Electric vehicle batteries(this article focuses on two wheeler batteries) are the source of power on electric vehicles. The battery drives the motor through the controller, converts electrical energy into mechanical energy, and drives the motor to rotate, so that the electric vehicle runs.
The battery, controller, and motor form an electric vehicle power system. In the system, the battery provides power, the motor rotates, and the controller controls and protects the battery and the motor to achieve controllable and safe work between the battery and the motor. The controller is the core control component.
The controller’s control of the battery includes two parts, one is current limiting, and the other is undervoltage protection. The current limit value must be less than the overcurrent protection value of the PCM, otherwise the PCM will be protected in advance, resulting in a malfunction and affecting the use. The undervoltage protection value of the controller is higher than the overdischarge protection of the PCM, otherwise it will cause abnormal power failure, shorten the riding distance, and cause customer complaints.
Because the motor is an inductive load, the starting current of the electric vehicle is greater than the normal working current, which is generally twice the working current, and the overload current of the controller is also twice the rated current. The standard requirement for withstand overload time is 3min. The maximum operating current of the battery PCM is required to be greater than twice the current limit of the controller
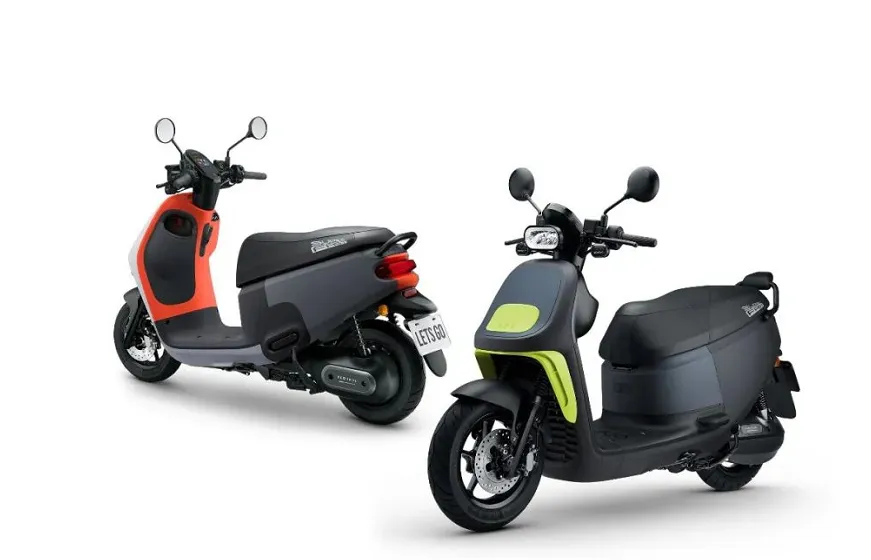
Application field requirements for batteries
A. The battery is required to have good consistency. Common electric bicycle batteries have three working voltages, 36V/48V/60V, and the capacity ranges from 10Ah to 30Ah. Whether it is a pouch pack or a cylindrical pack, connection in series or parallel are required. If the consistency is poor, it will affect the battery capacity. The battery with the lowest capacity in a group determines the capacity of the entire group of batteries.
B. High current discharge performance is required. According to the load analysis of the electric bicycle battery, the discharge current is between 0.5C and 1C under normal driving conditions. If there is an uphill road, the discharge current is larger, and the discharge exceeds 1C for a long time. Therefore, the electric vehicle battery must meet the high current discharge requirements.
C. The battery is required to have good heat dissipation.For the battery, discharging more than 1C means that the battery has a temperature rise of more than 20% in the environment.The number of electric vehicle batteries is large, and the internal battery temperature rise is not easy to dissipate, resulting in uneven temperature between batteries, inconsistent discharge curves, and inconsistent capacity.A long time will lead to inconsistent life between the batteries, which is manifested as a shortened riding distance and a faster shortening time.
D. The battery structure is required to be reasonable and the production technology level is high. The battery must be able to withstand the vibration shock of bumpy road surfaces. The production process, especially the spot welding process, has high requirements. The spot welding is required to be firm, and the shock absorption protection is required to be good. Avoid shaking the battery in the case.
E. The battery cycle life is required to be high. Compared with lead-acid batteries, lithium batteries are lighter in quality but higher in price. If the lifespan cannot be higher than that of lead-acid batteries, the market recognition will definitely be reduced. Lifespan is guaranteed by excellent quality.
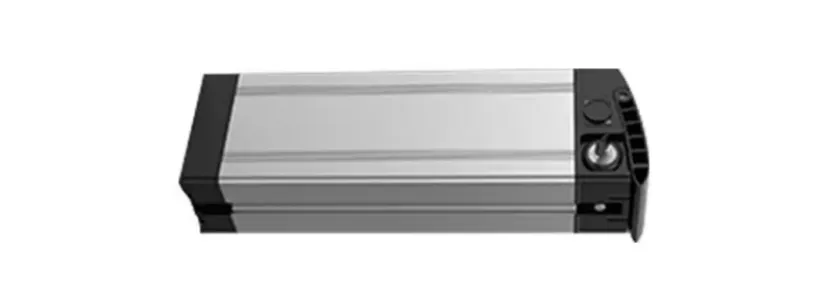
Quality Control
In view of the above requirements for electric vehicle batteries, in order to meet these requirements, the following measures should be taken.
A. Use high-quality cells. Qualified and stable suppliers are required to provide cells with good performance. The cells need to be done a series of safety tests and performance tests before being used.
B. The internal resistance of the battery is required to be low and the consistency is good. Low internal resistance ensures the capacity, platform and heat dissipation of high current discharge.
C. The battery structure adopts ventilation design, and the distance between two cells is not less than 2mm. This structure requires the cells to be fixed with holder which normally plastic.
D. Use a reasonable battery assembly process and use better lithium ion battery machine, such as: Battery testing machine, Sorting machine, Barley paper sticking machine, lithium battery welding machine (lithium battery spot welding machine), these machines at least use Semi-automatic machine to ensure the consistency of product processing. The spot welding machine ensures stable work, and the welding needle ensures the quality. In addition, a vibration test is performed for each batch of products to verify the anti-vibration performance.
E. Different batches of batteries are made into typical finished products and subjected to life test, and the actual cycle life can be obtained by cycle test of battery finished products.
F. Verify the high and low temperature performance of the battery. Cells from different manufacturers are made into finished products and subjected to different rate discharge tests at high and low temperatures to obtain the actual discharge curve.
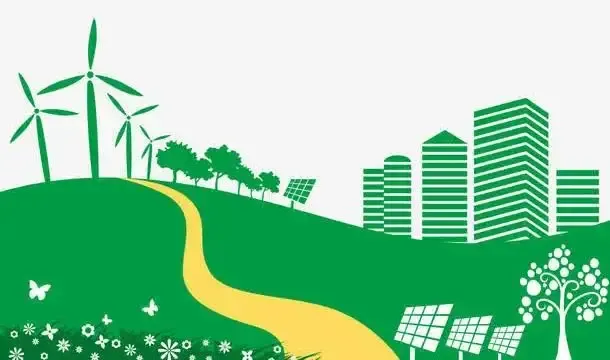