Mezcla (electrodo positivo y negativo, materiales activos + agente conductor + aglutinante + dispersante) – recubrimiento —– laminación ——- corte — soldadura de lengüetas — – bobinado (o junta) – papel adhesivo – inserción de la carcasa de la batería – soldadura – sellado – formación, etc. Básicamente, el proceso de producción de baterías en toda la industria es similar, la principal diferencia es que la diferencia en el equipo o los productos de batería son diferentes. En el caso de las celdas de bolsa, generalmente se apilan, mientras que las celdas cilíndricas se enrollan, y las celdas prismáticas pueden implicar tanto bobinado como apilamiento. Esto da lugar a diferentes procesos durante la etapa de bobinado de la celda. Las tecnologías más importantes y centrales se encuentran en los procesos de mezcla y recubrimiento, así como en el proceso de formación final.
El proceso de producción de baterías de litio es complejo e implica principalmente tres etapas principales: la etapa de fabricación de electrodos (front-end) con mezcla y recubrimiento, la etapa de ensamblaje de celdas (etapa intermedia) con bobinado e inyección de electrolitos, y la etapa de empaquetado y prueba (back-end) con formación y sellado. La distribución del valor (en términos de monto de adquisición) es de aproximadamente 35-40% para el front-end, 30-35% para la etapa intermedia y 30-35% para el back-end. Según la información de los proveedores de equipos de recubrimiento, las variaciones se deben principalmente a los diferentes proveedores de equipos y a la proporción entre el equipo importado y el equipo producido en el país. Sin embargo, el proceso general se mantiene relativamente consistente, con ligeras desviaciones en la distribución del valor, pero en general se alinea con las proporciones mencionadas.
Los equipos de producción de baterías de litio correspondientes a los procesos front-end incluyen principalmente mezcladores de vacío,Máquinas de recubrimientoyMáquinas de calandrado. Para los procesos de etapa intermedia, el equipo incluye máquinas troqueladoras, máquinas bobinadoras, máquinas apiladoras y máquinas de inyección de electrolitos. Los procesos de back-end involucran máquinas de formación, equipos de prueba de capacidad y automatización de procesos de almacenamiento y logística. Además, la producción de paquetes de baterías requiere equipos de automatización de paquetes.
El resultado del proceso inicial en la producción de baterías de litio es la preparación de las láminas de electrodos positivo y negativo. El primer paso en este proceso es la mezcla, donde los materiales de la batería de estado sólido para los electrodos positivo y negativo se mezclan uniformemente y luego se mezclan con un solvente para formar una suspensión. La mezcla de los ingredientes es la base de los procesos posteriores en la producción de baterías de litio. La mezcla de alta calidad es esencial para lograr resultados de alta calidad en los siguientes procesos de recubrimiento y calandrado.
Después de los procesos de recubrimiento y calandrado, el siguiente paso es el corte, que consiste en cortar el material recubierto en los anchos deseados. Si hay rebabas o bordes ásperos durante el proceso de corte, puede provocar problemas de montaje, problemas de inyección de electrolitos e inclusoRiesgos de seguridaddurante el uso de la batería. Por lo tanto, el equipo frontal en el proceso de producción de baterías de litio, como mezcladores, máquinas de recubrimiento, máquinas de calandrado ymáquinas de corte longitudinal, son las máquinas principales para la fabricación de baterías. Tienen un gran impacto en la calidad de toda la línea de producción. Como resultado, el equipo front-end tiene el valor más alto (en términos de cantidad) en la línea de producción automatizada de baterías de litio en general, lo que representa aproximadamente el 35%.
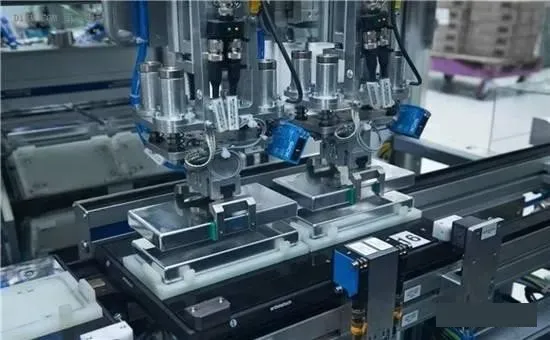
En el proceso de fabricación de baterías de litio, los procesos de etapa intermedia se centran principalmente en la formación de baterías. Los procesos principales en esta etapa incluyen la preparación de electrodos, el bobinado de electrodos, el troquelado, el bobinado de celdas y el apilamiento. Esta etapa es un área ferozmente competitiva entre los fabricantes de equipos nacionales y representa aproximadamente el 30% del valor de una línea de producción de baterías de litio.
