Mixing (positive and negative electrode active materials + conductive agent + binder + dispersant) – coating —– rolling ——- cutting — tab welding — – Winding (or gasket) – Adhesive paper – Inserting the battery shell – Welding – Sealing – Formation, etc. Basically the battery production process in the entire industry is similar, the main difference is the difference in equipment or battery products are different. In the case of pouch cells, they are typically stacked, while cylindrical cells are wound, and prismatic cells can involve both winding and stacking. This results in different processes during the cell winding stage. The most important and core technologies lie in the mixing and coating processes, as well as the final formation process.
The production process of lithium batteries is complex and primarily involves three main stages: the electrode fabrication stage (front-end) with mixing and coating, the cell assembly stage (middle stage) with winding and electrolyte injection, and the packaging and testing stage (back-end) with formation and sealing. The value distribution (in terms of procurement amount) is approximately 35-40% for the front-end, 30-35% for the middle stage, and 30-35% for the back-end. According to information from coating equipment suppliers, the variations primarily stem from different equipment suppliers and the ratio of imported to domestically produced equipment. However, the overall process remains relatively consistent, with slight deviations in the value distribution but generally aligning with the mentioned proportions.
The lithium battery production equipment corresponding to the front-end processes mainly include vacuum mixers, coating machines, and calendering machines. For the middle-stage processes, the equipment includes die-cutting machines, winding machines, stacking machines, and electrolyte injection machines. The back-end processes involve formation machines, capacity testing equipment, and process warehousing and logistics automation. Additionally, the production of battery packs requires Pack automation equipment.
The result of the front-end process in lithium battery production is the preparation of the positive and negative electrode sheets. The first step in this process is mixing, where the solid-state battery materials for the positive and negative electrodes are blended uniformly and then mixed with a solvent to form a slurry. Mixing the ingredients is the foundation of subsequent processes in lithium battery production. High-quality mixing is essential for achieving high-quality results in the following coating and calendering processes.
After the coating and calendering processes, the next step is slitting, which involves cutting the coated material into desired widths. If burrs or rough edges are present during the slitting process, it can lead to assembly issues, electrolyte injection problems, and even safety hazards during battery usage. Therefore, the front-end equipment in the lithium battery production process, such as mixers, coating machines, calendering machines, and slitting machines, are the core machines for battery manufacturing. They greatly impact the quality of the entire production line. As a result, the front-end equipment holds the highest value (in terms of amount) in the overall lithium battery automated production line, accounting for approximately 35%.
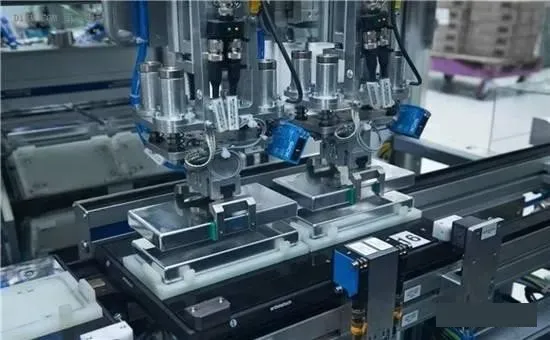
In the manufacturing process of lithium batteries, the middle-stage processes are primarily focused on battery formation. The main processes in this stage include electrode preparation, electrode winding, die-cutting, cell winding, and stacking. This stage is a fiercely competitive area among domestic equipment manufacturers and accounts for approximately 30% of the value in a lithium battery production line.
Currently, the manufacturing processes for power lithium battery cells mainly include winding and stacking, corresponding to three battery structural forms: cylindrical, prismatic, and pouch. Cylindrical and prismatic batteries are primarily produced using the winding process, while pouch batteries mainly utilize the stacking process. The cylindrical batteries are represented by formats such as 18650 and 26650 (Tesla has independently developed the 21700 battery, which is being widely promoted across the industry). The main difference between prismatic and pouch batteries lies in the casing, with prismatic batteries using hard aluminum shells and pouch batteries utilizing aluminum-plastic film. The manufacturing process for pouch batteries is primarily stacking, while for aluminum-shell batteries, it is primarily winding.
According to the understanding, the pouch structure of lithium batteries primarily targets the mid-to-high-end digital market, with relatively higher profit margins per unit product. Under equivalent production capacity conditions, the profit margin for pouch batteries is generally higher than that of aluminum-shell batteries. However, due to the ease of achieving economies of scale and controlling product qualification rates and costs, aluminum-shell batteries also have significant profits in their respective market domains. It is foreseeable that both pouch and aluminum-shell batteries are unlikely to be completely replaced in the foreseeable future.
