混合(正極と負極の活物質+導電剤+バインダー+分散剤)–コーティング—–圧延——-切断—タブ溶接—–巻線(またはガスケット)–粘着紙–バッテリーシェルの挿入–溶接–シーリング–形成など。基本的に、業界全体のバッテリー製造プロセスは似ていますが、主な違いは、機器の違いやバッテリー製品が異なることです。ポーチセルの場合、通常は積み重ねられますが、円筒形のセルは巻き取られ、角型セルには巻き取りと積み重ねの両方が含まれる場合があります。これにより、セルの巻き取り段階でさまざまなプロセスが発生します。最も重要なコアテクノロジーは、ミキシングとコーティングのプロセス、および最終的な形成プロセスにあります。
リチウム電池の製造プロセスは複雑で、主に3つの主要な段階が含まれます:混合とコーティングを行う電極製造段階(フロントエンド)、巻線と電解液注入を行うセル組み立て段階(中間段階)、および形成とシーリングを伴うパッケージングとテスト段階(バックエンド)。価値分布(調達量の観点から)は、フロントエンドが約35〜40%、中期が30〜35%、バックエンドが30〜35%です。コーティング装置サプライヤーからの情報によると、変動は主にさまざまな機器サプライヤーと、輸入機器と国内生産機器の比率に起因します。ただし、全体的なプロセスは比較的一貫しており、値の分布にはわずかな偏差がありますが、一般的には前述の比率と一致しています。
フロントエンドプロセスに対応するリチウム電池製造装置には、主に真空ミキサー、コーティング機そしてカレンダー加工機.中期工程では、ダイカット機、巻線機、スタッキング機、電解液注入機などの設備を取り揃えています。バックエンドプロセスには、フォーメーションマシン、容量試験装置、プロセス倉庫保管およびロジスティクスの自動化が含まれます。さらに、バッテリーパックの製造には、パック自動化装置が必要です。
リチウム電池製造のフロントエンドプロセスの結果は、正極シートと負極シートの準備です。このプロセスの最初のステップは、正極と負極の固体電池材料を均一にブレンドし、溶媒と混合してスラリーを形成する混合です。成分の混合は、リチウム電池製造の後続のプロセスの基礎です。高品質なミキシングは、以下のコーティング・カレンダー加工工程で高品質な結果を得るために不可欠です。
コーティングとカレンダー加工のプロセスの後、次のステップはスリット加工で、コーティングされた材料を希望の幅にカットします。スリット加工中にバリや粗いエッジがあると、組み立ての問題や電解液注入の問題、さらには安全上の問題バッテリー使用中。したがって、ミキサー、コーティング機、カレンダー機などのリチウム電池製造プロセスのフロントエンド機器、およびスリッターは、バッテリー製造の基幹マシンです。それらは生産ライン全体の品質に大きく影響します。その結果、フロントエンド機器は、リチウム電池自動化生産ライン全体で最も高い値(量)を保持し、約35%を占めています。
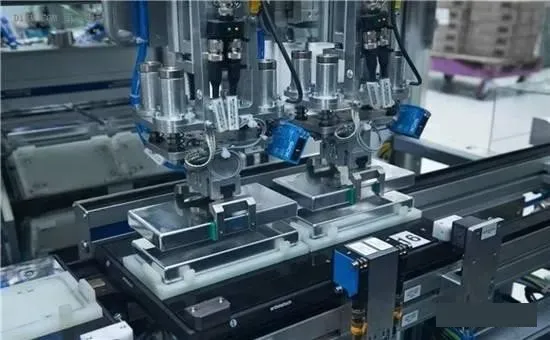
リチウム電池の製造工程では、中期工程は主に電池形成に焦点を当てています。この段階の主なプロセスには、電極の準備、電極の巻線、型抜き、セルの巻線、およびスタッキングが含まれます。この段階は、国内の機器メーカー間で激しい競争が繰り広げられている分野であり、リチウム電池の生産ラインの価値の約30%を占めています。
現在、パワーリチウム電池セルの製造プロセスには、主に巻線とスタッキングが含まれ、円筒形、角柱状、ポーチの3つの電池構造形式に対応しています。円筒形および角形の電池は主に巻線プロセスを使用して製造されますが、パウチ電池は主にスタッキングプロセスを利用します。円筒形バッテリーは、18650や26650などの形式で表されます(テスラは21700バッテリーを独自に開発し、業界全体で広く宣伝されています)。プリズム電池とパウチ電池の主な違いはケーシングにあり、角型電池は硬質アルミニウムシェルを使用し、パウチ電池はアルミニウムプラスチックフィルムを使用しています。パウチ電池の製造工程はスタッキングが中心ですが、アルミシェル電池は巻き取りがメインです。
理解によれば、リチウム電池のパウチ構造は主にミッドエンドからハイエンドのデジタル市場を対象としており、単位製品あたりの利益率は比較的高くなっています。同等の生産能力条件下では、パウチ電池の利益率は一般にアルミシェル電池の利益率よりも高くなります。ただし、規模の経済を達成し、製品の認定率とコストを管理することが容易であるため、アルミニウムシェル電池は、それぞれの市場領域でも大きな利益を上げています。ポーチ電池とアルミシェル電池の両方が近い将来に完全に交換される可能性は低いと予想されます。
回転速度で高速生産を実現できるため、巻線プロセスは現在、国内のパワーリチウム電池製造で使用される主要な方法です。一方、スタッキング技術で達成できる速度向上は限られています。その結果、現在、巻線機の出荷量はスタッキングマシンよりも多くなっています。巻線とスタッキングの生産に先行するプロセスは、電極の準備と型抜きです。電極の作製には、切断した電極・タブの溶接、電極の粉塵除去、保護用粘着テープの貼付、タブの封入、固定長への巻き取りや切断などの工程があります。巻線電極はその後の全自動巻線に使用され、半自動巻線にはカット・トゥ・レングス電極が使用されます。ダイカットでは、その後のスタッキングプロセスのために、創傷電極を切断して成形します。