Actualmente, los procesos de fabricación de celdas de batería de litio de potencia incluyen principalmente el bobinado y el apilamiento, correspondientes a tres formas estructurales de batería: cilíndrica, prismática y de bolsa. Las baterías cilíndricas y prismáticas se producen principalmente mediante el proceso de bobinado, mientras que las baterías de bolsa utilizan principalmente el proceso de apilamiento. Las baterías cilíndricas están representadas por formatos como 18650 y 26650 (Tesla ha desarrollado de forma independiente la batería 21700, que está siendo ampliamente promocionada en toda la industria). La principal diferencia entre las baterías prismáticas y las de bolsa radica en la carcasa, ya que las baterías prismáticas utilizan carcasas de aluminio duro y las baterías de bolsa que utilizan una película de aluminio y plástico. El proceso de fabricación de las baterías de bolsa es principalmente de apilamiento, mientras que de las baterías de aluminio, es principalmente de bobinado.
Según el entendimiento, la estructura de bolsa de las baterías de litio se dirige principalmente al mercado digital de gama media a alta, con márgenes de beneficio relativamente más altos por producto unitario. En condiciones de capacidad de producción equivalente, el margen de beneficio de las baterías de bolsa es generalmente mayor que el de las baterías de aluminio. Sin embargo, debido a la facilidad de lograr economías de escala y controlar las tasas y costos de calificación del producto, las baterías de carcasa de aluminio también tienen ganancias significativas en sus respectivos dominios de mercado. Es previsible que tanto las baterías de bolsa como las de aluminio se reemplacen por completo en un futuro próximo.
Debido a la capacidad de lograr una producción de alta velocidad a través de la velocidad de rotación, el proceso de bobinado es actualmente el método principal utilizado en la producción de baterías de litio de energía doméstica. Por otro lado, la mejora de la velocidad que se puede lograr con la tecnología de apilamiento es limitada. Como resultado, el volumen de envío de las máquinas bobinadoras es actualmente mayor que el de las máquinas apiladoras. Los procesos anteriores para la producción de bobinado y apilamiento son la preparación de electrodos y el troquelado. La preparación de electrodos incluye procesos como la soldadura de los electrodos/lengüetas cortados, la eliminación del polvo de los electrodos, la aplicación de cinta adhesiva protectora, el encapsulado de las lengüetas y el bobinado o corte a una longitud fija. Los electrodos bobinados se utilizan para el bobinado posterior totalmente automatizado, mientras que los electrodos cortados a medida se utilizan para el bobinado semiautomático. El troquelado consiste en cortar y dar forma a los electrodos bobinados para los procesos de apilamiento posteriores.
En términos de soldadura de encapsulación de baterías de litio, los principales fabricantes de aplicaciones integradas, como Uwlaser, Hanslaser y Gdlaser, están involucrados en el campo de la tecnología láser. Son capaces de satisfacer la demanda sin necesidad de importaciones.
Flujo de proceso de back-end de batería de litio: la separación y formación de volumen es el enlace central
Los procesos de postproducción en litioFabricación de bateríasincluyen principalmente la clasificación, la formación, las pruebas y el embalaje para el almacenamiento, que representan aproximadamente el 35% del valor en la línea de producción. La formación y la clasificación son los procesos clave en la etapa de postproducción, que implica las pruebas de activación de las baterías formadas. Debido al largo ciclo de prueba para la carga y descarga de la batería, el equipo utilizado en estos procesos tiene el valor más alto. El objetivo principal del proceso de formación es activar las celdas selladas después del empaquetado de inyección cargándolas, mientras que el proceso de clasificación implica probar la capacidad de la batería y otros parámetros de rendimiento eléctrico después de la activación, y luego clasificarlos en consecuencia. La formación y la clasificación se realizan normalmente mediante sistemas automatizados que constan de máquinas formadoras y máquinas clasificadoras.
