Description of the problem
The coating of lithium-ion battery electrodes mainly consists of two parts: coating and baking. The coating process determines key parameters such as coating width and coating amount, while the baking process has a significant impact on the electrode’s microstructure. Furthermore, the microstructure of the electrode greatly affects the battery’s wettability, adhesion, and the diffusion kinetics of lithium ions. One common defect in coating baking is the occurrence of cracks in the coating, especially in thick electrodes and water-based electrodes.
Theoretical analysis:
The main cause of cracking in electrode coatings during the baking process is capillary forces. When a wet coating containing suspended particles dries, initially all particles are suspended in the solvent (Figure 1a). As the solvent evaporates, the gas-liquid interface reaches the surface of the coating during baking (Figure 1b). The curved meniscus at the air-solvent interface between the particles generates capillary forces, exerting compressive forces on the particles perpendicular to the gas-liquid interface. With further baking, the gas-liquid interface penetrates into the interior of the coating, and the capillary forces increase as the solvent evaporates (Figure 1c), applying additional compressive forces on the particles. Eventually, the coating cracks at certain critical points to relieve the baking stress (Figure 1d).

Figure 1: Coating baking cracking process
The electrode has a maximum thickness without cracking, known as the critical cracking thickness. When the thickness is below the critical cracking thickness, the coating does not crack. However, when the thickness exceeds this critical value, the coating cracks. The estimation formula for the critical cracking thickness, denoted as hmax, is as follows:
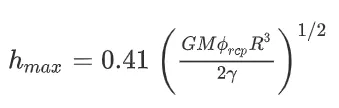
In the equation, G represents the shear modulus of the particles, M stands for the coordination number, φrcp denotes the volume fraction of randomly close-packed particles, R represents the particle radius, and γ represents the surface tension between the solvent and air.
Process Experience
(1)In lithium battery slurry, water is commonly used as a solvent for the negative electrode, while NMP (N-Methyl-2-pyrrolidone) is used as a solvent for the positive electrode. Due to the higher surface tension of water (72.80 mN/m, 20°C) compared to NMP (40.79 mN/m, 20°C), the baking process of aqueous slurry results in higher capillary pressure, making it more prone to coating cracking (Figure 2-5).
(2)In the preparation of a certain submicron lithium battery electrode, PVDF (Polyvinylidene fluoride) is used as a binder and NMP (N-Methyl-2-pyrrolidone) as a solvent. When the electrode thickness increases, even if the electrode is air-dried at room temperature and then vacuum-dried in a vacuum oven, cracking occurs. However, when the binder is switched to polyacrylamide, the electrode does not crack during baking. This indicates that the binder also has an influence on electrode cracking, as shown in Figures 3 and 5. The binder affects the surrounding environment of the particles, which may cause changes in the parameters M, φ, and γ in the equation, thereby affecting the tendency of electrode cracking.
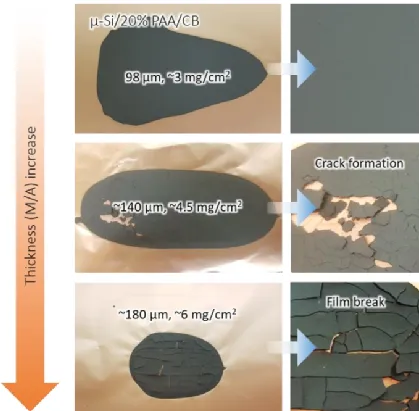
Figure 2 depicts the critical cracking thickness of the micro-sized Si/PAA/conductive agent composite electrode. In all electrodes, the composition of Si (2μm), PAA, and conductive agent is 80%, 10%, and 10%, respectively, with water as the solvent. No cracks are observed when the coating thickness is below approximately 100μm (coating areal loading of 3mg/cm2). However, when the coating thickness exceeds 140μm (coating areal loading of 4.5mg/cm2), cracks appear in the electrode.
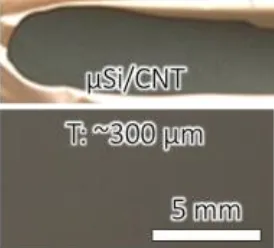
Figure 3 illustrates that when no binder is added to the electrode and CNT conductive agent is used to provide some cohesion, the critical cracking thickness of the silicon electrode is 300μm.
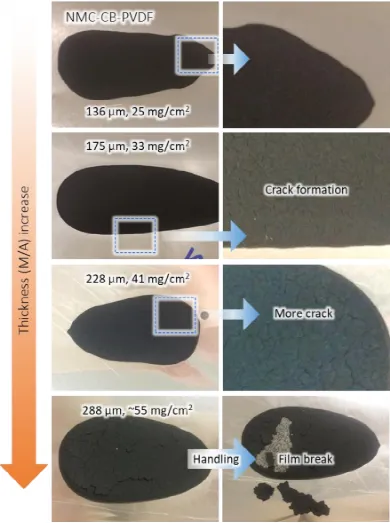
Figure 4 depicts the critical cracking thickness (175μm) of the nickel cobalt manganese (NMC)/PVDF/conductive agent composite electrode. The composition of NMC:PVDF:CB in the electrode is 90%, 5%, and 5%, respectively, with NMP as the solvent. When the electrode thickness is less than 175μm, no cracks are observed. However, thicker electrodes are more prone to cracking and delamination from the current collector.
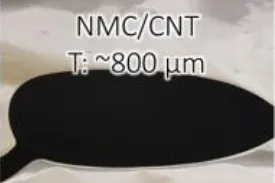
Figure 5 illustrates that when no binder is added to the electrode and CNT conductive agent is used to provide some cohesion, the critical cracking thickness of the ternary material electrode is 800μm.
Solution:
(1)Use a mixture of water/IPA (isopropyl alcohol, surface tension 23.00 mN/m, 20°C) as the solvent for the electrode slurry to reduce the surface tension, thereby avoiding cracking and improving electrode performance. The surface tension of the mixed solvent can be estimated using the following formula:

Where x1 is the molar fraction of water, x2 is the molar fraction of IPA. γ1 is the surface tension of water, and γ2 is the surface tension of IPA.
(2)Consider using NMP or other solvents with lower surface tension to prevent cracking. The surface tension can be characterized by measuring the contact angle between the solvent or a solution containing the binder and the substrate.

Figure 6 illustrates the gradual decrease in contact angle and surface tension from (a) to (d).
(3)Compaction can improve the quality of the coating, reducing the size of cracks. However, it cannot completely eliminate cracks (as shown in Figure 7).
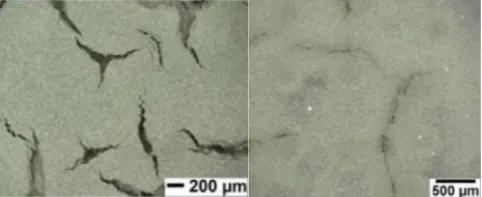
Figure 7 Comparison before (left picture) and after (right picture) electrode compaction
(4) Replace the binder to prevent cracking.