calendering process for lithium battery electrode involves compacting a mixture of active material and conductive additives coated on a metal foil to form a uniform and dense electrode layer. The calendering process is carried out by applying pressure and control the calendering speed to ensure the electrode has sufficient density, thickness, and consistency.
1.The main purpose of lithium battery calendering:
The main purpose of lithium battery calendering is to uniformly press the mixture of positive materials and negative active materials, conductive agents, binders, etc. into sheets to ensure the uniformity, compactness and stability of the electrode sheets. The purpose of calendering includes the following aspects:
1.1 Increase electrode density: calendering process helps in tightly compacting the active materials, conductive additives, binders, and other components of the electrode sheets, thereby increasing its density. This is beneficial for enhancing the energy density and capacity of the battery.
1.2 Uniformize electrode sheets thickness: calendering process ensures a more uniform thickness of the electrode sheets, avoiding issues related to uneven thickness that may affect the stability of the battery performance.
1.3 Improve mechanical strength of the electrode sheets: calendering process enhances the mechanical strength of the electrode sheets, reducing the chances of fracture and deformation during fabrication, assembly, and usage.
1.4 Enhance electrode sheets conductivity: calendering process facilitates uniform distribution of conductive additives within the electrode sheets, thereby improving its conductivity and enhancing the battery’s charge/discharge performance.
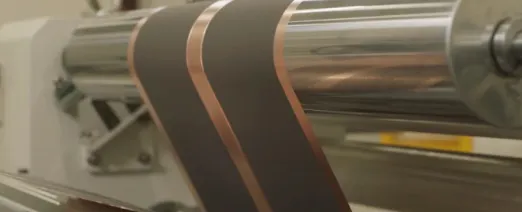
2.Calendering process parameter control
In the manufacturing of lithium batteries, the following aspects should be controlled during the calendering process of the positive and negative electrode sheets:
2.1 calendering temperature: Control the calendering temperature can affect the bonding between the battery sheet and the electrolyte layer and separator. The calendering process is typically conducted within a certain temperature range.
2.2 calendering pressure: Appropriate calendering pressure ensures a tight bond between the battery sheet and the electrolyte layer/separator. However, excessive pressure may cause deformation or damage to the battery sheet.
2.3 calendering speed: The control of calendering speed is also an important factor to consider during the calendering process. A suitable calendering speed ensures the uniformity of the composite process.
3.Common issues in the calendering process:
3.1 Uneven electrode thickness: This may be caused by uneven calendering pressure or unstable calendering speed of the calendering equipment.
3.2 Uneven transverse thickness: This may be caused by misalignment of the rollers or uneven surface of the rollers.
3.3 Uneven longitudinal thickness: This may be caused by uneven calendering pressure or unstable calendering speed of the rollers.
3.4 Electrode sheets curling: This may be caused by uneven calendering pressure or uneven surface of the rollers.
3.5 Wave-like edges on the electrode sheets: This may be caused by uneven calendering pressure or unstable calendering speed of the rollers.
3.6 Dark streaks on the electrode sheets surface: This may be caused by uneven surface of the rollers or unstable temperature of the rollers.
3.7 Edge curling of the electrode sheets: This may be caused by uneven calendering pressure or unstable calendering speed of the rollers.
3.8 Broken strips on the electrode sheets: This may be caused by excessive calendering pressure or unstable calendering speed of the rollers.
4.Solutions
4.1Uneven electrode sheets thickness:
(1) Adjust the parameters of the calendering equipment to ensure even distribution of calendering pressure across the entire electrode sheets surface.
(2)Check the wear of the rollers and replace the severely worn rollers if necessary.
4.2 Uneven electrode sheets thickness:
(1) Adjust the parameters of the calendering equipment to ensure even distribution of calendering pressure across the entire electrode surface.
(2)Check the wear condition of the rollers and replace heavily worn rollers if necessary.
4.3 Uneven longitudinal thickness:
(1) Adjust the parameters of the calendering equipment to ensure even distribution of calendering pressure across the entire electrode sheets surface.
(2) Check the wear condition of the rollers and replace heavily worn rollers if necessary.
4.4 Electrode sheets curling:
(1) Check the installation of the rollers to ensure parallel alignment. Use measuring tools to make necessary adjustments.
(2) Grind the surface of the rollers to ensure a smooth surface.
4.5 Wave-like edges on the electrode sheets:
(1) Adjust the parameters of the calendering equipment to ensure even distribution of calendering pressure across the entire electrode sheets surface.
(2) Check the wear condition of the rollers and replace heavily worn rollers if necessary.
4.6 Dark streaks on the electrode sheets surface:
(1) Grind the surface of the rollers to ensure a smooth surface.
(2) Adjust the temperature of the rollers to ensure stable temperature.
4.7 Edge curl on the electrode sheets:
(1) Adjust the parameters of the calendering equipment to ensure that the calendering pressure is evenly distributed on the entire electrode sheets surface.
(2) Check the wear of the rollers and replace the seriously worn rollers if necessary.
4.8 Broken on the electrode sheets:
(1) Adjust the parameters of the calendering equipment to ensure that the calendering pressure is moderate and not too high.
(2) Check the wear of the rollers and replace the seriously worn rollers if necessary.
By implementing the above measures, the issues encountered during the calendering process of lithium battery electrode sheets can be effectively resolved, ensuring consistent and stable electrode sheets quality. It is also important to adjust and maintain the calendering equipment according to the specific situation to ensure its proper functioning and stability.