par conséquent, la teneur en humidité de l’air varie en fonction des différents niveaux d’humidité relative.
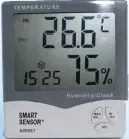
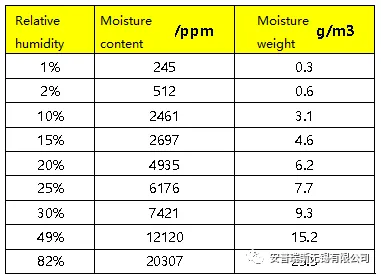
Eau produite par le corps humain (sueur du corps humain, souffle expiré, eau après s’être lavé les mains)
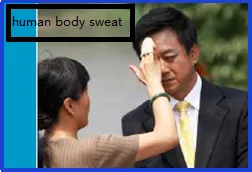
Humidité apportée par divers matériaux auxiliaires et papiers (cartons, chiffons, rapports)
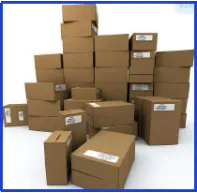
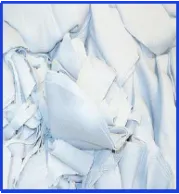
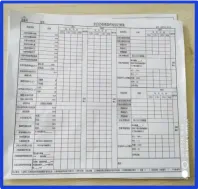
03Contrôle de l’humidité pendant le processus de production des batteries au lithium
1.Contrôler strictement l’humidité ambiante dans l’atelier de production
1.1 Dans l’atelier de production d’électrodes, lors du mélange de boues, l’humidité relative doit être de ≤10%.
1.2 Dans l’atelier de production d’électrodes, pendant le revêtement (tête et queue) et le pressage des rouleaux, l’humidité du point de rosée doit être de ≤-10°C DP.
1.3 Dans l’atelier de production d’électrodes, lors du refendage, l’humidité relative doit être de ≤10%.
1.4 Dans l’atelier d’empilage, d’enroulement et d’assemblage des électrodes, l’humidité du point de rosée doit être de ≤-35°C DP.
1.5 Lors de l’injection et de l’étanchéité de la cellule, l’humidité du point de rosée doit être de ≤-45°C DP.
2.Contrôle strict du corps humain et de l’humidité externe apportée dans l’atelier
2.1 Gestion de la conformité :
L’entrée dans l’atelier de séchage nécessite de changer de vêtements, de porter un chapeau, de changer de chaussures et de porter un masque.
Il est strictement interdit de toucher les feuilles d’électrodes et les cellules à mains nues.
2.2 Gestion de la contamination par l’humidité :
Il est strictement interdit d’introduire des cartons dans l’atelier de séchage.
Les affiches et les panneaux en papier à l’intérieur de la zone de séchage doivent être plastifiés.
Le nettoyage à l’eau est interdit dans la zone de séchage.
3. Contrôle strict du stockage de la feuille d’électrode et du temps d’exposition :
3.1 Gestion du stockage à faible humidité :
Les feuilles d’électrodes après le pressage et la refendage du rouleau doivent être stockées dans un environnement à faible humidité dans les 30 minutes (≤-35°C DP).
Les feuilles d’électrodes qui ont été cuites mais qui n’ont pas été traitées rapidement (bobinage du film) doivent être stockées sous vide (≤-95 kPa).
3.2 Gestion du temps d’exposition :
Après la cuisson, les feuilles d’électrodes doivent être traitées (bobinage du film), encapsulées, injectées d’électrolyte et scellées dans les 72 heures (humidité du point de rosée de l’atelier ≤-35°C).
3.3 Gestion FIFO (premier entré, premier sorti) :
L’utilisation de feuilles d’électrodes doit suivre le principe FIFO, où les lots produits précédemment sont utilisés en premier.
Les feuilles d’électrodes cuites doivent être utilisées dans l’ordre de cuisson.
4. Contrôlez strictement le processus de cuisson de la feuille d’électrode et du séparateur
4.1 Les feuilles d’électrodes et les séparateurs doivent être cuits (séchés) avant d’être utilisés.
4.2 Si les feuilles d’électrodes et les séparateurs ne sont pas cuits (séchés) avant l’enroulement du film, ils doivent être cuits (séchés) avant l’injection de la cellule.
4.3 Pendant le processus de cuisson (séchage) des feuilles d’électrodes ou des cellules, les paramètres du four (température, temps, niveau de vide) doivent être strictement surveillés.
4.4 La température et le niveau de vide du four doivent être régulièrement calibrés pour assurer la précision.
5. Analyse et contrôle de la teneur en eau
5.1 La teneur en eau des feuilles d’électrodes, des séparateurs (ou cellules) et de l’électrolyte doit être testée, et ce n’est que s’ils répondent aux exigences que la cellule peut être remplie.
5.2 Méthode d’essai : Échantillonnage conformément à la réglementation et mesure à l’aide d’un testeur d’humidité Karl Fischer.
5.3 Critères d’acceptation de la teneur en eau :
Teneur en eau de la feuille d’électrode ≤200 ppm (pré-contrôle ≤150 ppm)
Teneur en eau du séparateur ≤600 ppm
Teneur en eau électrolytique ≤20 ppm

En résumé, dans le processus de fabrication des batteries au lithium, le contrôle de l’humidité ambiante, le stockage et le temps d’exposition des feuilles d’électrodes, les processus de séchage et de déshumidification des feuilles d’électrodes et des séparateurs, les dates d’expiration des électrolytes et les tests de teneur en eau sont tous essentiels. L’absence de contrôle de ces facteurs peut entraîner de graves défauts dans les performances des lots de batteries, avec de graves conséquences. Par conséquent, qu’il s’agisse du personnel de direction, des opérateurs de production ou des inspecteurs de la qualité, il est crucial d’améliorer la sensibilisation au contrôle de l’humidité dans les batteries et de respecter strictement les réglementations tout au long du processus de fabrication pour s’assurer que la teneur en humidité des batteries reste contrôlée et dans des limites acceptables.