In the new energy industry, the production process of lithium batteries involves several key steps, including mixing and slurring, coating, winding, cutting and shaping, stacking or winding, assembly, electrolyte injection, sealing and welding, and packaging. During the processes of mixing and slurring, cutting and shaping, winding or stacking, as well as sealing and welding, a significant amount of dust or smoke is generated. It is necessary to collect the dust in a reasonable and scientific manner.
The production of lithium batteries in the new energy industry generates various types of dust and smoke. If not dealt with in a timely manner, it can affect the quality of lithium batteries, damage processing equipment, and pose a threat to the health and safety of employees. Therefore, it is essential to implement dust removal measures for each process in lithium battery manufacturing to ensure the environmental quality of the production process.
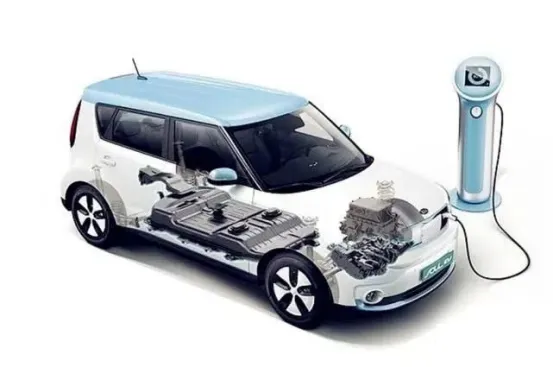
What are the various dust control solutions for lithium batteries in the new energy industry? Below we will briefly introduce the dust removal solutions for the following process links:
1.Slitting and die cutting
The rolled aluminum foil is cut according to the required size for battery production while effectively controlling the generation of burrs. This is done to prevent burrs from puncturing the separator, which could pose serious safety hazards. The dust or chips generated during the cutting process must be promptly removed using a vacuum system. Since the dust may have explosive potential, an explosion-proof dust collector is required. Additionally, for the chips, it is necessary to increase the negative pressure of the dust collector.
2.Mixing and slurring
The mixing and slurring process involves blending the positive and negative electrode solid battery materials and adding solvents to create a slurry. The slurry mixing is the starting point of the preceding processes such as coating and winding, serving as the foundation for subsequent steps. It is crucial to strictly control dust in this step to prevent any impact on the consistency of the batteries. The production environment requirements for this process are equivalent to pharmaceutical-grade standards. Typically, dust collectors are used in this process to ensure effective dust control.
3.Sealing and welding
This step involves sealing and welding the battery after the electrolyte injection and adding the cap. Due to the generation of smoke during laser welding, an automatic welding smoke purifier is required.
4.Winding or stacking
Depending on the type of battery production, there are two processes in this step: winding or stacking. However, regardless of the specific process, it is crucial to prevent any foreign particles or dust from adhering to the surface of the materials. Therefore, a high-negative-pressure vacuum dust collector is required in this step.
Dust control in the lithium battery industry
1.Dust removal system for thermal kilns in lithium battery material production
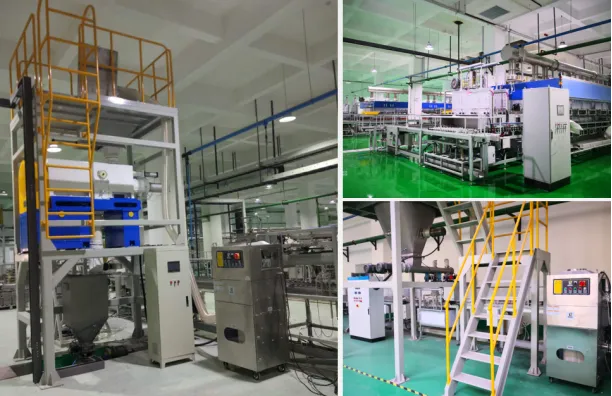
2.Dust removal for battery material mixing and stirring operations
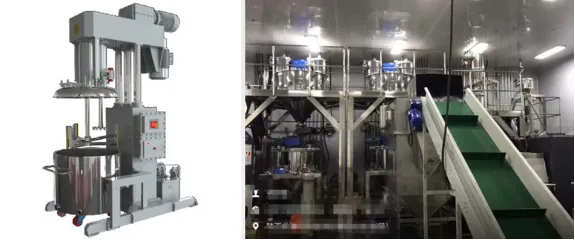
3.Dust removal system for electrode sheet slitting, trimming, cutting, cell winding, or stacking processes
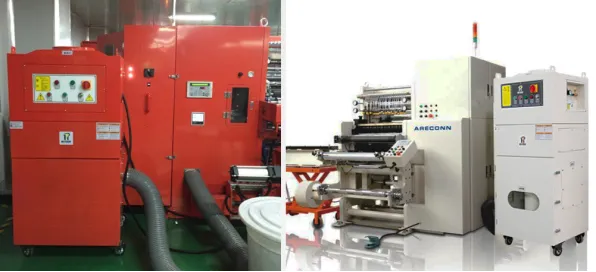
4.Dust control for cell packaging operations including laser welding, cleaning, and marking
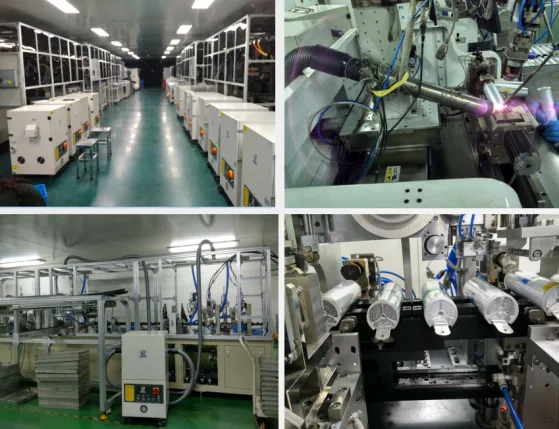