Proceso del paquete de baterías de litio: aparentemente simple, pero debe combinarse con un diseño sistemático
Un sistema de paquete de baterías de potencia se compone de múltiples celdas de batería individuales conectadas en serie o en paralelo, integrando sistemas de gestión de energía y térmica. El paquete es un componente clave en la producción, el diseño y la aplicación de sistemas de baterías de potencia. Sirve como enlace entre la producción de celdas de batería aguas arriba y las aplicaciones posteriores de vehículos. Por lo general, los requisitos de diseño son propuestos por los fabricantes de celdas de batería o las empresas automotrices y, por lo general, los completan los fabricantes de baterías, las empresas automotrices o los fabricantes de paquetes de terceros.
La línea de producción de paquetes de baterías de litio es relativamente simple, con procesos centrales que incluyen carga de material, ensamblaje de soportes, soldadura y pruebas. El equipo principal incluye máquinas de soldadura láser y varios tipos de adhesivos y equipos de prueba. Actualmente, el nivel de automatización en la producción de envases es relativamente bajo. Esto se debe principalmente a que el volumen de ventas de modelos individuales de vehículos de nueva energía no es lo suficientemente grande como para justificar el alto costo de las líneas de producción automatizadas.
Fosfato de hierro y litio y ternario: la densidad de energía es un tema inevitable, diferentes materiales requieren un conjunto completo de inversión en equipos
Actualmente, los principales materiales catódicos para alimentar baterías de litio en China se dividen en dos categorías: fosfato de hierro y litio (LiFePO4) y materiales ternarios. Entre ellos, el fosfato de hierro y litio es el material catódico más seguro para las baterías de iones de litio, con una vida útil típica de más de 2000 ciclos. Además, debido a la madurez de la industria y a la disminución de los precios y las barreras tecnológicas, muchos fabricantes eligen las baterías de fosfato de hierro y litio por diversas razones. Sin embargo, las baterías de fosfato de hierro y litio tienen una desventaja notable en términos de densidad de energía. El principal fabricante de baterías de fosfato de hierro y litio, BYD, tiene una densidad de energía de 150 Wh para sus celdas de fosfato de hierro y litio, y esperaban aumentarla a 160 Wh para finales de 2017. Teóricamente, es difícil que el fosfato de hierro y litio supere una densidad energética de 200 Wh/kg.
Las baterías de litio de polímero ternario se refieren a las baterías de litio que utilizan un material catódico compuesto de óxido de manganeso, litio, níquel, cobalto, manganeso, con la proporción real de níquel, cobalto y manganeso ajustada según las necesidades específicas. Las baterías ternarias de litio tienen una mayor densidad de energía (actualmente, los fabricantes de baterías de potencia de primera clase como CATL pueden alcanzar una densidad de energía de 200Wh/kg-220Wh/kg, y se prevé que para 2020, la densidad energética de las baterías ternarias alcance los 300Wh/kg). Como resultado, el mercado de vehículos de pasajeros está cambiando hacia las baterías de litio ternarias. Por otro lado, el fosfato de hierro y litio es más favorecido para aplicaciones con mayores requisitos de seguridad, como en autobuses. Con el desarrollo de vehículos de pasajeros totalmente eléctricos, las baterías ternarias de litio ocupan cada vez más un lugar importante.
Los dos materiales tienen diferencias en la densidad de energía y el costo, y los diferentes vehículos y fabricantes de automóviles toman diferentes decisiones. Según Tucbol, el proceso de producción de ambos materiales es generalmente similar, pero las diferencias radican principalmente en el uso y la proporción de materiales, así como en variaciones significativas en parámetros específicos del proceso. El equipo no se puede compartir para la producción, y el costo de simplemente adaptar o cambiar la capacidad de producción es alto (los materiales ternarios tienen requisitos estrictos para la deshumidificación al vacío, que no eran necesarios para las líneas de producción anteriores de fosfato de hierro y litio). Por lo tanto, muchos fabricantes de baterías planifican el diseño de su capacidad de producción mediante la implementación simultánea y la compra por separado de equipos para ambos materiales.