リチウム電池のカプセル化溶接に関しては、Uwlaser、Hanslaser、Gdlaserなどの主流の統合アプリケーションメーカーがすべてレーザー技術の分野に関与しています。彼らは輸入を必要とせずに需要を満たすことができます。
リチウム電池のバックエンドプロセスフロー:ボリュームの分離と形成がコアリンクです
リチウムのポストプロダクションプロセスバッテリー製造主に、生産ラインの価値の約35%を占める、保管用の選別、形成、テスト、およびパッケージングが含まれます。形成と選別は、形成されたバッテリーの活性化テストを含むポストプロダクション段階の主要なプロセスです。バッテリーの充電と放電のテストサイクルが長いため、これらのプロセスで使用される機器は最高の価値を保持しています。形成プロセスの主な目的は、注入包装後に密封されたセルを充電して活性化することですが、選別プロセスには、活性化後のバッテリー容量やその他の電気的性能パラメータをテストし、それに応じて等級付けすることが含まれます。形成と選別は通常、形成機と選別機で構成される自動化システムによって実行されます。
リチウム電池パックのプロセス:一見シンプルですが、体系的な設計と組み合わせる必要があります
パワーバッテリーパックシステムは、直列または並列に接続された複数の個別のバッテリーセルで構成され、電力管理システムと熱管理システムを統合しています。このパックは、パワーバッテリーシステムの製造、設計、およびアプリケーションにおける重要なコンポーネントです。これは、アップストリームのバッテリーセル生産とダウンストリームの車両アプリケーションとの間のリンクとして機能します。通常、設計要件はバッテリーセルメーカーまたは自動車会社によって提案され、通常はバッテリーメーカー、自動車会社、またはサードパーティのパックメーカーによって完成されます。
リチウム電池パックの生産ラインは比較的シンプルで、材料の積み込み、ブラケットの組み立て、溶接、テストなどのコアプロセスがあります。コア機器には、レーザー溶接機と各種接着剤および試験装置が含まれます。現在、パック生産の自動化レベルは比較的低いです。これは主に、新エネルギー車の個々のモデルの販売台数が、自動化された生産ラインの高コストを正当化するほど大きくないためです。
リン酸鉄リチウムと三元系:エネルギー密度は避けられないトピックであり、さまざまな材料にはフルセットの機器投資が必要です
現在、中国のパワーリチウム電池の主流のカソード材料は、リン酸鉄リチウム(LiFePO4)と三元材料の2つのカテゴリに分類されています。その中で、リン酸鉄リチウムはリチウムイオン電池の最も安全な正極材料であり、典型的なサイクル寿命は2000サイクルを超えています。さらに、業界の成熟と価格の低下、および技術的な障壁により、多くのメーカーはさまざまな理由でリン酸鉄リチウム電池を選択しています。ただし、リン酸鉄リチウム電池には、エネルギー密度の点で顕著な欠点があります。大手リン酸鉄リチウム電池メーカーであるBYDは、リン酸鉄リチウム電池のエネルギー密度が150Whで、2017年末までに160Whに増やすと予想しています。理論的には、リン酸鉄リチウムが200Wh / kgのエネルギー密度を超えることは困難です。
三元ポリマーリチウム電池とは、リチウムニッケル、コバルト、マンガン酸化物で構成されるカソード材料を使用するリチウム電池を指し、ニッケル、コバルト、およびマンガンの実際の比率は特定のニーズに応じて調整されます。三元リチウム電池はエネルギー密度が高くなります(現在、CATLのような一流のパワー電池メーカーは200Wh / kg-220Wh / kgのエネルギー密度を達成でき、2020年までに三元電池のエネルギー密度は300Wh / kgに達すると予測されています)。その結果、乗用車市場は三元リチウム電池にシフトしています。一方、リン酸鉄リチウムは、バスなど、より高い安全要件を持つアプリケーションに適しています。完全電動乗用車の開発に伴い、三元リチウム電池はますます重要な位置を占めています。
2つの材料はエネルギー密度とコストに違いがあり、車両や自動車メーカーが異なれば選択も異なります。Tucbolの理解によれば、両方の材料の製造プロセスは一般的に似ていますが、違いは主に材料の使用と比率、および特定のプロセスパラメータの大きな変動にあります。機器を生産用に共有することはできず、生産能力を単に改造または切り替えるコストは高くなります(三元材料には真空除湿の厳しい要件があり、これは以前のリン酸鉄リチウム生産ラインには必要ありませんでした)。したがって、多くのバッテリーメーカーは、両方の材料の機器を同時に展開し、個別に購入することにより、生産能力のレイアウトを計画しています。