Mélange (électrode positive et négative matériaux actifs + agent conducteur + liant + dispersant) – revêtement —– laminage ——- découpe — soudage à languette — – Enroulement (ou joint) – Papier adhésif – Insertion de la coque de la batterie – Soudure – Etanchéité – Formation, etc. Fondamentalement, le processus de production de batteries dans l’ensemble de l’industrie est similaire, la principale différence est que la différence entre les équipements et les produits de batterie sont différents. Dans le cas des cellules de poche, elles sont généralement empilées, tandis que les cellules cylindriques sont enroulées, et les cellules prismatiques peuvent impliquer à la fois l’enroulement et l’empilement. Il en résulte différents processus au cours de l’étape d’enroulement des cellules. Les technologies les plus importantes et les plus fondamentales résident dans les processus de mélange et de revêtement, ainsi que dans le processus de formation finale.
Le processus de production des batteries au lithium est complexe et comprend principalement trois étapes principales : l’étape de fabrication de l’électrode (front-end) avec mélange et revêtement, l’étape d’assemblage des cellules (étape intermédiaire) avec enroulement et injection d’électrolyte, et l’étape d’emballage et de test (back-end) avec formation et étanchéité. La distribution de la valeur (en termes de montant d’approvisionnement) est d’environ 35 à 40 % pour l’avant-train, 30 à 35 % pour l’étage intermédiaire et 30 à 35 % pour l’aval. Selon les informations fournies par les fournisseurs d’équipements de revêtement, les variations proviennent principalement de différents fournisseurs d’équipements et du rapport entre les équipements importés et les équipements produits dans le pays. Cependant, le processus global reste relativement cohérent, avec de légers écarts dans la distribution de la valeur, mais s’alignant généralement sur les proportions mentionnées.
Les équipements de production de batteries au lithium correspondant aux processus front-end comprennent principalement des mélangeurs sous vide,machines d’enductionetMachines à calandrer. Pour les processus intermédiaires, l’équipement comprend des machines de découpe à l’emporte-pièce, des bobineuses, des machines d’empilage et des machines d’injection d’électrolyte. Les processus back-end impliquent des machines de formation, des équipements de test de capacité, ainsi que l’entreposage des processus et l’automatisation de la logistique. De plus, la production de batteries nécessite un équipement d’automatisation Pack.
Le résultat du processus frontal dans la production de batteries au lithium est la préparation des feuilles d’électrodes positives et négatives. La première étape de ce processus est le mélange, où les matériaux de la batterie à l’état solide pour les électrodes positive et négative sont mélangés uniformément, puis mélangés à un solvant pour former une boue. Le mélange des ingrédients est à la base des processus ultérieurs de production de batteries au lithium. Un mélange de haute qualité est essentiel pour obtenir des résultats de haute qualité dans les processus d’enrobage et de calandrage suivants.
Après les processus de revêtement et de calandrage, l’étape suivante est le refendage, qui consiste à couper le matériau revêtu dans les largeurs souhaitées. Si des bavures ou des bords rugueux sont présents pendant le processus de refendage, cela peut entraîner des problèmes d’assemblage, des problèmes d’injection d’électrolyte et mêmeRisques pour la sécuritépendant l’utilisation de la batterie. Par conséquent, les équipements frontaux du processus de production de batteries au lithium, tels que les mélangeurs, les machines d’enrobage, les machines de calandrage, etMachines à refendre, sont les machines de base pour la fabrication de batteries. Ils ont un impact considérable sur la qualité de l’ensemble de la chaîne de production. En conséquence, l’équipement frontal détient la valeur la plus élevée (en termes de quantité) dans l’ensemble de la chaîne de production automatisée de batteries au lithium, représentant environ 35 %.
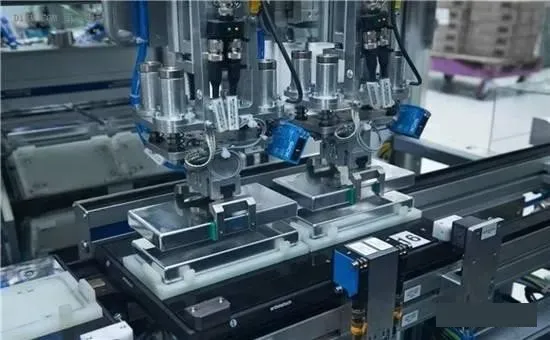
Dans le processus de fabrication des batteries au lithium, les processus intermédiaires sont principalement axés sur la formation des batteries. Les principaux processus de cette étape comprennent la préparation des électrodes, l’enroulement des électrodes, la découpe, l’enroulement des cellules et l’empilage. Cette étape est un domaine très concurrentiel entre les fabricants d’équipements nationaux et représente environ 30 % de la valeur d’une ligne de production de batteries au lithium.
