在锂离子电池的制造过程中,必须严格控制三个关键因素:灰尘、金属颗粒和水分。对灰尘和金属颗粒的控制不佳会直接导致内部短路以及电池中的火灾事故。同样,湿度控制不当也会对电池性能造成重大损害,并导致严重的质量事故。因此,在整个制造过程中,必须严格控制电极、隔膜和电解液等关键材料的含水量,不得有任何放松。下面将从三个方面进行详细的讲解:锂电池中受潮的危害、受潮过程中的受潮来源制造工艺以及制造过程中的湿度控制。
01湿气对锂电池的危害
- 电池鼓起和漏液
如果锂离子电池中的水分含量过高,它会与电解液中的锂盐发生反应,产生HF(氟化氢):
H2O +氯化锂6 → POF3 + LiF + 2HF
氟化氢(HF)是一种强腐蚀性酸,会对电池性能造成重大损害。HF会腐蚀电池的内部金属部件、电池外壳和密封件,导致泄漏并最终导致电池破裂。
HF还会破坏电池内部的固体电解质界面(SEI)膜。HF可以与SEI薄膜的主要成分发生反应:罗可2Li + HF → ROCO2H + LiFLi2CO3+ 2高频→ H2CO3+ 2LiF
最后,电池内部形成LiF沉淀物,导致锂离子与负极发生不可逆的化学反应,导致活性锂离子的消耗和电池能量的降低。
当水分大量时,气体产生量会增加,导致电池内部压力增加。这会导致电池因施加的力而变形,从而导致电池膨胀和泄漏等风险。
电池膨胀或导致设备盖弹开的情况常见于市场上的智能手机或数字电子产品,主要是由于锂离子电池内部的高水分含量和气体产生引起的。
- 电池内阻增大
内阻是电池最重要的性能参数之一。它是电池内离子和电子传输难易程度的主要指标,直接影响电池的循环寿命和运行状态。较低的内阻会导致电池放电期间的电压降较低,从而实现更高的能量输出。
当含水量增加时,会导致电池中固体电解质界面(SEI)膜表面形成POF3和LiF沉淀物。这破坏了SEI薄膜的致密性和均匀性,逐渐增加了电池的内阻。因此,电池的放电容量不断降低。
- 循环寿命缩短
当含水量过高时,会损坏电池的SEI膜,导致内阻逐渐增加。结果,电池的放电容量降低,每次充满电的使用时间也变得更短。电池在退化之前可以经历的充放电循环次数自然会减少,从而导致电池的整体使用寿命缩短。
02锂电池生产过程中的水分来源
-
原材料带来的水分
- 1正负极材料:电池正负极中的活性物质都由微米级和纳米级的颗粒组成,它们极易从空气中吸收水分。对于镍(Ni)含量高的三元或二元正极材料尤其如此,因为它们具有相对较大的表面积,有助于吸收水分和后续反应。电极涂覆后,如果存放在高湿度环境中,电极的表面涂层可以迅速吸收空气中的水分。
- 2电解质:电解质中的溶剂成分可以与水分子发生化学反应。此外,电解质中的溶质锂盐也容易吸收水分并发生化学反应。因此,电解质中存在一定量的水分。如果电解液长时间储存或在高温环境中储存,电解液中的水分含量会增加。
- 3分隔符:隔板是一种多孔塑料薄膜(由PP/PE材料制成),具有显着的吸水能力。
- 添加到电极片制浆中的水分:在负极浆料制备过程中,在涂布过程之前加入水并与原材料混合。结果,负极片本身含有水。在随后的涂布过程中,虽然涉及加热和干燥,但电极片的涂层内仍会吸收大量的水分。
空气中的水分含量通常使用相对湿度来测量。相对湿度会因季节和天气条件的不同而有很大差异。春季和夏季,空气趋于潮湿,相对湿度超过60%。秋冬季节,空气相对干燥,湿度低于40%。雨天,空气湿度较高,而晴天,空气湿度较低。因此,空气中的水分含量根据相对湿度的不同水平而变化。
