混合(正负极活性材料+导电剂+粘合剂+分散剂) -涂层-轧制——-切割-极耳焊接- -卷绕(或垫圈) -胶纸-插入电池外壳-焊接-密封-形成等。基本上整个行业的电池生产过程是相似的,主要区别在于设备或电池产品的不同。在软包电池的情况下,它们通常是堆叠的,而圆柱形电池是缠绕的,而棱柱形电池可以同时涉及缠绕和堆叠。这导致电池卷绕阶段的工艺不同。最重要和核心的技术在于混合和涂层工艺,以及最终的成型工艺。
锂电池的生产过程很复杂,主要涉及三个主要阶段:电极制造阶段(前端)与混合和涂层,电池组装阶段(中间阶段)与绕组和电解液注入,以及封装和测试阶段(后端)与形成和密封。价值分配(以采购金额计)约为前端35-40%,中期30-35%,后端30-35%。根据涂装设备供应商提供的信息,这些差异主要源于不同的设备供应商以及进口设备与国产设备的比例。然而,整个过程仍然相对一致,值分布略有偏差,但总体上与上述比例一致。
与前端工艺相对应的锂电池生产设备主要包括真空混合机、涂布机和压延机.对于中期工艺,设备包括模切机、绕线机、堆垛机和电解液注入机。后端流程涉及化成机、容量测试设备以及流程仓储和物流自动化。此外,电池组的生产需要电池组自动化设备。
锂电池生产前端过程的结果是制备正极和负极片。该工艺的第一步是混合,其中正负极的固态电池材料均匀混合,然后与溶剂混合形成浆料。混合成分是锂电池生产后续过程的基础。高质量的混合对于在随后的涂布和压延过程中获得高质量的结果至关重要。
涂布和压延过程之后,下一步是分切,包括将涂布材料切割成所需的宽度。如果在分切过程中出现毛刺或粗糙的边缘,可能会导致组装问题、电解液注入问题,甚至安全隐患在电池使用期间。因此,锂电池生产过程中的前端设备,如混合机、涂布机、压延机等分切机是电池制造的核心机器。它们极大地影响了整个生产线的质量。因此,前端设备在整个锂电池自动化生产线中具有最高的价值(以数量计),约占35%。
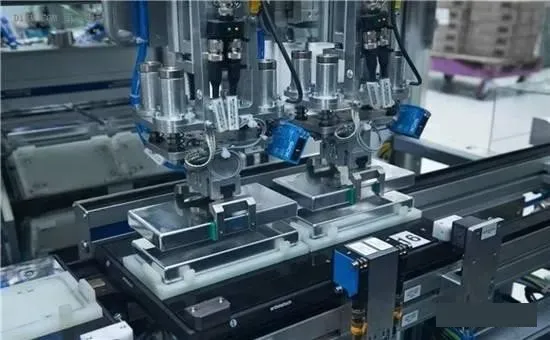
在锂电池的制造过程中,中间过程主要集中在电池的形成上。此阶段的主要过程包括电极制备、电极绕组、模切、电芯卷绕和堆叠。这一阶段是国内设备制造商之间竞争激烈的领域,约占锂电池生产线价值的30%。
目前,动力锂电池电芯的制造工艺主要包括卷绕和堆叠,对应三种电池结构形式:圆柱形、棱柱形和软包形。圆柱形和方形电池主要使用卷绕工艺生产,而软包电池主要使用堆叠工艺。圆柱形电池以18650和26650等格式表示(特斯拉自主研发了21700电池,正在业界广泛推广)。方形电池和软包电池的主要区别在于外壳,方形电池使用硬铝外壳,而软包电池使用铝塑料薄膜。软包电池的制造过程主要是堆叠,而铝壳电池的制造过程主要是绕组。
据了解,锂电池的软包结构主要针对中高端数字化市场,单位产品的利润率相对较高。在同等产能条件下,软包电池的利润率普遍高于铝壳电池。然而,由于易于实现规模经济和控制产品合格率和成本,铝壳电池在各自的市场领域也获得了可观的利润。可以预见,在可预见的将来,软包电池和铝壳电池都不太可能被完全取代。
