レーザーWエルディング
レーザー溶接には、深い溶け込み深さ、高速、変形の最小化など、多くの利点があり、パワーバッテリーの安全性を大幅に向上させることができます。レーザー溶接には、新エネルギー車や動力電池の製造に広く使用されているいくつかの利点があります。溶接環境に対する要件が低く、電力密度が高く、磁場の影響を受けず、導電性材料に限定されず、真空作業条件を必要としません。さらに、溶接プロセス中にX線を生成しません。
レーザー溶接技術は、パワーバッテリーの処理効率と溶接精度を大幅に向上させ、安全性、信頼性、一貫性を確保できます。また、コストを削減し、バッテリーの寿命を延ばします。
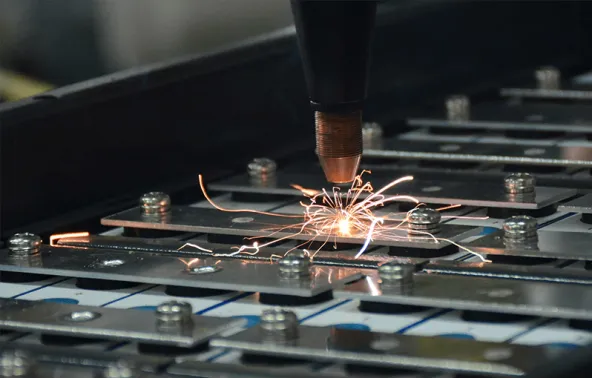
パワーバッテリーの製造では、レーザー溶接(関連マシン)は、バッテリーセルの組み立てプロセスとバッテリーパックのプロセスで使用されます。
1.バッテリーセルアセンブリセクション-ミッドセクション:セルアセンブリ段階でのレーザー溶接技術の適用には、セルケーシング、トップカバー、シーリングピン、およびタブ接続の溶接作業が含まれます。セル組み立て段階での特定のプロセスには、セルの巻線が含まれます。スタッキング、タブ溶接、ケーシングへのセル挿入、ケーシングトップカバー溶接、注射、および注入ポートのシーリング。セルはパワーバッテリーの最小単位であり、セルの品質がバッテリーモジュールの性能を決定し、それがパワーバッテリーシステムの全体的な信頼性に影響を与えます。
アルゴンアーク溶接や抵抗溶接などの従来の方法と比較して、レーザー溶接にはこのプロセスで大きな利点があります。
- 熱影響部が狭く、溶接変形が最小限に抑えられているため、特に微小部品の溶接に適しています。
- レーザー溶接は、レーザー光を光ファイバーに通すか、プリズムで偏向させることで、長距離にわたって行うことができます。
- レーザー溶接は非常に高いエネルギー密度を示します。
- レーザー溶接は、真空保護やX線遮蔽を必要とせず、磁場の影響を受けません。
2.後処理段階–最終段階:レーザー自動化システムは、モジュールパックの後処理段階で従来の手動組み立て方法に取って代わりつつあります。この段階での特定のタスクには、パックモジュールの形成、テストとグレーディング、および組み立てが含まれます。使用される主な機器には、フォーメーションマシン、容量検出デバイス、プロセス倉庫およびロジスティクスの自動化、およびパック自動化装置が含まれます。レーザー自動化システムは、バッテリーパックモジュールの組み立て中にタブ溶接を接続するためのモジュールパック組立ラインに広く適用されています。さらに、レーザーはモジュールカバーの防爆バルブの溶接にも使用できます。防爆バルブは通常、レーザー溶接を使用して特定の形状で溶接された2つのアルミニウム金属シートでできています。これらのバルブは、バッテリーの圧力が高くなりすぎると破裂して圧力を解放する溝で設計されています。防爆バルブとモジュールカバーの間のクリアランスが小さいため、それらを正確に配置することは困難です。したがって、レーザー溶接プロセスには、シームシーリングの確保や、溶接部の破壊圧力を一定範囲内に維持するための入熱制御など、厳しい要件があります。これらの要件を満たさないと、バッテリーの安全性に大きな影響を与える可能性があります。防爆バルブは通常、重ね溶接または複合溶接を使用して接合されます。レーザー溶接技術が進歩し続けるにつれて、レーザー溶接の溶け込み率は増加すると予想されます。
レーザー切断
レーザー切断技術は、加工タブ接続の切断と成形、電極シートの分割、セパレーターの分離など、リチウム電池の。型抜きと比較して、レーザー切断には、高精度、運用コストの低下などの利点があり、バッテリーの生産効率の向上とコスト削減に貢献できます。従来の機械的な切断方法とは対照的に、レーザー切断には、物理的な摩耗がない、柔軟な切断形状、エッジ品質の制御、精度の向上、運用コストの削減など、いくつかの利点があります。これらの利点は、製造コストの削減、生産効率の向上、新製品の型抜きサイクルの大幅な短縮に役立ちます。
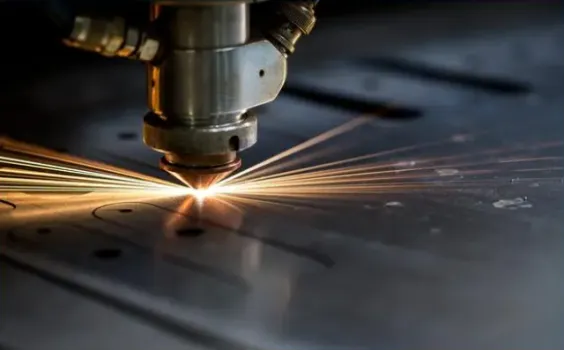
1.タブカット
レーザータブ成形は、その利点により主流の技術となっています。プロセスパラメータ、制御システム、およびカッティングステーションの設計によって、カッティングの速度と品質が決まります。従来、タブ成形には機械的な型抜きが主に使用されていました。しかし、機械的な型抜きには、金型の摩耗が激しい、金型交換時間が長い、柔軟性が低い、生産効率が低いなどの制限があります。リチウム電池製造の進化する要件を満たすことができなくなりました。
高出力、高ビーム品質のナノ秒レーザーとシングルモード連続ファイバー技術の開発により、レーザー切断は徐々にタブ成形の主流技術になりました。レーザータブ成形は、通常、連続ロールツーロール切断を採用しています。主なプロセスフローには、巻き戻し、張力制御、アライメント制御、レーザー切断、二次粉塵除去、巻き戻し(関連マシン).
