The term “battery pack” generally refers to the assembly and manufacturing of a lithium-ion battery pack. It involves the integration of battery cells, battery protection boards, battery connectors, label papers, and other components through battery pack processes to create the desired product for customers.
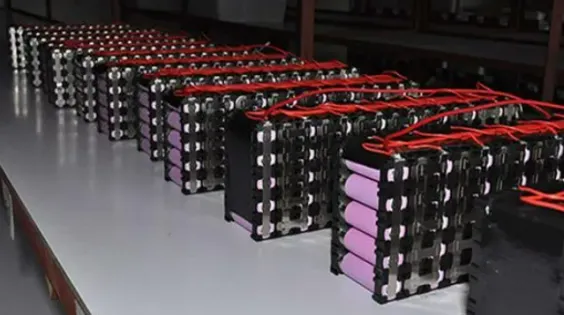
Battery pack manufacturing now predominantly focuses on lithium-ion battery pack factories, which have their own pack structural design, pack electronic design, and pack production workshops. They can independently develop and design battery packs according to customer requirements. Once the pack lithium-ion battery customization requirements are confirmed through battery methods, battery specifications, and battery samples, the pack production line in the workshop carries out production and processing. After passing quality inspection, the products are shipped out.
For energy storage power products, the key points of the lithium battery pack manufacturing process are as follows:
- Sorting and matching groups
Battery sorting refers to the selection of appropriate variables such as battery ohmic resistance, polarization resistance, open-circuit voltage, rated capacity, charge-discharge efficiency, self-discharge rate, etc. Through sorting, batteries are classified into groups based on their consistency in parameters. The main objective is to improve the internal consistency of batteries after grouping, thereby enhancing the efficiency and lifespan of battery modules.
Battery sorting methods mainly include single factor method, multi-factor method and dynamic sorting method.
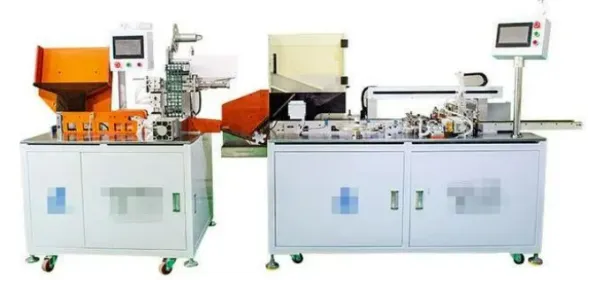
- A method of assembling lithium batteries, including the following steps:
Capacity testing of battery cells: Install the cells to be capacity sorted onto the testing equipment and perform charge-discharge cycles three times using the specified current. On the fourth cycle, charge the individual cell’s voltage to a percentage range set for the rated capacity.
Obtaining grouping reference benchmarks: Record the discharge capacity, constant current charging time, constant voltage charging time, and other parameters of the cells after the third cycle.
Cell capacity sorting: Based on the discharge capacity of the cell in the third cycle as the standard, the lower limit capacity is set, and cells with a capacity greater than the lower limit are selected as qualified cells;
Preliminary grouping of battery cells: Based on the obtained parameters of constant current charging time and constant voltage charging time, battery cells with qualified capacity and the same or similar constant current and constant voltage charging time parameters are matched;
Battery cell voltage drop: Store the assembled batteries in a set environment for a period of time to measure their discharge capacity. After determining the voltage drop qualification standards, select qualified batteries;
Final grouping of battery cells: Select the battery cells with qualified voltage drop, and use the cells with qualified voltage drop for final grouping.
- Assembly fixture for lithium battery cells, equipped with an automatic welding machine.
When assembling the battery cells using the fixture, it is important to follow the positive and negative electrode sequence specified in the Standard Operating Procedure (SOP) provided by the PE engineer. Reversing the sequence can result in a short circuit. Once the automatic welding machine program is properly set, the fixture is loaded with the battery cells, and the automated spot welding(related machine) process begins.
After the automated spot welding is completed, the quality inspection team needs to perform spot checks on the battery pack. Any missed or inadequate weld spots need to be re-welded to ensure proper connections.
- Lithium battery pack welding PCM/BMS
PCM or PCB (Protection Circuit Module or Circuit Board) is the “heart” of a lithium battery pack. It protects the lithium battery from overcharging, over-discharging, and short circuits, preventing battery pack explosions, fires, and damage.
For low-voltage lithium battery packs (<20 cells), a PCM with balancing functionality should be selected to maintain the balance and good lifespan of each cell. For high-voltage lithium battery packs (>20 cells), consideration should be given to using an advanced Battery Management System (BMS) to monitor the performance of each cell and ensure safer operation of the battery pack.