由于能够通过转速实现高速生产,绕线工艺是目前国内动力锂电池生产采用的主要方法。另一方面,堆叠技术可实现的速度改进是有限的。因此,目前卷绕机的出货量高于堆垛机。收卷和堆叠生产的前道工序是电极准备和模切。电极制备包括焊接切割的电极/极耳、去除电极灰尘、涂抹保护胶带、封装极耳以及缠绕或切割成固定长度等过程。绕线电极用于随后的全自动绕线,而定长切割电极用于半自动绕线。模切包括切割和塑造缠绕的电极,用于后续的堆叠过程。
在锂电池封装焊接方面,Uwlaser、Hanslaser、Gdlaser等主流集成应用厂商均涉足激光技术领域。它们能够在不需要进口的情况下满足需求。
锂电池后端工艺流程:体积分离和化成是核心环节
锂的后生产过程电池制造主要包括分拣、形成、检测、包装入库,在生产线中约占价值的35%。化成和分选是后生产阶段的关键过程,涉及形成电池的活化测试。由于电池充电和放电的测试周期长,这些过程中使用的设备具有最高价值。化成过程的主要目的是在注射封装后通过充电来激活密封电池,而分拣过程涉及在激活后测试电池容量和其他电气性能参数,然后对其进行相应的分级。化成和分拣通常由化成机和分拣机组成的自动化系统执行。
锂电池组工艺:看似简单,但需要结合系统化设计
动力电池组系统由多个串联或并联的单个电池单元组成,集成了电源和热管理系统。该电池组是动力电池系统生产、设计和应用的关键部件。它是上游电池生产和下游车辆应用之间的纽带。通常,设计要求由电池制造商或汽车公司提出,通常由电池制造商、汽车公司或第三方电池组制造商完成。
锂电池组生产线比较简单,核心工序包括上料、支架组装、焊接、检测。核心设备包括激光焊接机和各类胶粘剂及检测设备。目前,包装生产的自动化水平相对较低。这主要是因为新能源汽车个别车型的销量不够大,不足以证明自动化生产线的高成本是合理的。
磷酸铁锂和三元:能量密度是回避不开的话题,不同的材料需要全套设备投入
目前,我国动力锂电池主流正极材料分为磷酸铁锂(LiFePO4)和三元材料两大类。其中,磷酸铁锂是最安全的锂离子电池正极材料,典型循环寿命超过2000次循环。此外,由于行业成熟以及价格和技术壁垒的降低,许多制造商出于各种原因选择磷酸铁锂电池。然而,磷酸铁锂电池在能量密度方面有一个明显的缺点。领先的磷酸铁锂电池制造商比亚迪的磷酸铁锂电池能量密度为150Wh,他们预计到160年底将增加到2017Wh。理论上,磷酸铁锂很难超过200Wh/kg的能量密度。
三元聚合物锂电池是指使用由锂镍钴锰氧化物组成的正极材料,根据具体需要调整镍、钴、锰的实际比例的锂电池。三元锂电池具有更高的能量密度(目前,宁德时代等一流动力电池制造商可以达到200Wh/kg-220Wh/kg的能量密度,预计到2020年,三元电池的能量密度将达到300Wh/kg)。因此,乘用车市场正在转向三元锂电池。另一方面,磷酸铁锂更受适用于安全要求较高的应用,例如公共汽车。随着纯电动乘用车的发展,三元锂电池越来越占据重要地位。
这两种材料在能量密度和成本方面存在差异,不同的车辆和汽车制造商会做出不同的选择。根据Tucbol的了解,两种材料的生产工艺总体上是相似的,但差异主要在于材料的使用和比例,以及具体工艺参数的显着变化。设备无法共享生产,简单改造或切换产能成本高(三元材料对真空除湿有严格的要求,这在以前的磷酸铁锂生产线上是不需要的)。因此,许多电池制造商通过同时部署和单独购买两种材料的设备来规划产能布局。