Laser Welding
Laser welding has many advantages, such as deep penetration depth, high speed, and minimal deformation, which can significantly enhance the safety of power batteries. Laser welding has several advantages that make it widely used in the manufacturing of new energy vehicles and power batteries. It has low requirements for the welding environment, high power density, is not affected by magnetic fields, is not limited to conductive materials, and does not require a vacuum working condition. Additionally, it does not generate X-rays during the welding process.
Laser welding technology can greatly improve the processing efficiency and welding accuracy of power batteries, ensuring safety, reliability, and consistency. It also reduces costs and extends the service life of the batteries.
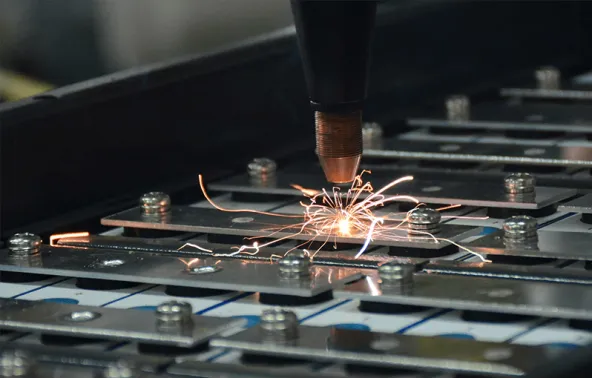
In the production of power batteries, laser welding(related machine) is used in the battery cell assembly process and battery pack process.
1. Battery cell assembly section-mid section:The application of laser welding technology in the cell assembly stage includes welding operations for the cell casing, top cover, sealing pins, and tab connections. The specific processes in the cell assembly stage include cell winding, stacking, tab welding, cell insertion into the casing, casing top cover welding,injection, and sealing of the injection port. The cell is the smallest unit of a power battery, and the quality of the cell determines the performance of the battery module, which in turn affects the overall reliability of the power battery system.
Compared to traditional methods such as argon arc welding and resistance welding, laser welding has significant advantages in this process:
- Narrow heat-affected zone and minimal welding deformation, making it particularly suitable for welding micro-components.
- Laser welding can be performed over long distances by guiding the laser beam through optical fibers or deflecting it using prisms.
- Laser welding exhibits extremely high energy density.
- Laser welding does not require vacuum protection or X-ray shielding and is not affected by magnetic fields.
2. Post-processing stage – Final stage: Laser automation systems are replacing traditional manual assembly methods in the module pack post-processing stage. Specific tasks in this stage include formation, testing and grading, and assembly of the pack module. The main equipment used includes formation machines, capacity detection devices, process warehousing and logistics automation, and pack automation equipment. Laser automation systems are widely applied in module pack assembly lines for connecting tab welding during battery pack module assembly. Additionally, lasers can also be used for welding explosion-proof valves on module covers. Explosion-proof valves are typically made of two aluminum metal sheets welded together with a specific shape using laser welding. These valves are designed with grooves that rupture and release pressure when the battery pressure becomes too high. Due to the small clearance between the explosion-proof valve and the module cover, it is challenging to accurately position them. Therefore, laser welding processes have strict requirements, including ensuring seam sealing and controlling the heat input to maintain the destruction pressure of the weld within a certain range. Failure to meet these requirements can significantly impact the safety of the battery. Explosion-proof valves are typically joined using lap welding or composite welding. As laser welding technology continues to advance, the penetration rate of laser welding is expected to increase.
Laser Cutting
Laser cutting technology can be applied in various processes during the manufacturing of lithium batteries, such as cutting and shaping tab connections, dividing electrode sheets, and separating separators. Compared to die-cutting, laser cutting offers advantages such as higher precision and lower operating costs, which can contribute to improving battery production efficiency and cost reduction. In contrast to traditional mechanical cutting methods, laser cutting has several advantages, including no physical wear, flexible cutting shapes, control over edge quality, higher accuracy, and lower operating costs. These advantages help reduce manufacturing costs, increase production efficiency, and significantly shorten the die-cutting cycle for new products.