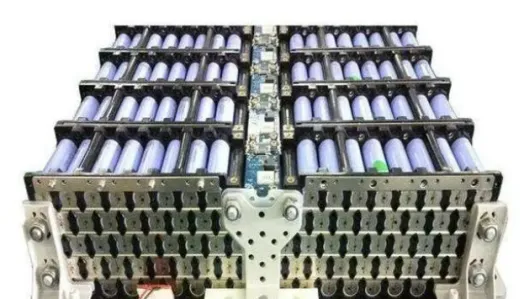
Employees must wear static wristbands to avoid damaging PCM/BMS due to static electricity.
There are different steps depending on the design of the battery pack. If the design involves PCM spot welding onto the battery pack, there is no need for soldering. Quality inspection is also required to check the spot welding points between PCM and the battery pack.
If soldering is required for PCM/BMS or for connecting screws to the pack, spot checks should be conducted on the soldering points and screw connections to ensure quality. For voltage collection wires, they should be connected in sequence from B-, B1… to B+ or soldered after removing the voltage collection wire plug. After soldering is completed, the collection plug should be tested for accuracy before connecting it to the BMS.
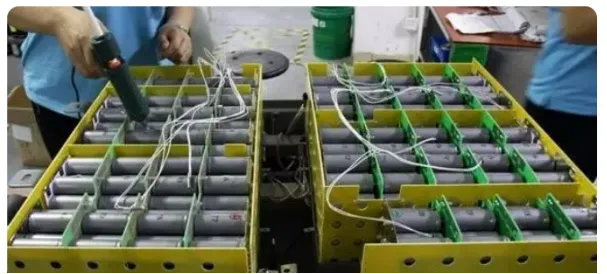
- Semi-finished product insulation
The voltage collection wires, conductors, and positive/negative output wires need to be properly secured and insulated. Commonly used materials for insulation include high-temperature adhesive tape,highland barley paper, epoxy boards, zip ties, etc. It is important to have safety awareness and avoid excessive pressure or stacking on the voltage collection wires or output conductors, as this can lead to damage and short circuits.
- Semi-finished product testing
After adding the BMS to the battery pack, a semi-finished product test can be conducted. Common tests include simple charge-discharge testing, pack internal resistance testing, pack capacity testing, pack overcharge testing, pack over-discharge testing, short circuit testing, and overcurrent testing. If there are special requirements, additional tests such as high-temperature and low-temperature testing, needle puncture testing, drop testing, salt spray testing, etc., may be necessary. It is important to note that special lithium battery pack testing can be destructive, so sampling is recommended.
Attention should be given to the battery pack’s endurance during these tests. For example, during pack overcharge testing, the BMS should be able to withstand high voltage. During short circuit testing, the BMS should be able to withstand high voltage and high current. During overcurrent testing, the BMS should be able to withstand pulse currents, and so on.
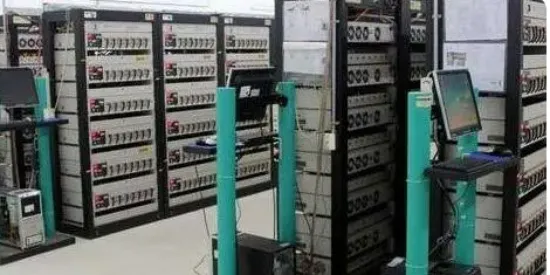
- Packing
This step also requires consideration of the design. However, before packing, it is essential to ensure the insulation of the signal acquisition wires and the positive and negative terminals of the battery pack.
For PVC-wrapped battery packs, a heat shrink machine is used. For battery packs sealed with ultrasonic technology, an ultrasonic sealing machine is employed. Battery packs with metal outer casings require assembly of the outer casing. Throughout this process, it is important to handle the battery pack with care, avoiding collisions and excessive pressure. The wires must be well insulated to prevent short circuits.
- Battery Pack Testing
The parameters of the entire set of testers are set, and the entire set of testers is tested on the battery pack.
Main test items: shipping voltage, internal resistance, simple charge and discharge.
Optional test items: overcurrent, short circuit.
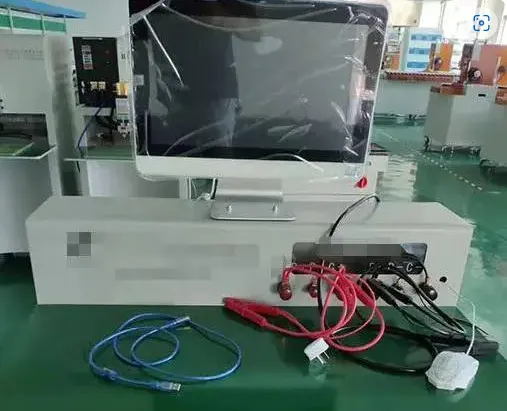
- Packing and shipping
Pack the boxes according to the size of the molded foam and do not place them randomly. When transporting the battery pack, you are most afraid of empty internal packing. Be sure to ensure there is enough foam inside for cushioning to avoid damage during transportation. Large battery pack, for safety reasons, you need to arrange for wooden frame to be shipped.
Above, all processes and quality must be tracked and controlled in place. Each position requires skilled employees to perform skilled work, ensuring quality while increasing speed.