Actuellement, les processus de fabrication des cellules de batterie au lithium de puissance comprennent principalement l’enroulement et l’empilement, correspondant à trois formes structurelles de batterie : cylindrique, prismatique et en poche. Les batteries cylindriques et prismatiques sont principalement produites à l’aide du processus d’enroulement, tandis que les batteries à poche utilisent principalement le processus d’empilage. Les batteries cylindriques sont représentées par des formats tels que 18650 et 26650 (Tesla a développé indépendamment la batterie 21700, qui fait l’objet d’une large promotion dans l’industrie). La principale différence entre les batteries prismatiques et les batteries de poche réside dans le boîtier, les batteries prismatiques utilisant des coques en aluminium dur et les batteries de poche utilisant un film aluminium-plastique. Le processus de fabrication des batteries à poche est principalement l’empilement, tandis que pour les batteries à coque d’aluminium, il s’agit principalement de l’enroulement.
Selon l’accord, la structure en poche des batteries au lithium cible principalement le marché numérique de milieu à haut de gamme, avec des marges bénéficiaires par produit unitaire relativement plus élevées. À capacité de production équivalente, la marge bénéficiaire des batteries à poche est généralement supérieure à celle des batteries à coque d’aluminium. Cependant, en raison de la facilité avec laquelle il est possible de réaliser des économies d’échelle et de contrôler les taux et les coûts de qualification des produits, les batteries à coque d’aluminium ont également des bénéfices importants dans leurs domaines de marché respectifs. Il est prévisible qu’il est peu probable que les batteries à poche et à coque en aluminium soient complètement remplacées dans un avenir prévisible.
En raison de la capacité d’obtenir une production à grande vitesse grâce à la vitesse de rotation, le processus d’enroulement est actuellement la principale méthode utilisée dans la production de batteries au lithium domestiques. D’autre part, l’amélioration de la vitesse réalisable avec la technologie d’empilage est limitée. En conséquence, le volume d’expédition des bobineuses est actuellement supérieur à celui des machines d’empilage. Les procédés précédents pour la production d’enroulement et d’empilage sont la préparation des électrodes et la découpe à l’emporte-pièce. La préparation des électrodes comprend des processus tels que le soudage des électrodes/languettes coupées, le dépoussiérage des électrodes, l’application de ruban adhésif protecteur, l’encapsulation des languettes et l’enroulement ou la coupe à une longueur fixe. Les électrodes bobinées sont utilisées pour le bobinage ultérieur entièrement automatisé, tandis que les électrodes coupées à longueur sont utilisées pour le bobinage semi-automatique. La découpe consiste à couper et à façonner les électrodes enroulées pour les processus d’empilage ultérieurs.
En ce qui concerne le soudage par encapsulation de batteries au lithium, les principaux fabricants d’applications intégrées tels que Uwlaser, Hanslaser et Gdlaser sont tous impliqués dans le domaine de la technologie laser. Ils sont capables de répondre à la demande sans avoir besoin d’importations.
Flux de processus back-end de la batterie au lithium : la séparation et la formation du volume sont le maillon central
Les processus de post-production dans le lithiumFabrication de batteriescomprennent principalement le tri, la formation, les tests et l’emballage pour le stockage, qui représentent environ 35 % de la valeur de la chaîne de production. La formation et le tri sont les processus clés de la phase de post-production, impliquant les tests d’activation des batteries formées. En raison du long cycle de test pour la charge et la décharge de la batterie, l’équipement utilisé dans ces processus a la valeur la plus élevée. L’objectif principal du processus de formation est d’activer les cellules scellées après l’emballage par injection en les chargeant, tandis que le processus de tri consiste à tester la capacité de la batterie et d’autres paramètres de performance électrique après l’activation, puis à les classer en conséquence. La formation et le tri sont généralement effectués par des systèmes automatisés composés de machines de formation et de machines de tri.