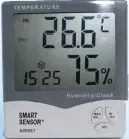
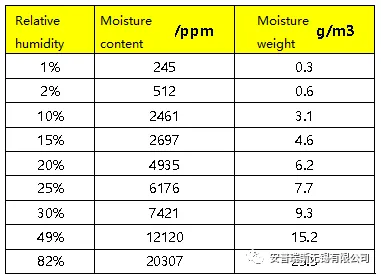
人体产生的水(人体汗液、呼出的气息、洗手后的水)
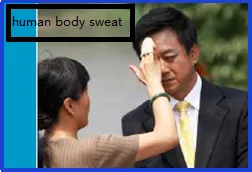
各种辅助材料和纸张(纸箱、碎布、报告)带来的水分
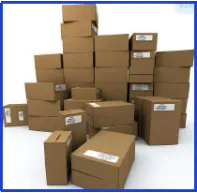
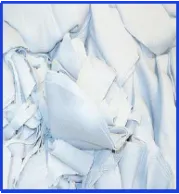
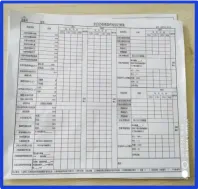
03锂电池生产过程中的水分控制
1.严格控制生产车间的环境湿度
1.1在电极生产车间,浆料混合时,相对湿度应为≤10%。
1.2在电极生产车间,涂布(头尾)和辊压过程中,露点湿度应≤-10°C DP。
1.3在电极生产车间,分切时,相对湿度应为≤10%。
1.4在电极堆放、绕组、组装车间,露点湿度应为≤-35°C DP。
1.5在电池注射和密封过程中,露点湿度应为≤-45°C DP。
2.严格控制带入车间的人体和外部湿气
2.1合规管理:
进入烘干车间需要换衣服、戴帽子、换鞋、戴口罩。
严禁徒手触摸电极片和电池。
2.2湿气污染管理:
严禁将纸板箱带入烘干车间。
干燥区内的纸质海报和标志必须层压。
晾衣区禁止拖水。
3.严格控制电极片的储存和曝光时间:
3.1低湿度储存管理:
辊压和分切后的电极片必须在30分钟内(≤-35°C DP)存放在低湿度环境中。
已烘烤但未及时处理(薄膜缠绕)的电极片必须在真空(≤-95kPa)下保存。
3.2曝光时间的管理:
烘烤后,电极片必须在72小时内进行加工(薄膜缠绕)、封装、注入电解液并密封(车间露点湿度≤-35°C)。
3.3先进先出(FIFO)管理:
电极片的使用必须遵循FIFO原则,即首先使用较早生产的批次。
烘烤的电极片应按照烘烤的顺序使用。
4.严格控制电极片和隔膜的烘烤过程
4.1电极片和隔板在使用前必须经过烘烤(干燥)。
4.2如果电极片和隔膜在薄膜缠绕前没有烘烤(干燥),则必须在电池注射前烘烤(干燥)。
4.3在电极片或电极片的烘烤(干燥)过程中,必须严格监控烘箱的参数(温度、时间、真空度)。
4.4必须定期校准烘箱的温度和真空度,以确保准确性。
5.含水量检测与控制
5.1必须测试电极片、隔板(或电池)和电解液的含水量,只有符合要求才能填充电池。
5.2测试方法:根据规定取样并使用卡尔费休水分测试仪进行测量。
5.3含水量验收标准:
电极片含水量≤200ppm (预控≤150ppm)
分离器含水量≤600ppm
电解质含水量≤20ppm

综上所述,在锂电池的制造过程中,控制环境湿度、电极片的储存和暴露时间、电极片和隔膜的干燥和除湿过程、电解液的有效期以及水分含量的测试都是必不可少的。未能控制这些因素会导致电池批次的性能出现严重缺陷,从而造成严重后果。因此,无论是管理人员、生产操作员还是质量检查员,都必须加强电池的水分控制意识,并在整个制造过程中严格遵守法规,以确保电池的水分含量保持受控并在可接受的范围内。