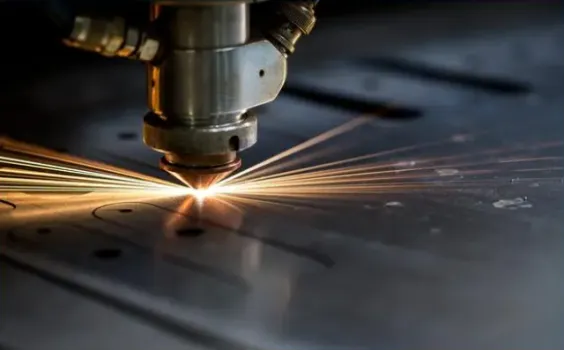
1. Tab cutting
Laser tab forming has become the mainstream technology due to its advantages. The process parameters, control system, and cutting station design determine the speed and quality of the cutting. In the past, mechanical die-cutting was primarily used for tab forming. However, mechanical die-cutting has limitations such as rapid mold wear, long mold replacement time, poor flexibility, and low production efficiency. It is no longer able to meet the evolving requirements of lithium battery manufacturing.
With the development of high-power, high-beam quality nanosecond lasers and single-mode continuous fiber technology, laser cutting has gradually become the mainstream technology for tab forming. Laser tab forming typically employs continuous roll-to-roll cutting. The main process flow includes unwinding, tension control, alignment control, laser cutting, secondary dust removal, and rewinding(related machine).
2. Electrode sheet cutting
There are three main methods for dividing electrode sheets: circular disc cutting, die-cutting, and laser cutting. Circular disc cutting and die-cutting both suffer from tool wear issues, which can lead to process instability, poor quality of the cut electrode sheets, and a decrease in battery performance. Laser energy and cutting speed are two crucial process parameters that have a significant impact on the cutting quality. When the laser power is too low or the cutting speed is too fast, the electrode sheet may not be completely cut through. On the other hand, if the power is too high or the cutting speed is too slow, the laser’s affected area on the material becomes larger, resulting in larger cut dimensions.
3. Separator cutting
Laser cutting is used to cut the separator formed by two alternating rolled separator components on a flipping roller. This process enables automated and uniform cutting of the separator, avoiding issues such as powder detachment, thread picking, film fragmentation, and incomplete cutting. This method is practical for use in batch production lines.
Laser Cleaning
Laser cleaning before electrode coating can effectively avoid damage caused by traditional wet ethanol cleaning methods. Prior to battery welding, laser cleaning uses pulsed laser to induce thermal shock and expansion in the substrate, causing contaminants to overcome surface adhesion and detach from the substrate, achieving a cleaning effect. During battery assembly, laser cleaning can be applied to insulation boards and end plates to clean the dirty surface of the cells, roughen the cell surface, and improve the adhesion of adhesive or coating materials.
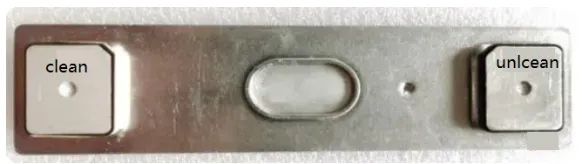
1.Before electrode coating:
The positive and negative electrode sheets of lithium batteries are coated with lithium battery electrode materials on metal foils. During the electrode coating process, it is necessary to clean the metal foils. The metal foils are typically made of aluminum or copper. Traditional wet ethanol cleaning methods can potentially damage other components of the lithium battery. Laser dry cleaning machines offer an effective solution to address these issues.
2.Before battery welding
By using pulsed laser radiation, the surface temperature of the target can be increased, leading to thermal expansion. This thermal expansion induces vibrations in the contaminants or the substrate, causing the contaminants to overcome surface adhesion and detach from the substrate, thus effectively removing surface stains. This method is particularly effective for removing dirt, dust, and other contaminants from the electrode column end faces of battery cells, preparing them for welding and reducing the production of defective welds.
3.During battery assembly
To prevent safety accidents in lithium batteries, it is common practice to apply adhesive coating to the battery cells. This serves as insulation to prevent short circuits, protect the circuits, and prevent scratches. Laser cleaning of insulation boards and end plates can effectively clean the dirty surface of the battery cells, roughen the cell surface, and improve the adhesion of adhesive or coating materials. Laser cleaning is a green and environmentally friendly method as it does not generate harmful pollutants after the cleaning process.
Laser Marking
To ensure better control of product quality and trace the entire production information of lithium batteries, including raw material information, production processes and procedures, product batches, manufacturing dates, and manufacturer details, it is necessary to store the key information within a QR code and label it on the battery. Laser marking offers the best solution for product quality tracking due to its characteristics of strong permanence, high anti-counterfeiting capability, high precision, excellent wear resistance, and reliable safety.