2.電極シートの切断
電極シートを分割するには、サーキュラーディスクカット、ダイカット、レーザーカットの3つの主要な方法があります。サーキュラーディスクカットとダイカットはどちらも工具の摩耗の問題に悩まされており、プロセスの不安定性、切断電極シートの品質の低下、およびバッテリー性能の低下につながる可能性があります。レーザーエネルギーと切断速度は、切断品質に大きな影響を与える2つの重要なプロセスパラメータです。レーザー出力が低すぎたり、切断速度が速すぎたりすると、電極シートが完全に切断されない場合があります。一方、出力が高すぎたり、切断速度が遅すぎたりすると、材料上のレーザーの影響領域が大きくなり、切断寸法が大きくなります。
3.セパレーター切断
レーザー切断は、フリッピングローラー上の2つの交互のロールセパレーターコンポーネントによって形成されたセパレーターを切断するために使用されます。このプロセスにより、セパレーターの自動かつ均一な切断が可能になり、粉末の剥離、糸のピッキング、フィルムの断片化、不完全な切断などの問題を回避できます。この方法は、バッチ生産ラインでの使用に実用的です。
LアセールC傾いて
電極コーティング前のレーザー洗浄は、従来の湿式エタノール洗浄方法による損傷を効果的に回避できます。バッテリー溶接の前に、レーザークリーニングはパルスレーザーを使用して基板に熱衝撃と膨張を誘発し、汚染物質が表面の付着を克服して基板から剥離し、洗浄効果を実現します。バッテリーの組み立て時には、断熱ボードやエンドプレートにレーザークリーニングを適用して、セルの汚れた表面を洗浄し、セル表面を粗くし、接着剤やコーティング材料の接着性を向上させることができます。
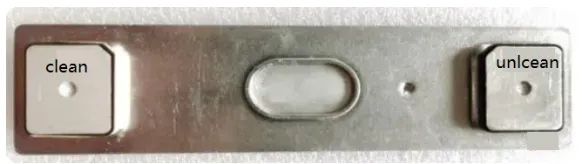
1.電極コーティング前:
リチウム電池の正極シートと負極シートは、金属箔にリチウム電池電極材料でコーティングされています。電極コーティングプロセスでは、金属箔を洗浄する必要があります。金属箔は通常、アルミニウムまたは銅でできています。従来のウェットエタノール洗浄方法では、リチウム電池の他のコンポーネントに損傷を与える可能性があります。レーザードライクリーニングマシンは、これらの問題に対処するための効果的なソリューションを提供します。
2.バッテリー溶接前
パルスレーザー放射を利用することで、ターゲットの表面温度を上昇させ、熱膨張につなげることができます。この熱膨張により、汚染物質または基板に振動が誘発され、汚染物質が表面の付着を克服して基板から剥離するため、表面の汚れが効果的に除去されます。この方法は、バッテリーセルの電極カラム端面から汚れ、ほこり、その他の汚染物質を除去し、溶接の準備をし、欠陥のある溶接の生成を減らすのに特に効果的です。
3.バッテリー組立時
リチウム電池の安全事故を防ぐために、電池セルに接着剤コーティングを施すのが一般的です。これは、予防するための断熱材として機能します短絡、回路を保護し、傷を防ぎます。断熱ボードとエンドプレートのレーザークリーニングは、バッテリーセルの汚れた表面を効果的にクリーニングし、セル表面を粗くし、接着剤またはコーティング材料の接着性を向上させることができます。レーザー洗浄は、洗浄プロセス後に有害な汚染物質を生成しないため、環境に優しく環境に優しい方法です。
レーザーマーキング
製品の品質をより適切に管理し、原材料情報、製造プロセスと手順、製品バッチ、製造日、メーカーの詳細など、リチウム電池の全生産情報を追跡するには、重要な情報をQRコード内に保存し、バッテリーにラベルを付ける必要があります。レーザーマーキングは、強力な耐久性、高い偽造防止能力、高精度、優れた耐摩耗性、信頼性の高い安全性の特性により、製品品質追跡に最適なソリューションを提供します。