Due to the ability to achieve high-speed production through rotational speed, the winding process is currently the primary method used in domestic power lithium battery production. On the other hand, the speed improvement achievable with stacking technology is limited. As a result, the shipment volume of winding machines is currently higher than that of stacking machines. The preceding processes for winding and stacking production are electrode preparation and die-cutting. Electrode preparation includes processes such as welding the cut electrodes/tab, electrode dust removal, applying protective adhesive tape, encapsulating the tabs, and winding or cutting to a fixed length. Wound electrodes are used for subsequent fully automated winding, while cut-to-length electrodes are used for semi-automatic winding. Die-cutting involves cutting and shaping the wound electrodes for subsequent stacking processes.
In terms of lithium battery encapsulation welding, mainstream integrated application manufacturers such as Uwlaser, Hanslaser, and Gdlaser are all involved in the field of laser technology. They are capable of meeting the demand without the need for imports.
Lithium battery back-end process flow: volume separation and formation is the core link
The post-production processes in lithium battery manufacturing mainly include sorting, formation, testing, and packaging for storage, which account for approximately 35% of the value in the production line. Formation and sorting are the key processes in the post-production stage, involving the activation testing of formed batteries. Due to the long testing cycle for battery charge and discharge, the equipment used in these processes holds the highest value. The main purpose of the formation process is to activate the sealed cells after injection packaging by charging them, while the sorting process involves testing the battery capacity and other electrical performance parameters after activation, and then grading them accordingly. Formation and sorting are typically performed by automated systems consisting of formation machines and sorting machines.
Lithium battery Pack process: seemingly simple but needs to be combined with systematic design
A power battery pack system is composed of multiple individual battery cells connected in series or parallel, integrating power and thermal management systems. The pack is a key component in the production, design, and application of power battery systems. It serves as the link between upstream battery cell production and downstream vehicle applications. Typically, the design requirements are proposed by battery cell manufacturers or automotive companies and are usually completed by battery manufacturers, automotive companies, or third-party pack manufacturers.
The lithium battery pack production line is relatively simple, with core processes including material loading, bracket assembly, welding, and testing. The core equipment includes laser welding machines and various types of adhesive and testing equipment. Currently, the level of automation in pack production is relatively low. This is mainly because the sales volume of individual models of new energy vehicles is not large enough to justify the high cost of automated production lines.
Lithium iron phosphate and ternary: energy density is an unavoidable topic, different materials require a full set of equipment investment
Currently, the mainstream cathode materials for power lithium batteries in China are divided into two categories: lithium iron phosphate (LiFePO4) and ternary materials. Among them, lithium iron phosphate is the safest cathode material for lithium-ion batteries, with a typical cycle life of over 2000 cycles. Furthermore, due to the mature industry and the decrease in prices and technological barriers, many manufacturers choose lithium iron phosphate batteries for various reasons. However, lithium iron phosphate batteries have a noticeable disadvantage in terms of energy density. The leading lithium iron phosphate battery manufacturer, BYD, has a energy density of 150Wh for its lithium iron phosphate cells, and they expected to increase it to 160Wh by the end of 2017. Theoretically, it is difficult for lithium iron phosphate to exceed an energy density of 200Wh/kg.
Ternary polymer lithium batteries refer to lithium batteries that use a cathode material composed of lithium nickel cobalt manganese oxide, with the actual proportion of nickel, cobalt, and manganese adjusted according to specific needs. Ternary lithium batteries have higher energy density (currently, first-class power battery manufacturers like CATL can achieve an energy density of 200Wh/kg-220Wh/kg, and it is projected that by 2020, the energy density of ternary batteries will reach 300Wh/kg). As a result, the passenger vehicle market is shifting towards ternary lithium batteries. On the other hand, lithium iron phosphate is more favored for applications with higher safety requirements, such as in buses. With the development of fully electric passenger vehicles, ternary lithium batteries are increasingly occupying an important position.
The two materials have differences in energy density and cost, and different vehicles and automakers make different choices. According to Tucbol’s understanding, the production process for both materials is generally similar, but the differences mainly lie in the use and proportion of materials, as well as significant variations in specific process parameters. The equipment cannot be shared for production, and the cost of simply retrofitting or switching production capacity is high (ternary materials have strict requirements for vacuum dehumidification, which were not necessary for previous lithium iron phosphate production lines). Therefore, many battery manufacturers plan their production capacity layout by simultaneously deploying and separately purchasing equipment for both materials.