Procédé de batterie au lithium : apparemment simple mais qui doit être combiné à une conception systématique
Un système de batterie d’alimentation est composé de plusieurs cellules de batterie individuelles connectées en série ou en parallèle, intégrant des systèmes de gestion de l’alimentation et thermiques. Le pack est un composant clé dans la production, la conception et l’application des systèmes de batteries de puissance. Il sert de lien entre la production de cellules de batterie en amont et les applications de véhicules en aval. En règle générale, les exigences de conception sont proposées par les fabricants de cellules de batterie ou les entreprises automobiles et sont généralement remplies par les fabricants de batteries, les entreprises automobiles ou les fabricants de packs tiers.
La ligne de production de batteries au lithium est relativement simple, avec des processus de base comprenant le chargement des matériaux, l’assemblage des supports, le soudage et les tests. L’équipement de base comprend des machines de soudage laser et divers types d’adhésifs et d’équipements de test. Actuellement, le niveau d’automatisation de la production d’emballages est relativement faible. Cela s’explique principalement par le fait que le volume des ventes de modèles individuels de véhicules à énergie nouvelle n’est pas assez important pour justifier le coût élevé des lignes de production automatisées.
Lithium fer phosphate et ternaire : la densité d’énergie est un sujet incontournable, différents matériaux nécessitent un ensemble complet d’investissements en équipement
Actuellement, les principaux matériaux de cathode pour les batteries au lithium de puissance en Chine sont divisés en deux catégories : le phosphate de fer lithium (LiFePO4) et les matériaux ternaires. Parmi eux, le phosphate de fer lithium est le matériau de cathode le plus sûr pour les batteries lithium-ion, avec une durée de vie typique de plus de 2000 cycles. De plus, en raison de la maturité de l’industrie et de la baisse des prix et des barrières technologiques, de nombreux fabricants choisissent les batteries au lithium fer phosphate pour diverses raisons. Cependant, les batteries au lithium fer phosphate présentent un inconvénient notable en termes de densité énergétique. Le principal fabricant de batteries au lithium fer phosphate, BYD, a une densité d’énergie de 150 Wh pour ses cellules au lithium fer phosphate, et ils prévoyaient de l’augmenter à 160 Wh d’ici la fin de 2017. Théoriquement, il est difficile pour le phosphate de fer lithium de dépasser une densité d’énergie de 200Wh/kg.
Les batteries au lithium polymère ternaires font référence aux batteries au lithium qui utilisent un matériau cathodique composé de lithium, de nickel, de cobalt et d’oxyde de manganèse, la proportion réelle de nickel, de cobalt et de manganèse étant ajustée en fonction des besoins spécifiques. Les batteries au lithium ternaires ont une densité d’énergie plus élevée (actuellement, les fabricants de batteries de puissance de premier ordre comme CATL peuvent atteindre une densité d’énergie de 200 Wh/kg-220 Wh/kg, et il est prévu que d’ici 2020, la densité énergétique des batteries ternaires atteindra 300 Wh/kg). En conséquence, le marché des véhicules de tourisme évolue vers les batteries au lithium ternaires. D’autre part, le phosphate de fer lithium lithium est plus privilégié pour les applications avec des exigences de sécurité plus élevées, comme dans les bus. Avec le développement des véhicules de tourisme entièrement électriques, les batteries au lithium ternaires occupent de plus en plus une position importante.
Les deux matériaux présentent des différences de densité énergétique et de coût, et différents véhicules et constructeurs automobiles font des choix différents. Selon les connaissances de Tucbol, le processus de production des deux matériaux est généralement similaire, mais les différences résident principalement dans l’utilisation et la proportion de matériaux, ainsi que dans des variations importantes de paramètres de processus spécifiques. L’équipement ne peut pas être partagé pour la production, et le coût de la simple mise à niveau ou de la commutation de la capacité de production est élevé (les matériaux ternaires ont des exigences strictes pour la déshumidification sous vide, qui n’étaient pas nécessaires pour les précédentes lignes de production de phosphate de fer lithium). Par conséquent, de nombreux fabricants de batteries planifient l’aménagement de leur capacité de production en déployant et en achetant simultanément des équipements pour les deux matériaux.